The Air Slide Conveyor is widely used for pneumatic conveying of dry powder materials, especially in the cement industry for transporting cement and raw meal. Compared to screw conveyors and belt conveyors, the Air Slide Conveyor has no moving parts, is easy to maintain, has good sealing, operates quietly, and ensures safe and reliable operation. It also allows for easy direction changes and multi-point feeding and discharging. However, improper installation, operation, and maintenance can lead to blockage in the Air Slide Conveyor.
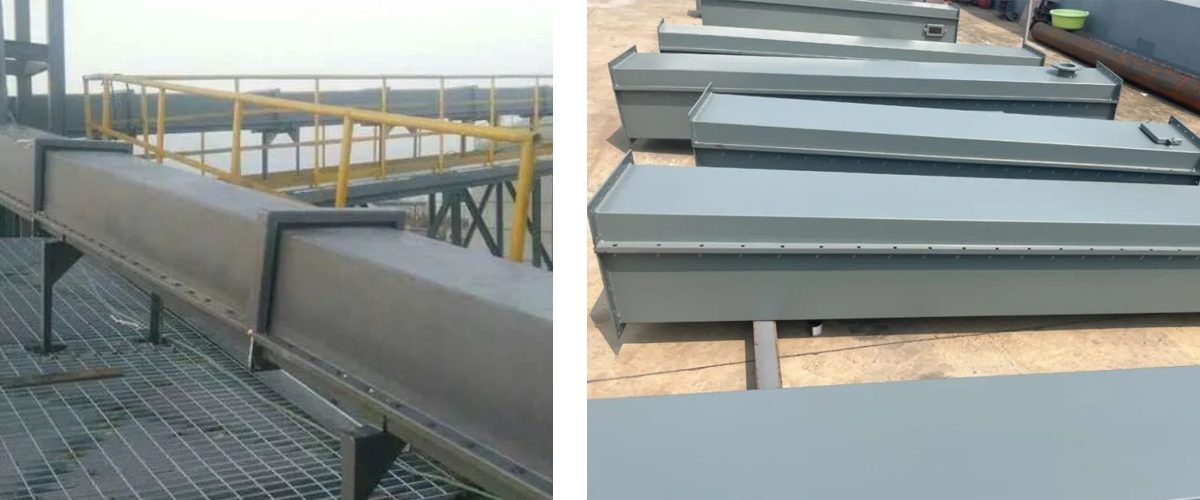
1. Causes of Conveyor Blockage
1.1 High Material Moisture
High moisture content in materials reduces the air permeability of the conveyor, leading to blockage.
1.2 Incomplete Slag Removal
If the slag is not adequately removed before the raw meal enters the storage, iron slag and small particles may accumulate in the conveyor, hindering airflow and causing blockage.
1.3 Broken Perforated Plates
If the perforated plates inside the conveyor are broken, air can leak through gaps, forming air columns that accumulate material and lead to blockage.
1.4 Poor Sealing
If the conveyor is not well-sealed, excessive air leakage may prevent proper material fluidization, resulting in blockage.
1.5 Improper Installation Angle
If the conveyor’s installation angle is too small, the material flow speed decreases. Sudden changes in material properties or airflow can cause blockage.
1.6 Material Condensation
After shutdown, if material remains in the conveyor and cools down, condensation may occur, making the material sticky and difficult to flow.
1.7 Delayed Exhaust
If the exhaust from the conveyor is delayed, trapped air can exert downward pressure on the material, preventing it from flowing freely and causing blockage.
2. Solutions for Conveyor Blockage
When blockage occurs in an Air Slide Conveyor, immediately stop the system and clean it. Identify the cause and implement the following measures:
2.1 Material-Related Solutions
- Reduce Moisture: Ensure that the moisture content of incoming materials is below 50°C and stop the cooling water.
- Control Water Spray: Limit the water spray inside the mill to no more than 2% of the mill’s output.
- Pre-Dry Materials: Pre-dry materials with high moisture content before milling.
- Regular Inspections: Check for loose bolts during external water spraying and tighten them as needed.
- Proper Operation: Start the Air Slide Conveyor a few minutes before starting the mill.
- Handle Slag Properly: If the milled material contains a lot of slag, remove it to prevent entry into the conveyor.
- Clean Before Shutdown: Clean the conveyor of materials before shutting down; start the conveyor a few minutes before feeding materials to avoid condensation issues.
2.2 Chute-Related Solutions
- Install Alarm Devices: Place automatic alarm devices at the conveyor’s feed end to close the feed port or stop the system in case of blockage.
- Regular Monitoring: Frequently check the conveyor’s working condition and address any abnormalities promptly.
- Replace Broken Plates: Replace broken perforated plates in a timely manner. Look for “bubbling” in the material to identify issues.
- Seal Air Leaks: Use sealing materials like graphite rope or rubber to fix leaks in the conveyor.
- Set Locking Devices: Install locking devices at the conveyor’s feed end to maintain stable airflow.
- Pressure Measurement: Install pressure measurement devices at intervals along the conveyor to monitor pressure changes.
- Exhaust Pipe Setup: Set up exhaust pipes or bag filters at the conveyor’s tail to ensure timely removal of trapped air.
By implementing these measures, you can effectively reduce blockage in Air Slide Conveyors and improve the system’s efficiency and reliability.For more information or technical support, please feel free to contact us. We are here to assist you!