During operation, high exhaust gas temperatures in boiler dust collectors are a common issue. This not only affects dust collection efficiency but may also damage the equipment. To ensure the stability and safety of the boiler system, it is crucial to implement timely cooling measures. This article will introduce several effective methods for lowering exhaust gas temperatures.
1. Add Cooling Devices
Install Coolers
Installing coolers serves as an effective method to reduce exhaust gas temperatures. By using cold air or cold water on the gas pipes, you can significantly lower the gas temperature and ensure the system operates normally.
Directly Inject Cold Air
Another straightforward cooling method involves directly injecting cold air into the exhaust gas. However, you must precisely control the temperature and airflow to prevent excessive cooling, which can lead to condensation and block the dust collection bags.
Direct Water Cooling
You can also achieve cooling by spraying water directly into the exhaust gas, utilizing the principle of evaporation to absorb heat. However, it is essential to manage the water spray volume to avoid dust agglomeration or pipe blockage.
Indirect Water Cooling
Using an indirect water cooling method allows you to cool high-temperature exhaust gas through the cooling pipes, ensuring a stable temperature decrease.
2. Use Air-Cooling Valves
Installing adjustable air-cooling valves before the bag filter effectively controls exhaust gas temperatures. One end of the valve connects to the high-temperature pipe, while the other end communicates with the atmosphere. This system automatically adjusts the amount of air drawn in, maintaining the exhaust gas temperature within a safe range.
3. Adjust Boiler Operating Parameters
Adjusting the boiler’s operating parameters is another effective way to lower exhaust gas temperatures. You can check and adjust the boiler load and excess air levels to decrease flue gas temperatures. Additionally, examining the moisture content of the coal and making appropriate adjustments can optimize the combustion process.
4. Optimize the Use of Dust Collection Bags
Ensure the initial layer thickness on the surface of the dust collection bags is sufficient to reduce the risk of bag damage due to high-temperature exhaust gas. For newly replaced bags, perform pre-coating with dust to prevent high-temperature gases carrying sparks from directly contacting the bags.
5. Add Fire Barriers
Adding fire barriers or other technical measures before the dust collector can effectively prevent high-temperature embers and unburned materials from entering the bag filter, thereby reducing the risk of equipment damage.
6. Utilize Natural Cooling Methods
In certain situations, you can employ natural cooling methods. By increasing the length of the dust-carrying gas pipes, you can leverage natural convection and radiation heat dissipation with the surrounding air to cool the gases.
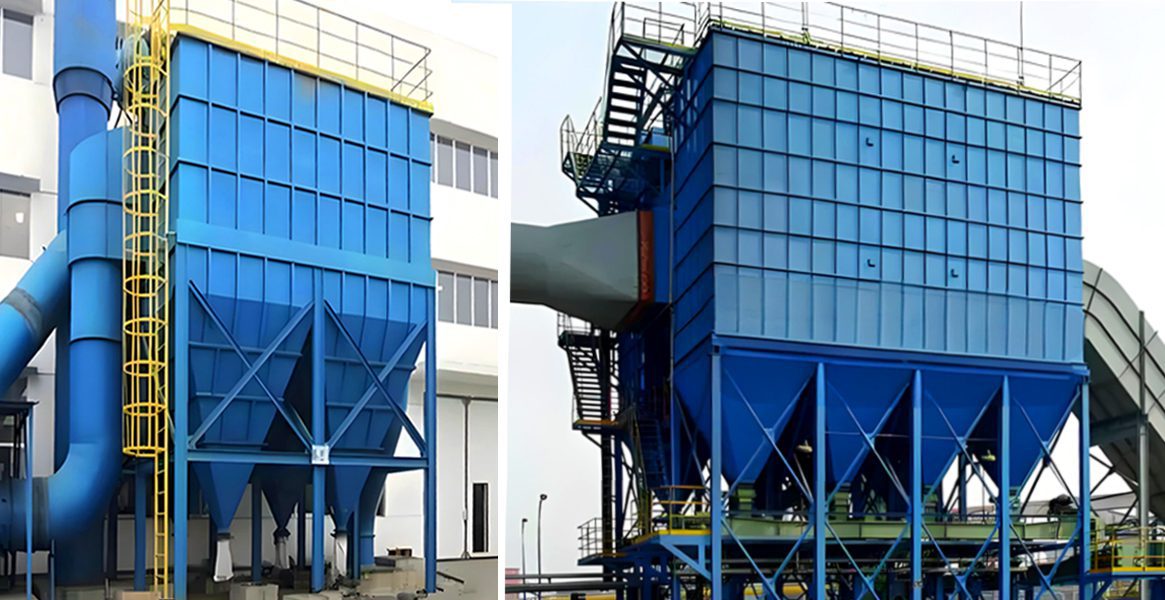
Conclusion
When addressing high exhaust gas temperatures in boiler dust collectors, it is essential to consider various factors to ensure that the cooling measures are effective and safe. This approach will help avoid negative impacts on the performance and efficiency of the dust collector. By implementing reasonable cooling strategies, you can enhance the operational efficiency of the dust collector and extend the equipment’s lifespan, thereby ensuring the stable operation of the boiler system.
For further information on related solutions or to seek professional advice, please contact us.