A company operates six cement storage silos. These silos feature a cylindrical steel and concrete structure. Each silo has a specification of ф18m×45m and can hold up to 10,000 tons of various types of cement according to market demand. The cement grinding system uses a combined grinding mode of “roller press + ball mill.” The company offers both bagged and bulk shipping options.
Overview of Cement Caking Issues
During cement shipping and clearing, the company identified varying degrees of wall caking and cement caking in the silos. In some cases, the wall caking exceeded 0.5 meters. When the silos discharge, the cement often falls in large pieces and blocks the discharge outlet. This blockage interrupts the shipping process and requires clearing before resuming operations. During peak shipping seasons, caking reduces loading efficiency and affects customer satisfaction with cement quality.
The storage space is pretty tight, and the setup is quite complicated.Narrow access passages create risks of falling objects, high dust levels, oxygen deficiency, mechanical injuries, and electrical hazards. These conditions can really put workers’ health and safety at risk.Some cement plants have started using machines for clearing instead of relying on manual methods. However, this change can really drive up their operating costs.
To reduce wall caking and cement caking during discharge, the company analyzed the causes and implemented targeted measures across various stages, including storage, transportation, grinding operations, management, and discharge control. These measures have achieved positive results.
Analysis of Cement Caking Causes
Cement is a hydraulic binding material. Its hydration characteristics are the main reason for caking in storage. Ideally, lower moisture content in cement is preferable. However, high moisture levels often result from excess moisture in mixed materials and water introduced during production and transportation. To keep cement from clumping together, it’s really important to manage moisture levels while making and transporting it, store it properly, and treat the walls of silos to prevent caking.
Common Problems and Production Measures
The cement production process includes various stages: material storage, batching and transportation, grinding systems, product transportation, silo tops, interiors, bottoms, and discharge. Below are common issues and corresponding production measures for each stage:
1. Material Storage Problems
- Outdoor Storage: Ensure mixed materials are stored indoors to reduce moisture through natural drying.
- Design Deficiencies: Use a zone-based stacking strategy and implement a first-in, first-out system to maintain material quality.
- Raw Material Quality Control: Strictly monitor the quality of incoming materials to prevent substandard materials from entering.
2. Batch Transportation Problems
- Rain Protection: Ensure the sealing of transportation corridors and dust collection systems to prevent rainwater leakage.
- Air Moisture Control: Regularly clean oil-water filters and drain water from air storage tanks.
3. Grinding System Problems
- Cold Air Valve Design: Install rain covers to prevent water ingress.
- Moisture Control: Adjust the mixture of materials according to seasonal climate conditions to keep finished cement moisture ≤0.5%.
4. Finished Product Transportation Problems
- Sealing of Transport Chutes: Ensure the transportation system is sealed to prevent moisture entry.
- Dust Collection System Check: Regularly inspect the sealing of the dust collection system to ensure optimal performance.
5. Silo Top Problems
- Waterproofing Measures: Regularly check and repair waterproofing facilities on the silo tops.
- Negative Pressure Control: Maintain the negative pressure of the dust collector on top of the silo within a reasonable range to prevent caking.
6. Silo Interior Problems
- Storage Time Management: Reduce storage amounts in winter to avoid prolonged storage.
- Caking Issues: Use new materials like nano-ceramic anti-corrosion membranes to minimize wall adhesion.
7. Silo Bottom Problems
- Electric Ball Valve Malfunctions: Conduct regular maintenance to ensure proper operation and prevent dead zones.
- Chute Inspection: Promptly replace damaged tarpaulins to ensure smooth transportation.
8. Discharge Problems
- Adding Lump Breakers: Install lump breakers below discharge gates to break up caked cement into smaller chunks for smooth transport.
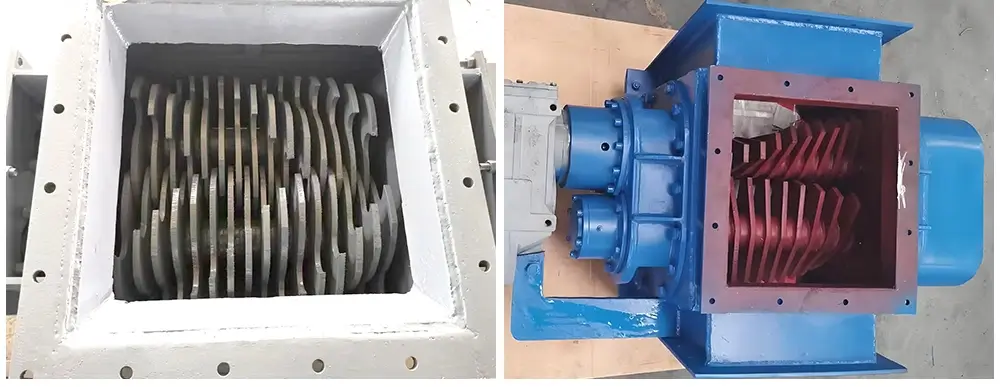
Conclusion
By implementing these targeted measures, the company significantly reduced cement caking in storage. They did a great job managing moisture in different materials, improved the design for rain protection, and used silos that can handle high discharge rates. These efforts ensured the smooth discharge of cement. In recent years, the frequency of caking incidents has decreased dramatically, ensuring efficient production and enhancing market competitiveness.
For more information or support, please contact us.
The Darko team looks forward to providing you with high-quality products and services.