Filter bags are really important for controlling dust in different industries.However, fire incidents involving these bags often occur. These incidents can result in big financial losses and create safety risks for staff, not to mention disrupt production.Therefore, understanding the causes of filter bag fires is essential for developing effective preventive measures and ensuring industrial safety.
What is a Filter Bag?
A filter bag is a device used for filtering gases or liquids. It is typically made of multiple layers of fiber material designed to capture suspended particles. These bags are widely used in industries, environmental applications, and households, effectively improving the cleanliness of air or liquids. Filter bags are primarily used in industrial dust collection systems to filter dust and particles, protecting equipment and improving work environments.
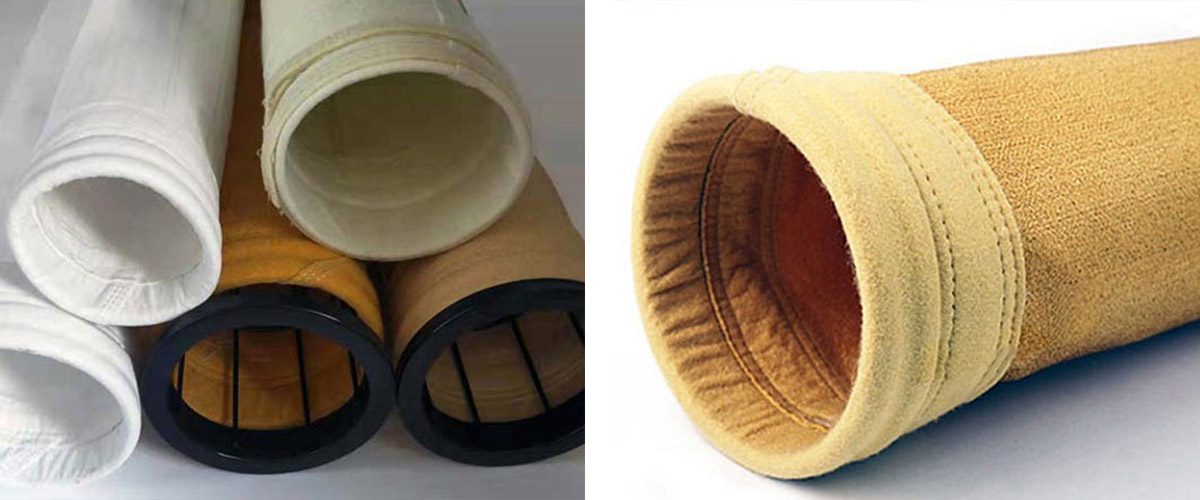
The Impact of High Temperature on Filter Bag Fires
High Inlet Gas Temperature
In industries such as metallurgy, cement, and power generation, the temperature of the gas entering filter collectors is often high. When this temperature exceeds the tolerance limit of the filter bag material, the fiber structure can be quickly damaged. For example, polyester bags can typically withstand continuous temperatures of 130-150°C. Staying in really hot temperatures for a long time can make the material much weaker and raise the chances of a fire. If sparks or high-temperature sources come into contact with such bags, combustion is likely.
Localized Overheating
In addition to high overall inlet temperatures, localized overheating can occur in certain areas of the bags. This may happen due to uneven airflow distribution or poor heat exchange. For instance, poorly designed internal structures can lead to excessive airflow in specific regions, causing localized temperature spikes. If the cleaning system isn’t working right, it can overheat, which lets dust pile up on the bag. This can be a serious fire risk. can lead to overheating, allowing dust to accumulate on the bag’s surface and creating a fire hazard.
The Relationship Between Accumulated Combustible Materials and Filter Bag Fires
Dust Characteristics and Self-Ignition Potential
Different types of industrial dust have varying physical and chemical properties. Some dusts exhibit strong self-ignition tendencies, such as coal dust and certain metallic powders. Under specific conditions, these dusts can undergo oxidation and release heat, raising their temperature to the ignition point. When gases containing such self-igniting dust pass through the filter bag, even in the absence of an external flame, the accumulation of dust can trigger self-ignition.
Dust Accumulation Due to Ineffective Cleaning
Keeping the cleaning system in good shape is really important for making sure that the filter bag works well. If the cleaning is ineffective, dust can gradually accumulate, forming thick layers on the bag surface. This not only increases filtration resistance but also generates heat from oxidation reactions. Over time, this accumulated heat can ignite the dust, leading to a fire in the filter bag.
The Role of Static Electricity in Filter Bag Fires
Mechanisms of Static Electricity Generation
During the dust collection process, friction and collisions between dust particles and the bag surface can generate static electricity. This is especially pronounced when handling dry, fine dust. In some chemical industries, the insulation of materials can prevent charge leakage, allowing static charges to accumulate on the bag’s surface.
Ignition from Static Discharge
When static electricity accumulates to a certain level, it can discharge. This energy, while relatively small, can ignite nearby combustible materials under certain conditions. If flammable dust or gases are present on the filter bag surface, static discharge can become a potential ignition source. Even small sparks can ignite combustible mixtures instantly.
Fire Risks from Equipment Failures
Mechanical Wear and Tear
Over time, filter bags experience wear from airflow, dust abrasion, and mechanical friction. This wear can lead to damage, making the bags more susceptible to fire. In pulse-jet filter collectors, regular bursts can really take a toll on the bag openings. Over time, this can cause them to rupture, which means the clean inside of the bag gets exposed to hot impurities.
Electrical Failures and Spark Generation
Electrical system failures are another big reason filter bag fires happen.Issues such as motor overloads, short circuits, and loose connections can generate heat or sparks. In environments containing flammable gases or dust, these sparks can ignite nearby combustible materials, leading to a fire in the filter bag.
Conclusion and Preventive Measures
Conclusion
In summary, filter bag fires result from a complex interplay of factors, including high temperatures, accumulated combustible materials, static electricity discharge, and equipment failures. Recognizing these risk factors is essential for effectively implementing preventive measures to reduce the likelihood of fire incidents.
Preventive Recommendations
1.Temperature Control
- Install reliable temperature monitoring devices to continuously track the inlet gas temperature, integrating them with control systems.
- Optimize production processes to lower gas temperatures at the source, using efficient heat recovery techniques.
2.Combustible Material Management
- Implement strict classification and handling protocols for self-igniting dusts, including inert gas protection measures.
- Regularly maintain the cleaning system to ensure effective dust removal and keep the dust layer thickness moderate.
3.Static Electricity Protection
- Use static elimination devices to reduce the risk of charge accumulation.
- Select filter bag materials with good anti-static properties and design systems to minimize static generation opportunities.
4.Equipment Maintenance and Inspection
- Establish a regular maintenance schedule to check for wear and damage in the filter bags, addressing potential hazards promptly.
- Strengthen the maintenance of electrical systems to ensure safe operation.
By implementing these comprehensive measures, industries can significantly reduce the risk of filter bag fires, ensuring safe and stable operations. Future research should continue to explore new technologies and methods to enhance the fire resistance of filter bags and improve the safety of industrial dust handling.
For more information or inquiries, please feel free to contact us. We look forward to assisting you.