Introduction to Double Dump Valves
Double dump valves (also known as dual-flap valves أو twin gate discharge valves) are essential components in powder and granular material handling systems. Widely used in cement plants, food processing, and metallurgy industries, these valves excel in:
✔ Make sure air doesn’t escape in pneumatic expressing systems.
✔ Ensuring continuous material flow control
✔ Providing airtight sealing for dust collection
1. Core Working Principle of Double Dump Valves
1.1 Basic Structure
Every double dump valve contains three critical components:
Upper and lower valve flaps (typically made of wear-resistant steel)
Heavy counterweight mechanism (for automatic flap reset)
Sealing gasket (usually food-grade rubber or PTFE)
1.2 Material Flow Process
The patented alternating flap system operates in 4 stages:
Upper flap opens – Material enters the intermediate chamber
Upper flap seals – Creates an airlock to prevent pressure loss
Lower flap discharges – Material exits by gravity
Lower flap resets – Counterweight ensures complete closure
Key Benefit: This sequential operation maintains constant system pressure while allowing uninterrupted material transfer – a critical advantage over rotary valves in high-pressure systems.
2. Electric Double Dump Valve Operation
2.1 Key Components
Part | Function |
---|---|
IP65-rated actuator | Weatherproof electric motor drive |
Chain/belt transmission | Converts rotary to linear motion |
Position sensors | Provides open/close feedback to PLC |
2.2 Working Cycle
Opening Sequence:
① Motor energizes → ② Gearbox rotates shaft → ③ Upper flap opens (0-90°) → ④ Time delay (2-5 sec) → ⑤ Lower flap opens
Closing Sequence:
① Lower flap seals → ② Upper flap closes → ③ Limit switch signals completion
Pro Tip: Electric models achieve <0.5% leakage rates when paired with inflatable seals for abrasive materials like fly ash.
3. Pneumatic Double Dump Valve Mechanism
3.1 Air Cylinder Operation
Single-acting cylinders (spring return) for compact installations
Double-acting cylinders for high-speed cycling (up to 60 cycles/minute)
3.2 Critical Sealing Technology
إن cone-and-spring sealing system provides:
Primary seal: Metal-to-metal contact between flap and seat
Secondary seal: Compressible elastomer gasket (FDA-approved options available)
Industry Application: Particularly effective in explosive environments (ATEX Zone 22) where electric sparks must be avoided.
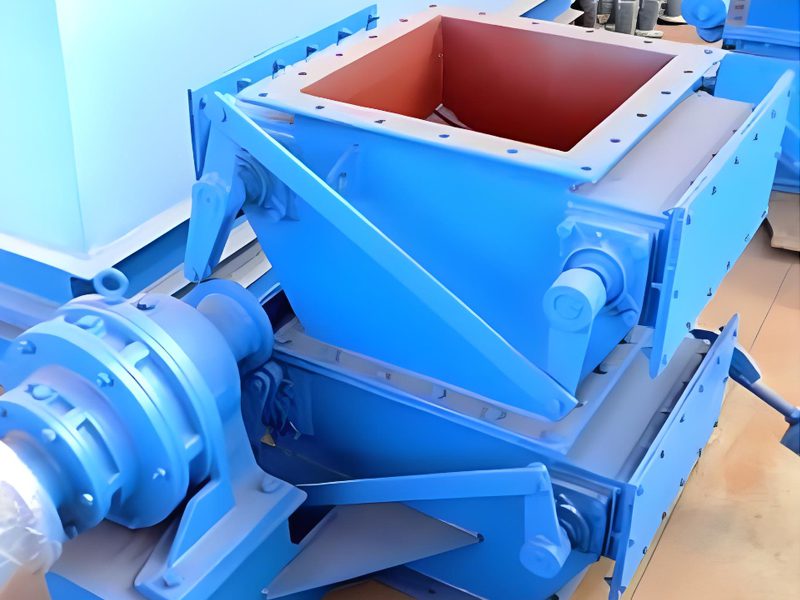
Comparative Analysis: Electric vs Pneumatic
الميزة | Electric | Pneumatic |
---|---|---|
Response Time | 3-10 seconds | <1 second |
الصيانة | Annual lubrication | Quarterly diaphragm checks |
استخدام الطاقة | 0.5-2 kW | 4-6 CFM @ 80 psi |
Best For | Precise positioning | Rapid cycling |
Troubleshooting Common Issues
Problem 1: Material bridging
الحل: التثبيت vibrators أو air cannons on valve body
Problem 2: Seal degradation
Diagnosis: Check for excessive play in linkage arms (>3mm indicates wear)
Problem 3: Incomplete closure
إصلاح: Adjust counterweight position or increase cylinder pressure by 10%
Industry-Specific Applications
✔ Cement Plants
Handles clinker dust at 300°C with water-cooled bearings
✔ Food Processing
316 stainless steel models with sanitary clamps meet USDA standards
✔ Power Generation
Explosion-proof versions for coal fly ash collection
FAQs (Featured Snippet Optimization)
Q: How often should double dump valves be maintained?
A: Perform visual inspections weekly و complete overhaul every 2,000 operating hours
Q: Can double dump valves handle sticky materials?
A: Yes, when equipped with Teflon-coated flaps و air purge connections
Q: What's the typical lifespan?
A: 5-7 years for standard models, 10+ years with hardened alloy components
Technical Specifications Table
Parameter | Range |
---|---|
Sizes | 4″ to 24″ diameter |
درجة الحرارة | -40°F to 750°F |
الضغط | Up to 15 PSI (standard) |
المواد | Cast iron, SS304, SS316, AR steel |
For double dump valve selection consultation or technical support, please contact us.