In cement production, the cooling process is critical to ensuring product quality and performance. Two primary methods are used: online cooling and post-storage cooling. Post-storage cooling, with its wide cooling range and precise temperature control, is ideal for applications requiring strict thermal management. To maximize efficiency and equipment longevity, several key factors must be addressed during implementation.
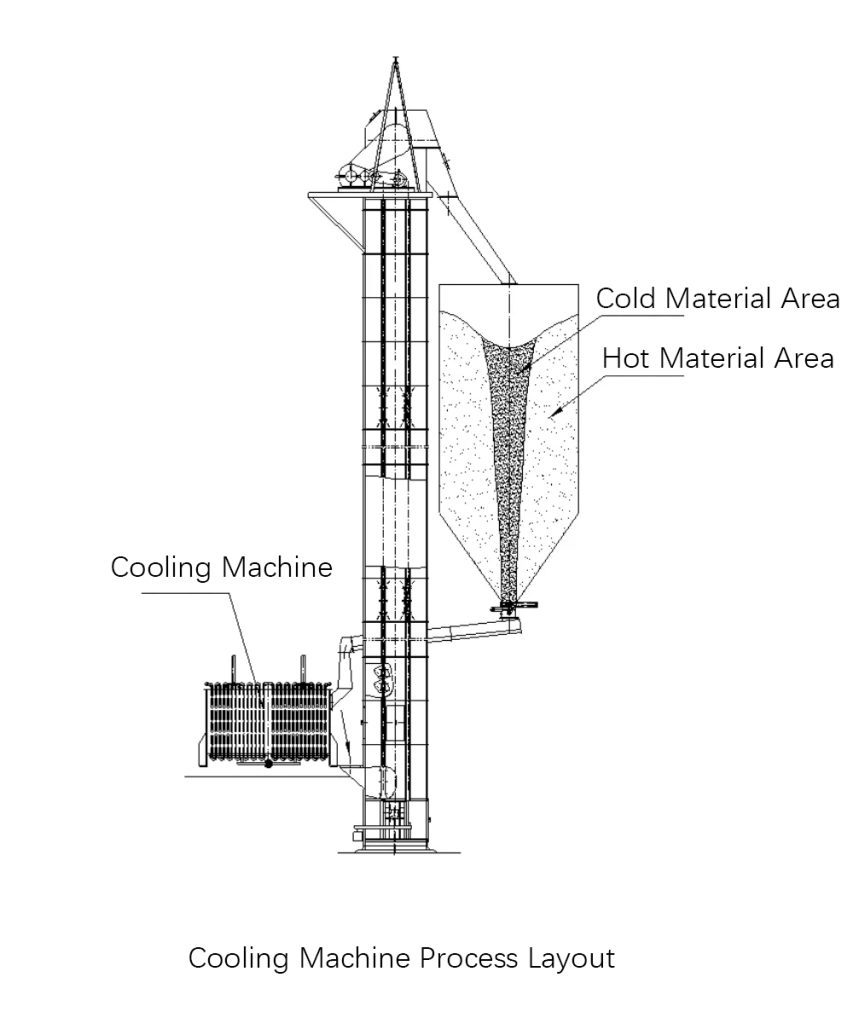
1. Overcoming Local Cooling Inefficiencies
In a single-silo cooling process, cement exits the silo, passes through the cooler, and returns via an elevator. However, this can lead to uneven cooling—while the cooler’s discharge temperature meets standards, the silo’s output material may remain too hot. This occurs due to material flow channeling, where only a portion of the cement circulates, leaving the rest insufficiently cooled.
Solution:
Adopt a dual-silo cooling process. Cement from Silo A passes through the cooler into Silo B. If temperatures remain high, the material can cycle back to Silo A for further cooling. This method ensures uniform temperature distribution and compliance with quality standards.
2. Preventing Cement Caking in Silos
Temperature fluctuations during storage often cause cement to cake on silo walls, particularly in steel silos. As the cement level drops, chunks may dislodge and enter the cooler, risking mechanical blockages or equipment damage.
Solution:
Install pre-cooler de-caking devices to break up clumps before they reach the cooler.
Add inspection ports for regular maintenance and removal of caked material.
3. Avoiding Expansion Box Issues
When cement overfills the cooler housing, mechanical action can cause material expansion, leading to housing deformation, blockages, or part failures. This typically happens when silo discharge rates exceed cooler or elevator capacity.
Solution:
Use flow-stabilizing feeders under the silo to regulate discharge rates and prevent system overload.
Conclusion: Optimizing Cement Cooling for Quality & Efficiency
Proper cooling process design and maintenance are essential for high-quality cement production. By addressing local cooling imbalances, caking, and expansion risks, manufacturers can enhance efficiency and extend equipment life.
Need expert advice on cement cooling solutions?
Contact us today for tailored support and industry-leading expertise!