The cement production process continually seeks innovation and optimization. The introduction of a 7-stage cement kiln preheater raises important questions. What does this change mean? What opportunities and challenges will it bring to cement enterprises?
I. Advantages of the 7-Stage Cement Kiln Preheater
(A) Significant Energy Savings
The 7-stage cement kiln preheater increases the overall height from about 105 meters in a 5-stage system to 135 meters. This height increase leads to improved energy efficiency. The first-stage outlet temperature in a 5-stage preheater typically ranges from 310-330°C. In contrast, a 7-stage preheater can lower this temperature to 180-200°C. This adjustment reduces standard coal consumption from 98-102 kg to below 90 kg. For cement companies with high coal costs, this represents a valuable cost-saving measure. Additionally, using less coal lowers carbon emissions, helping companies meet future environmental standards.
(B) Improved Separation Efficiency
The 7-stage cement kiln preheater also shows better separation efficiency compared to the 6-stage system. In a 5-stage cyclone preheater, the first-stage separation efficiency is around 92%, reaching only 95% at best. This inefficiency leads to significant raw material loss. In contrast, the 6-stage system has a specific material consumption of about 1.55 to 1.58. The 7-stage preheater can improve this to a consumption of 1.49 to 1.52. Higher separation efficiency reduces energy consumption and boosts overall production efficiency.
(C) Support for Alternative Fuel Combustion and Ultra-Low Emissions
Optimized Alternative Fuel Combustion: The additional stage in the preheater allows for better combustion of alternative fuels. This improvement ensures that these fuels burn more completely, maximizing energy use. It also lessens the impact on SCR and baghouse equipment, extending their lifespan.
Enhanced Ultra-Low Emission Efficiency: The high collection efficiency of the 7-stage preheater positively affects SCR systems. Stable and low-dust concentration flue gas enters the SCR system, improving catalyst efficiency. This helps cement companies achieve and maintain ultra-low emission targets, complying with stricter environmental regulations.
(D) Advantages of Low Pressure Drop Design (New Production Lines)
New production lines using 6-stage or 7-stage cement kiln preheaters benefit from a low pressure drop design. The redesigned pre-decomposition system minimizes resistance. Each stage's pressure drop can be controlled at 600-800 Pa. When the production line reaches its designed feed rate, the first-stage outlet pressure drop stays below 5500 Pa. Even with a 20% overproduction, the pressure drop can remain below 6500 Pa. Lower pressure drops reduce energy consumption of high-temperature fans and lower long-term operating costs.
(E) Benefits from the Elimination of the Humidification Tower
The lower outlet temperature of the 7-stage preheater allows for the removal of the humidification tower. This change simplifies the process and eliminates the need for water spraying operations. When the preheating boiler is not running, operators can manage the dust collector's temperature effectively. This reduction in equipment decreases corrosion risks and improves system reliability.
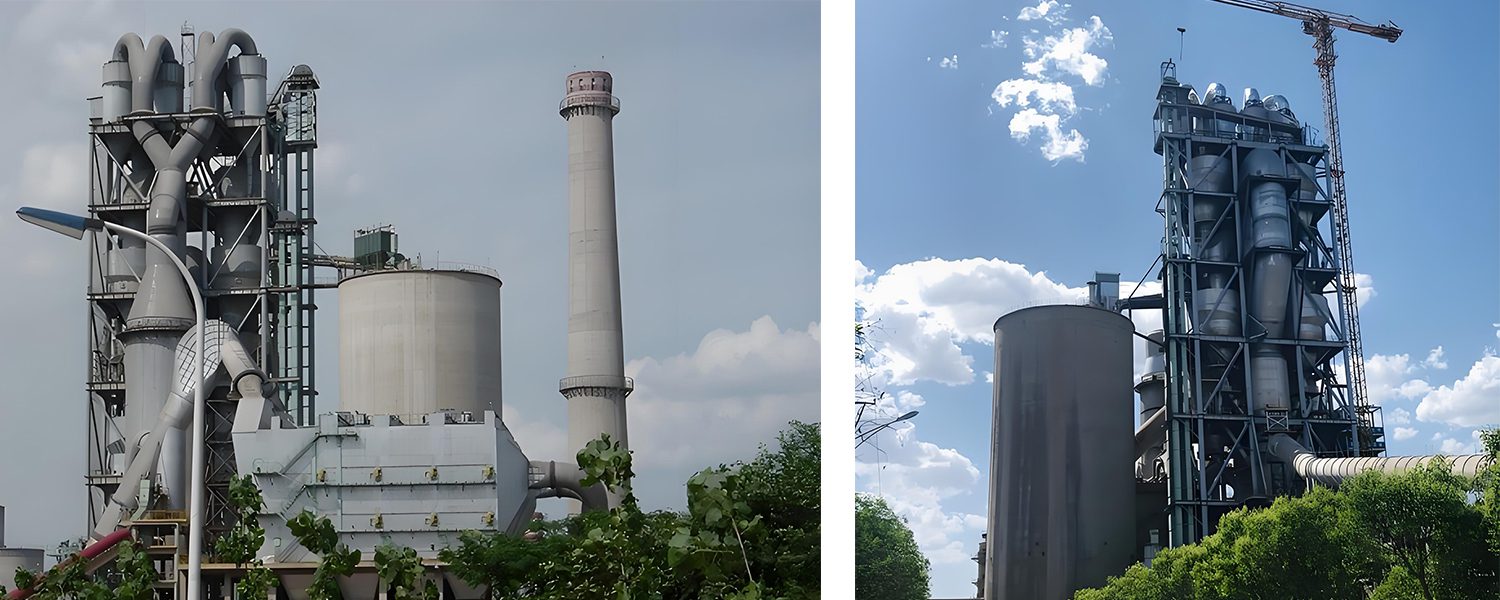
II. Challenges of the 7-Stage Cement Kiln Preheater
(A) Increased Construction Costs and Difficulty
Upgrading from a 5-stage to a 7-stage preheater raises investment costs. The higher frame and equipment heights complicate installation. This complexity requires more resources for equipment hoisting and precise installation, leading to longer project timelines and increased financial pressure.
(B) Impact on Raw Material Drying
The lower first-stage temperature means the kiln tail preheating boiler has an inlet temperature of about 200°C and an outlet temperature as low as 120°C. If raw materials have high moisture content, the mill may struggle to achieve production targets. To meet drying needs, companies may need to increase the load on high-temperature fans, raising energy consumption and affecting production stability.
(C) Reduced Waste Heat Power Generation
The lower kiln tail flue gas temperature leads to a decrease in waste heat power generation. The temperature drops from 35-40°C in a 5-stage system to 22-24°C per ton of clinker in a 7-stage system. While the 7-stage preheater brings energy savings, the reduced waste heat power generation means lower returns on energy recovery. Companies must optimize their energy management strategies to find new energy sources.
(D) Challenges in Controlling Flue Gas Temperature
To meet environmental requirements, bag dust collection is used at the kiln head and tail. If the waste heat boiler cannot run simultaneously, the maximum daily output of a 6-stage kiln system can reach only 60-70% of its designed capacity. Even with adjustments like small drafts or thicker layers, flue gas temperatures may exceed limits, risking damage to bag filters and increasing maintenance costs.
(E) High Costs for Upgrading Old Production Lines
Existing cement kilns face high retrofitting costs. Each stage of an old production line typically experiences a pressure drop of about 1200 Pa. Upgrading to a 7-stage preheater requires modifications to achieve low pressure drop design. If companies add a stage without upgrading the dust collector, system resistance will increase, causing operational costs to soar.
III. Conclusion and Outlook
In summary, the 7-stage cement kiln preheater offers significant advantages in reducing energy consumption, enhancing separation efficiency, supporting alternative fuel applications, and achieving ultra-low emissions. However, it also presents challenges, including high construction costs and impacts on raw material drying and waste heat power generation.
For new production lines, adopting the low pressure drop design of 6-stage or 7-stage preheaters is wise. This choice allows companies to benefit from technological advancements while avoiding complications and cost increases. For existing production line enterprises considering an upgrade, a thorough assessment of production conditions, energy costs, environmental requirements, and budgets is essential for informed decisions.
As the cement industry advances and faces stricter environmental requirements, the 7-stage preheater is likely to achieve further breakthroughs.
At Darko, we are dedicated to providing innovative solutions tailored to your needs. If you have questions or require assistance with our products, please contact us. We can offer customized solutions to support your transition to more efficient and sustainable operations. Let’s work together to lead the cement industry into a greener, smarter, and more efficient future.