Air pollution control technology plays a crucial role in modern industrial production. As environmental regulations become stricter, industries increasingly rely on dust collection devices. Pulse bag dust collectors have emerged as a preferred solution for dust removal because they perform efficiently.Among these, Off-line Pulse Jet Baghouse Filters stand out as an effective option.
These dust collectors fall into two categories: online and offline. By understanding the features and applications of both types, businesses can optimize their dust removal systems for better design and effectiveness.
Off-line Pulse Jet Baghouse Filters
Working Principle
The offline pulse bag dust collector features a chambered design. When cleaning is needed, control valves close the airflow to a specific chamber, stopping the filtration process. Subsequently, a pulse blowing device cleans the inactive chamber, using the powerful back pressure of compressed air to quickly remove dust from the filter bag's surface, allowing it to fall into the hopper. Once cleaning is complete, the chamber resumes filtration, and the others follow suit. This method ensures that some chambers remain operational, maintaining continuous dust removal.
Structural Characteristics
The off-line pulse jet baghouse filter mainly consists of the following parts:
Inlet
Filter bags
Cage
Flower plate
Hopper
Pulse cleaning device (including pulse valves, blowing pipes, air tanks, etc.)
Control system
Outlet
Its chambered structure gives each chamber independent control valves and pulse cleaning devices. This design enables each chamber to clean independently. Furthermore,offline pulse bag dust collectors usually have a larger hopper. This hopper collects and stores the dust that has been removed. It also includes baffles to prevent secondary dust emissions.
Application Fields
Off-line pulse jet baghouse filters are common in heavy industries like steel, cement, power, and chemicals. They are especially effective at handling large air volumes, high dust concentrations, and sticky dust. For example, in the steel industry, these collectors can tackle high gas volumes and dust concentrations in sintering machine tail dust removal systems.
Advantages and Disadvantages
Advantages
High Cleaning Efficiency: The offline cleaning method ensures complete removal of dust from the filter bags, maintaining filtration efficiency and prolonging service life.
Strong Adaptability: The chambered design allows stable operation in high dust concentration and humidity environments.
Continuous Operation: While some chambers are being cleaned, others continue filtering, ensuring system continuity.
Low Energy Consumption: The efficient cleaning process reduces operational resistance, minimizing energy use and maintenance costs.
Disadvantages
Complex Structure: The chambered design and numerous valves increase the complexity and manufacturing cost of the equipment.
Large Footprint: Compared to online dust collectors, offline pulse bag dust collectors require more installation space.
High Initial Investment: The complex structure and multiple components lead to higher initial investment costs.
Complex Maintenance: The chambered structure and numerous components make maintenance and repairs relatively complicated.
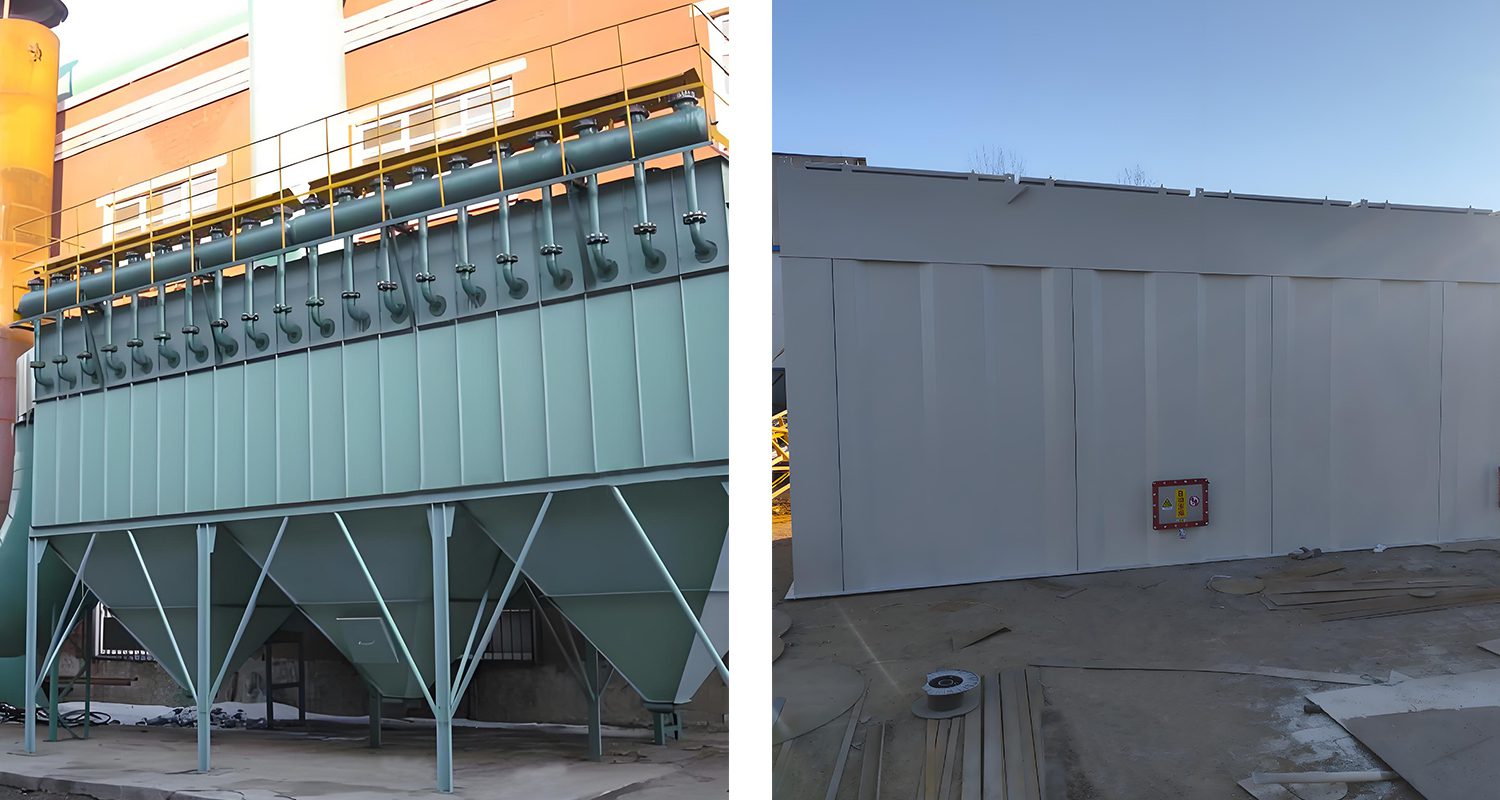
On-line Pulse Jet Baghouse Filters
Working Principle
The online pulse bag dust collector cleans while it filters. It uses high-pressure airflow to spray the surface of the filter bags. This airflow creates vibrations and impacts that dislodge dust into the hopper. The cleaning process does not require downtime. As a result, it ensures continuous gas flow and effective dust removal.
Structural Characteristics
The on-line pulse jet baghouse filter primarily consists of the following components:
Inlet
Filter bags
Cage
Flower plate
Hopper
Pulse cleaning device
Control system
Outlet
All filter bags install in one or a few chambers. This design simplifies the overall structure and reduces the number of valves and mechanical parts. As a result, it lowers complexity and costs. Additionally, on-line pulse jet baghouse filters usually have a smaller footprint. This feature makes them suitable for industrial sites with limited space.
Application Fields
On-line pulse jet baghouse filters are common in many industrial sectors. They work especially well with medium concentrations and ordinary dust. For example, in the building materials industry, such as in brick and tile production and lime kiln dust removal, these collectors efficiently remove dust generated during processes. This ensures that emissions meet environmental standards.
Advantages and Disadvantages
Advantages
Simple Structure: The design is straightforward, without complex chamber structures or valve control systems.
Low Cost: Manufacturing and maintenance costs are relatively low, making it suitable for budget-constrained scenarios.
Convenient Operation: Cleaning operations do not require downtime, simplifying the operational process.
Small Footprint: The compact design is ideal for environments with space constraints.
Disadvantages
Limited Cleaning Effectiveness: The online cleaning method may not completely remove dust from the filter bags’ surface.
Not Suitable for Sticky Dust: For highly sticky or humid dust, the online cleaning method may lead to filter bag clogging, affecting efficiency.
High Operational Resistance: Prolonged operation may increase system resistance, impacting dust removal efficiency.
Frequent Maintenance: Although structurally simple, more frequent cleaning operations may lead to increased wear on filter bags and other components, raising maintenance costs.
Differences Between Off-line and On-line Pulse Jet Baghouse Filters
Differences in Working Principles
Offline pulse bag dust collectors stop filtration by cutting off airflow to one or more chambers using control valves. This allows for cleaning before they resume filtration. In contrast, on-line pulse jet baghouse filters clean while all chambers are filtering. This design ensures continuous gas flow.
Differences in Structural Characteristics
Off-line pulse jet baghouse filters have a chambered design with independent control valves. This design leads to a complex structure and a larger size. On the other hand, on-line pulse jet baghouse filters have a simpler design. Their compact size makes them suitable for applications with limited space.
Differences in Application Fields
Off-line pulse jet baghouse filters work well in complex conditions with high dust concentration and humidity. In contrast, on-line pulse jet baghouse filters are better for medium dust concentrations and ordinary dust handling.
If you wish to achieve efficient air filtration in dust handling processes, Darko can provide you with the best solution. Our professional team will assist you in selecting the most suitable dust collection equipment based on your specific needs. Feel free to contact us anytime!