What is a roller press used for?
The roller press, also known as a squeeze mill, roller mill, or double roller machine.A roller press is a grinding device used in industrial applications, particularly in cement production. It consists of two counter-rotating rollers that compress and grind the material. This process significantly reduces the particle size of the material, making it an efficient alternative to traditional grinding methods.
The roller press has high grinding efficiency, low energy consumption, and high output, making it widely used in the cement industry. However, during operation, various issues arise due to factors such as design, usage, and external conditions. These problems lead to poor working conditions, inadequate feed control, and hydraulic system failures, all of which negatively affect the performance of the roller press. To address these challenges, we analyze the root causes and implement improvements across multiple aspects, including design and usage. As a result, we optimize the modification process, enhance efficiency, and achieve better operational results.
I.Role of the Roller Press in Cement Plants
In cement plants, operators use the roller press to grind clinker and other raw materials into fine powder. Typically, they employ it alongside other grinding systems, such as ball mills, to enhance overall efficiency and reduce energy consumption. Furthermore, the roller press's capacity to manage high pressure and produce fine products makes it an essential component of modern cement production.
II.Differences Between Roller Press and Ball Mill
The primary difference between a roller press and a ball mill lies in their grinding mechanisms. A roller press compresses the material between two rollers under high pressure, resulting in lower energy consumption and higher efficiency. In contrast, a ball mill relies on the impact and friction of balls to grind the material, which typically consumes more energy. Therefore, roller presses usually perform better in terms of energy efficiency and product fineness.
III.Skew Issues in Roller Presses
Skew refers to the misalignment between the rollers of the roller press and may arise from mechanical wear or improper installation. This misalignment can lead to uneven pressure distribution, which ultimately reduces grinding efficiency. Therefore, regular maintenance and proper alignment are crucial for minimizing skew and ensuring the optimal performance of the roller press.
IV.Analysis of Issues with Roller Presses
1. Fine Powder Content at the Outlet
The fine powder content at the outlet of the roller press, also known as first-pass yield, directly reflects the effectiveness of the pressing process. However, many companies overlook this critical aspect. Testing samples from various enterprises revealed that the German BHS roller press achieved an outlet fineness of 33% on a 0.9mm sieve and 64% on a 0.08mm sieve (with 36% below 0.08mm). In contrast, many of these machines do not reach similar results.
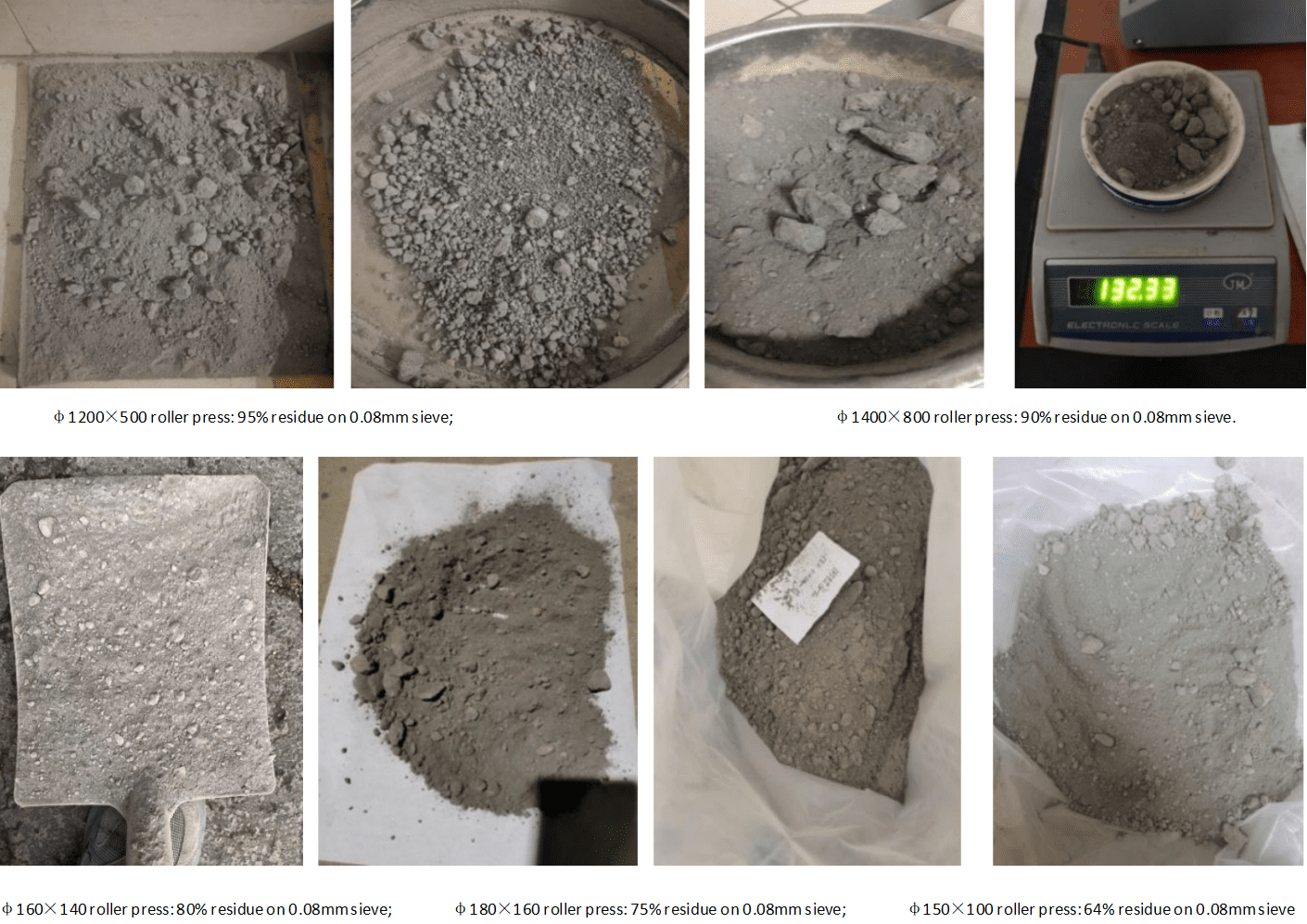
2. Working Pressure
The pressing force is the most fundamental parameter determining the effectiveness of the roller press. To calculate the total force F (in kN) of the roller press, we use the formula:
F=n⋅S⋅Pr
where:
- n= number of hydraulic cylinders
- S= effective area of the hydraulic cylinder (m²)
- Pr = hydraulic system pressure (MPa)
Moreover, the average roller pressure Pcp(in kN/m²) is given by:
Pcp=2F/D⋅B⋅sinα
Here:
- D = diameter of the grinding roller (m)
- B = effective width of the grinding roller (m)
- α = pressure angle, also known as the bite angle (°)
Projected Pressure Calculation
In addition, the projected pressure PT (in kN/m²) is calculated using:
PT=F/B⋅D
Impact of Maximum Roller Pressure on Pressing Efficiency
In practice, the maximum roller pressure significantly affects the pressing effect. Specifically, when the line connecting the centers of the two rollers is set at 0 degrees, the pressure angle starts at 8.3 degrees and ends at -1.6 degrees. Notably, the maximum peak pressure occurs at 1.5 degrees, slightly exceeding twice the average pressure.
Moreover, the hydraulic system of the roller press plays a crucial role, as it provides the dynamic roller pressure necessary to compress the material. This system consists of various components, including the oil station, hydraulic cylinders, nitrogen bags, solenoid valves, overflow valves, pressure gauges, oil lines, and control cabinet. If the configuration lacks damping adjustment valves and stroke adjustment valves, it cannot achieve optimal pressing results. Therefore, in some cases, adding small nitrogen bags may prevent the displayed pressure from accurately reflecting actual pressure changes.
Nitrogen Bag Configuration and Pressure Management
- The size of the nitrogen bags and the piping must be calculated based on the size of the hydraulic cylinders. Furthermore, using pipes that are too small will increase resistance. In a parallel setup, when one large and one small nitrogen bag are used, the small bag activates first, followed by the large bag. As a result, this process repeatedly suppresses the opening of the roller gap, which operates in a cycle of retracting, retracting, and advancing, ultimately resulting in low pressing efficiency.
- Moreover, the pressures of the nitrogen bags are set at 8, 10, and 12 MPa, meaning that only one nitrogen bag operates within a specific range while the other two become ineffective. Although this theory of differential pressure was initially proposed by German engineers, it failed to achieve the expected results due to significant variations in material properties. Consequently, the Germans did not pursue this approach further.
- In general, it is advisable to set the nitrogen bag pressure at 60-80% of the system’s minimum pressure. This approach ensures that when the system operates at its lowest working pressure, a certain level of safety is maintained between the nitrogen bags and the on-off valve. However, the system’s operational state must be monitored on-site to determine its effectiveness. If the oil temperature is too high or too low, it indicates that the system is not in good working condition, which severely impacts pressing efficiency.
3. Roller Speed
The roller speed of the roller press can be expressed in two ways: one is the circumferential linear speed V of the rollers, and the other is the rotational speed of the rollers. The circumferential linear speed is related to output, power consumption, and operational stability. Generally, higher roller speeds lead to increased output; however, excessively high speeds can cause greater relative sliding between the rollers and the material, resulting in poor engagement and increased wear on the roller surfaces, which negatively impacts the output of the roller press.
Currently, the typical roller speed ranges from 1.0 to 1.75 m/s, with some experts suggesting that it should not exceed 1.5 m/s. The linear speed of the rollers usually falls between 1.0 and 1.7 m/s, with most operating around 1.5 to 1.7 m/s, and some even reaching 2.0 to 2.2 m/s. It is crucial to prioritize the squeezing effect when selecting the speed; this effect should be based on actual sampling. If the speed is too high, the pressing time shortens, leading to increased vibrations in the equipment. The significant variations in force become difficult to control, resulting in excessive power consumption without achieving the desired pressing effect.
4. Operating Gap and Material Properties
The operation of the roller gap is influenced by various factors, including the properties of the material (such as hardness, particle size, and moisture content), the form of the roller surface, the speed, the pressure, and the pressure control method. There are two ways to control the hydraulic cylinder pressure: constant pressure control and constant gap control. However, regardless of the method used, both are fundamentally flawed from a hydraulic perspective because pressure and gap continuously fluctuate.
The pressure gauge has a response time of 200 milliseconds, which complicates the control of the oil pump's pressure adjustments. This, in turn, affects the hydraulic cylinder pressure and subsequently the roller gap. As a result, there are two main issues: first, there is a lag in response; second, excessive pressure differentials occur. These factors hinder the stable operation of the roller press and negatively impact pressing efficiency.
5. Feeding Device
Currently, most roller presses use a feeding device that directs material straight from the hopper into the roller gap, pulling the material between the two rollers. This process is commonly referred to as the "pull-in angle" of the roller press. However, controlling the flow from two directions is not feasible, as the adjustment range is limited, making it difficult to achieve precise and stable control. Additionally, the other two directions cannot be adjusted at all. As a result, issues such as material segregation and roller misalignment frequently occur, leading to unmanageable conditions.
V.Roller Press System Modification Plan
1. Replacement of Feeding Device
Replace the roller press feeding device with a new type of four-direction feeding system (patented technology) to control the material feed. This system allows for adjustment and control from two directions, enabling reasonable control of material flow. The other two directions can be adjusted to correct the lateral gap deviation between the rollers, reducing the impact of the material on the roller press and facilitating the formation of a stable material bed. This approach eliminates issues such as material segregation and roller misalignment, and it operates at a low hopper position, making it easier to adjust and control.
2. Upgrading the Hydraulic System
We replaced the hydraulic system of the roller press, including components such as the oil station, overflow valve, pressure gauge, accumulator (nitrogen bag), and valve assembly. Additionally, we incorporated damping adjustment valves and stroke adjustment valves (patented technology) to make the hydraulic system flexible, rigid, and controllable.
During the research and development process, we conducted extensive field tests using a specialized high-precision pressure measurement device (1000 Hz) to collect and analyze data. We employed dedicated simulation software and complex mathematical models to successfully develop a dual-channel adjustable damping anti-vibration regulation mechanism, achieving a reasonable balance of rigidity and flexibility in the hydraulic system.
3. Implementing PLC Control
We replaced the roller press hydraulic PLC and implemented four-directional control of the feeding device, utilizing a constant power control method for easier centralized operation. We configured the system with Siemens SIMATIC S7-1200, integrating Siemens SINAMICS drive products and SIMATIC human-machine interface products. The CPU comes standard with an Ethernet interface that supports various industrial Ethernet communication protocols, including PROFINET, TCP, UDP, and Modbus TCP.
Our company developed this technology through mathematical modeling, gathering extensive field data during the research and development process. We employed specialized simulation software and complex mathematical models, which have been validated through practical application.
VI.Case Studies
1. Chao Lake Hengxin Cement Co., Ltd.
Since the modification in August 2020, production efficiency has increased from 200 tons/hour to 290 tons/hour, with energy consumption controlled at 22 kWh/ton of cement.
2. Hainan Huaren Cement
In June 2022, the roller press was upgraded, increasing hourly output from 150-160 tons to 180-200 tons, with energy consumption reduced to about 23 kWh/ton.
3. Guizhou Southwest
Through the upgrade, output has risen to 180-190 tons/hour, and energy consumption decreased from 32 kWh/ton to 25 kWh/ton.
4. Jiangxi Sanqing Cement Co., Ltd.
After the modification, the output increased to 270-280 tons/hour, with stable operation and nitrogen bag temperatures maintained at 40-60°C.
VII.Benefits of Roller Press Technology Upgrade and Modification
- The stability of the roller press has improved, with virtually no side leakage. There are three methods for adjusting roller skew: first, four-directional feed adjustment; second, hydraulic system adjustments; and third, separate pressure adjustments for left and right. Control is stable, with minimal occurrences of material collapse and roller skew.
- The hydraulic system of the roller press is flexibly adjustable and controllable. The fluctuation of the roller gap has changed from slow retraction and fast advance to fast retraction and slow advance, increasing pressing efficiency. The fine powder content at the roller press outlet has increased by 3-7%, the specific surface area of the input material has improved, and hourly output has increased by 10-20%.
- A constant power control method is used, with operational power maintained at 85±5% of the rated power. The efficiency of the roller press has two requirements: first, high operational power; second, high first-pass yield. By improving the efficiency of the roller press and reducing mill power consumption, the overall energy consumption has been lowered by 2-5 kWh/ton.
If you have needs regarding the modification and upgrading of roller press systems, please feel free to contact us at Darko. We will provide you with professional solutions and support.