When you install bag dust collectors, keep a few key points in mind. This will help ensure efficient operation and easy maintenance. Ultimately, proper installation improves air quality and boosts productivity in industrial settings.
1. Layout of the Dust Collection System
The layout of your dust collection system is crucial. Therefore, follow these principles for the best results:
- Proximity of Dust Sources: First, combine dust sources into one system if they are close together and operate simultaneously. This approach reduces ducting and enhances efficiency.
Different Types of Dust: Additionally, if dust sources produce different types of dust but operate at the same time, create a single system if mixed recovery is possible. This simplification benefits overall operations.
Temperature and Humidity Variations: Moreover, install separate systems for dust-laden gases with varying temperatures and humidity. This can prevent condensation in the ducts, which might lead to operational issues.
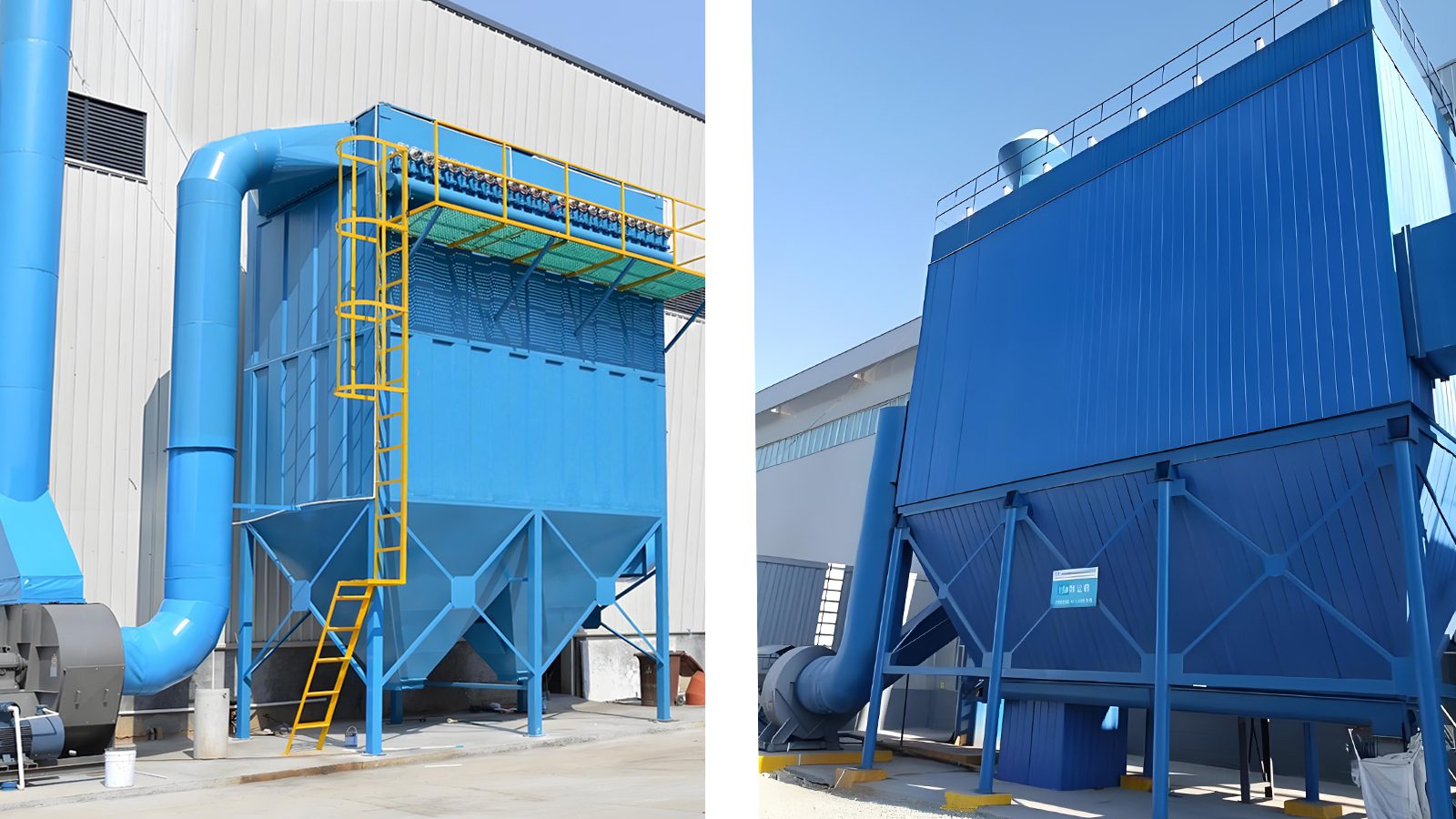
When many dust sources exist, set up the dust collection system in concentrated zones. Each system should connect to a limited number of exhaust points. If you cannot achieve hydraulic balance through adjustments, consider installing balancing valves on branches with lower resistance. Furthermore, place these valves on vertical ducts to enhance performance.Talk to us if you are dealing with these challenges.
Calculate the exhaust volume based on the maximum simultaneous exhaust volume and the leakage volume from intermittent points. Ensure each intermittent point has valves linked to the process equipment. Additionally, maintain leakage volume at 15% to 20% of normal exhaust volume when the valves are closed.
Note: When designing multiple exhaust cabinets as one system, determine the system's airflow based on the total airflow of the cabinets used at the same time. Install a valve for airflow regulation at each exhaust cabinet's outlet. Also, ensure that the fan has variable frequency drive capabilities.
2. Types of Dust Collection Systems
Bag dust collectors can be classified into three types based on production processes, equipment layout, and exhaust volume:
Local Dust Collection: For example, install bag dust collectors directly near production equipment. This setup captures and recovers dust on-site. It requires minimal or short ducting, making it efficient.
Dispersed Dust Collection System: In contrast, when exhaust points in a workshop are spread out, combine appropriate exhaust points based on the nature of the conveyed gases. Therefore, position the industrial dust collectors and fans as close as possible to the dust-generating equipment. This approach leads to shorter ducts and easier pressure balance.
Centralized Dust Collection System: This system is suitable for workshops with concentrated dust sources. In this case, centralize all exhaust points or arrange several dust extraction systems together. Centralized systems simplify dust handling and maintenance. However, they often require longer and more complex ducting, which can be a drawback.
Application in Cement Plants
In cement plants, bag dust collectors play a vital role in several areas:
- Raw Material Handling: They capture dust generated during the processing and transportation of raw materials like limestone and clay.
- Milling Process: During the grinding of cement clinker and other materials, these collectors effectively manage the fine dust produced.
- Mixing and Packaging: Bag dust collectors control dust emissions during mixing and packaging, ensuring a clean environment and high product quality.
- Kiln Emissions: They help in purifying exhaust gases from the kiln, reducing air pollution and adhering to environmental regulations.
3. Layout Guidelines for Dust Collectors
When laying out your bag dust collectors, follow these principles:
First, position the dust collector above equipment like belt conveyors and hoppers if you can integrate the collected dust into the production process. This improves workflow significantly.
Alternatively, if the collected dust cannot easily integrate, place the dust collector in a suitable location with a dust storage bin. This ensures easy access for maintenance.
Additionally, locate dust collectors in the negative pressure section of the system. If they are in a positive pressure section, use exhaust fans to manage airflow effectively.
Ensure the pressure loss at each exhaust point does not exceed 10%. If you cannot achieve this through adjustments, consider installing airflow regulation devices to maintain efficiency.
Finally, for wet gas purification equipment at risk of freezing, implement anti-freezing measures. In colder regions, install wet gas purification equipment indoors.
Note: Position flue gas dust collectors outdoors to ensure proper operation.
Make sure that the dust discharge pipes of dry dust collectors and the wastewater discharge pipes of wet dust collectors have measures to prevent air leakage. This helps maintain efficiency and safety.
Allowable deviations and inspection methods for dust collector installation
Item No. | Project | Allowed Deviation (mm) | Inspection Method |
1 | Horizontal Displacement | ≤10 | Theodolite or cable and ruler inspection |
2 | Elevation | ±10 | Level, straight line and ruler inspection |
3 | Verticality | ≤2 per meter | Hanging wire and ruler inspection |
4 | Total Deviation | ≤10 |
4. Installation Requirements for Bag Dust Collectors
To install your bag dust collectors effectively, follow these requirements:
Confirm that the installation position is correct and that the unit is securely fixed. Allowable deviations should meet relevant standards for safety and performance.
Furthermore, ensure that moving or rotating parts operate flexibly and reliably. This step is essential for long-term reliability.
The installation of ash discharge valves, unloading valves, and sludge discharge valves should be tight for easy operation and maintenance. This facilitates easy access for cleaning and upkeep.
For the on-site assembly of bag dust collectors, meet these requirements:
Seal the outer shell properly. Additionally, ensure the filter bag interfaces are secure to prevent dust leakage.
For compartmentalized reverse-blowing bag dust collectors, install the filter bags straight. Maintain the tension on each filter bag at 30N/m ± 5N/m to ensure optimal performance.
For mechanical rotary flat bag dust collectors, ensure the rotating arms operate smoothly. The top cover of the clean air chamber should be well-sealed.
Finally, for pulse bag dust collectors, align the blowing nozzle with the center of the venturi tube. Allow a deviation of no more than 2mm.
At Darko, we provide high-quality bag dust collectors and dust collection systems tailored to your industrial needs. Our expertise ensures optimal performance, efficiency, and compliance with environmental standards. We are dedicated to helping you maintain a clean and safe working environment.
