In industrial production, the boiler bag dust collector plays a crucial role in reducing dust emissions and protecting the environment. Recently, we conducted a comprehensive inspection and analysis of a specific dust collector's operation. We found several issues that affected the equipment's efficiency and hindered environmental protection goals. This article will analyze the operational problems of the boiler bag dust collector and their causes. We will also propose corresponding corrective measures to enhance the equipment's performance and ensure efficient and stable operation.
1. Emission Concentration Not Up to Standard
The designed emission concentration is 50 mg/m³. However, on-site tests show much higher levels.
1.1 Reasons for Non-Compliance
1.1.1 Excessive Air Velocity
High air velocity causes some dust to pass through the filter media and be discharged directly. According to the original design, the online cleaning airflow reaches 1.09 m/min, while the offline cleaning airflow reaches 1.25 m/min.
1.1.2 Damaged Bags
Bag damage results from improper material or installation, leading to air leaks. We observed uneven dust discharge below the flower plate, with some bags even making contact. Under expansion during reverse blowing, bags are prone to wear. Additionally, misalignment between nozzles and bags can accelerate bag damage.
1.1.3 Air Leakage
The equipment experiences air leakage, especially at the flower plate, allowing dust to bypass the bags. We found a significant amount of dust in the clean room.
1.1.4 High Dust Concentration
The test report indicates that the coal used in the boiler differs significantly from the designed type. The ash content is high, and the coal size is small (with a high proportion below 1 mm), resulting in increased coal input and total ash volume. This further raises the dust concentration at the dust collector's inlet, causing bag overload.
2. Excessive Operating Resistance
The designed resistance is <1300 Pa, while the measured data is around 1500 Pa.
2.1 Reasons for High Resistance
2.1.1 Fast Design Air Velocity
The filtering air speed is directly proportional to resistance; higher speeds lead to higher resistance.
2.1.2 Issues with the Pulse Jet System
Misalignment between nozzles and bags prevents effective reverse blowing, causing severe dust accumulation on the bags and increasing resistance. The small diameter of the gas supply pipe limits the replenishment effect, impacting cleaning efficiency.
2.1.3 Insufficient Settling Space
The internal settling space of the dust collector is only 380 mm, making effective settling difficult and leading to increased bag load and resistance.
2.1.4 Bag Caking
Low inlet temperatures and high sulfur content can raise the dew point temperature of flue gas, resulting in bag caking.
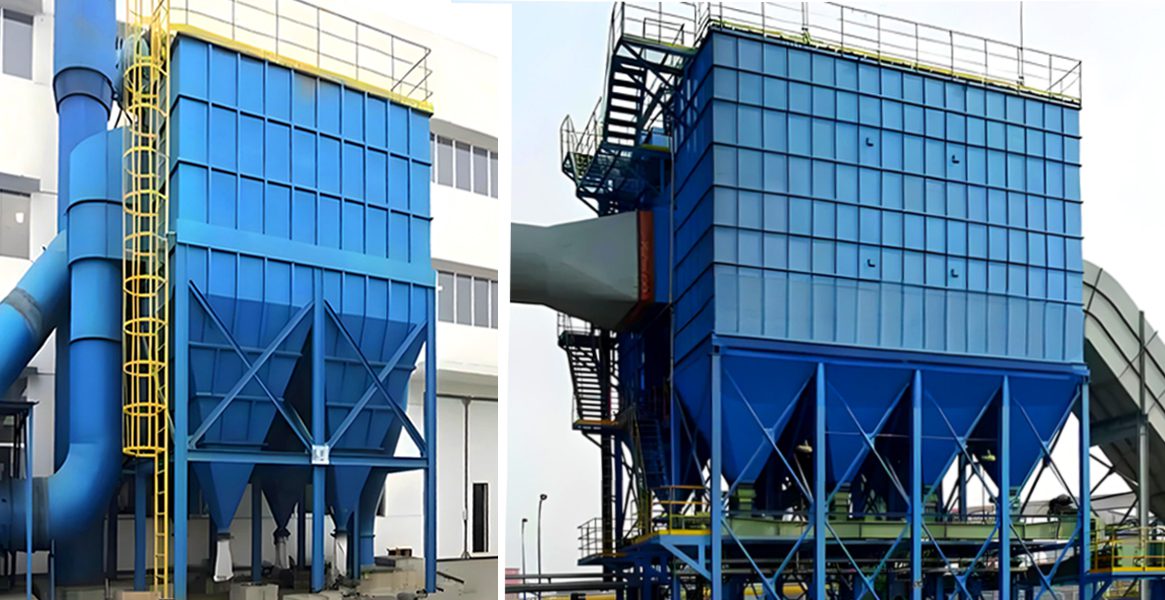
3. Need for Performance Expansion
Due to production demands, the dust collector urgently requires performance expansion, targeting a processing air volume of 350,000 m³/h.
4. Corrective Measures
In response to the above issues and based on the site conditions, Darko's technicians will implement the following corrective measures:
4.1 Replace with Pleated Bags
We will use pleated bags to increase the filtration area. We will select 160×6000 pleated bags, each with a filtration area of 5.5 m². This will raise the total filtration area to 7260 m². With a processing volume of 350,000 m³/h, the online cleaning airflow will be 0.8 m/min, and the offline cleaning airflow will be 0.91 m/min.
4.2 Replace with Custom Cage
The new cage will work with pleated bags and will ensure adequate strength and vertical alignment according to industry standards.
4.3 Inspect and Correct the Flower Plate
We will check the flatness, hole dimensions, and surface roughness of the flower plate to prevent leaks during bag and cage installation.
4.4 Improve the Pulse Jet System
We will redesign and replace the blowing pipes, installing quick-disconnect devices. We will increase the air supply pipe diameter to 89 mm and check for leaks.
4.5 Increase Settling Space
By using pleated bags, which are 6 meters long, we will increase the internal settling space to nearly 1 meter, significantly enhancing settling efficiency.
5. Quality Assurance and After-Sales Service
5.1 Quality Assurance
After the renovation, we guarantee that when the inlet air volume is <350,000 m³/h, dust concentration is <50 g/m³, and the dew point temperature is <15℃, the dust collector's operating resistance will be ≤1200 Pa, and it will operate for ≥30,000 hours, with an outlet dust concentration ≤30 mg/m³.
5.2 After-Sales Service
- Our service personnel will arrive on-site within 48 hours of notification (limited to mainland China).
- During the warranty period, we will provide free guidance for installation and commissioning.
- We will offer discounts on spare parts.
6. On-Site Operation Precautions
6.1 Operating Temperature
- High flue gas temperatures accelerate chemical reactions, damaging filter materials and reducing their lifespan.
- The operating temperature must remain above 15℃ to avoid concentrated water vapor forming corrosive acid dew.
- Sparks in the flue gas can damage filter bags, so preventive measures are essential.
6.2 Bag Installation Precautions
- Before installation, keep the site clean and orderly, removing impurities and ensuring a smooth process.
- Install spark arresters before flue gas enters the dust collector to eliminate spark risks.
- Ensure good sealing of the dust collector to prevent localized cooling and condensation.
- After bag installation, use lime powder or talc for pre-coating to extend the lifespan of the filter materials.
Conclusión
Through the in-depth analysis of the operational issues of the boiler bag dust collector and the implementation of corrective measures, we aim to significantly enhance the equipment's performance and stability. This will not only meet production needs but also reduce environmental impact, ensuring sustainable development for the enterprise. We will continue to monitor the equipment's operational status, conducting regular inspections and maintenance to ensure compliance with environmental standards and support green production.
For further information or to discuss how we can assist you, please Contacto. We look forward to collaborating with you to achieve effective solutions for your dust collection needs.