El proceso de producción de cemento busca continuamente la innovación y la optimización. La introducción de un precalentador de horno de cemento de 7 etapas plantea cuestiones importantes. ¿Qué significa este cambio? ¿Qué oportunidades y retos supondrá para cemento ¿empresas?
I. Ventajas del precalentador de 7 etapas para hornos de cemento
(A) Ahorro significativo de energía
El precalentador de 7 etapas del horno de cemento aumenta la altura total de unos 105 metros en un sistema de 5 etapas a 135 metros. Este aumento de altura conlleva una mayor eficiencia energética. La temperatura de salida de la primera etapa en un precalentador de 5 etapas suele oscilar entre 310 y 330°C. En cambio, un precalentador de 7 etapas puede reducir esta temperatura a 180-200°C. Este ajuste reduce el consumo estándar de carbón de 98-102 kg a menos de 90 kg. Para las empresas cementeras con altos costes de carbón, esto representa una valiosa medida de ahorro. Además, usar menos carbón reduce las emisiones de carbono, lo que ayuda a las empresas a cumplir las futuras normas medioambientales.
(B) Mejora de la eficacia de separación
El precalentador de 7 etapas del horno de cemento también muestra una mayor eficacia de separación en comparación con el sistema de 6 etapas. En un precalentador de ciclones de 5 etapas, la eficacia de separación en la primera etapa es de unos 92%, alcanzando sólo 95% en el mejor de los casos. Esta ineficacia provoca una pérdida importante de materia prima. En cambio, el sistema de 6 etapas tiene un consumo específico de material de aproximadamente 1,55 a 1,58. El precalentador de 7 etapas puede mejorarlo hasta un consumo de 1,49 a 1,52. Una mayor eficacia de separación reduce el consumo de energía y aumenta la eficacia general de la producción.
(C) Apoyo a la combustión de combustibles alternativos y a las emisiones ultrabajas
Combustión optimizada de combustibles alternativos: La etapa adicional del precalentador permite una mejor combustión de los combustibles alternativos. Esta mejora garantiza que estos combustibles se quemen más completamente, maximizando el uso de la energía. También reduce el impacto en los equipos SCR y de filtros de mangas, alargando su vida útil.
Eficiencia mejorada de emisiones ultrabajas: La alta eficacia de recogida del precalentador de 7 etapas afecta positivamente a los sistemas SCR. Los gases de combustión estables y con baja concentración de polvo entran en el sistema SCR, mejorando la eficacia del catalizador. Esto ayuda a las empresas cementeras a alcanzar y mantener los objetivos de emisiones ultrabajas, cumpliendo las normativas medioambientales más estrictas.
(D) Ventajas del diseño de baja pérdida de carga (nuevas líneas de producción)
Las nuevas líneas de producción que utilizan precalentadores de horno de cemento de 6 ó 7 etapas se benefician de un diseño de baja caída de presión. El sistema de predescomposición rediseñado minimiza la resistencia. La caída de presión de cada etapa puede controlarse a 600-800 Pa. Cuando la línea de producción alcanza la velocidad de alimentación diseñada, la caída de presión de salida de la primera etapa se mantiene por debajo de 5500 Pa. Incluso con una sobreproducción de 20%, la caída de presión puede permanecer por debajo de 6500 Pa. Las menores caídas de presión reducen el consumo de energía de los ventiladores de alta temperatura y disminuyen los costes de funcionamiento a largo plazo.
(E) Beneficios de la eliminación de la torre de humidificación
La menor temperatura de salida del precalentador de 7 etapas permite suprimir la torre de humidificación. Este cambio simplifica el proceso y elimina la necesidad de operaciones de pulverización de agua. Cuando la caldera de precalentamiento no está en marcha, los operarios pueden gestionar la colector de polvode forma eficaz. Esta reducción del equipo disminuye los riesgos de corrosión y mejora la fiabilidad del sistema.
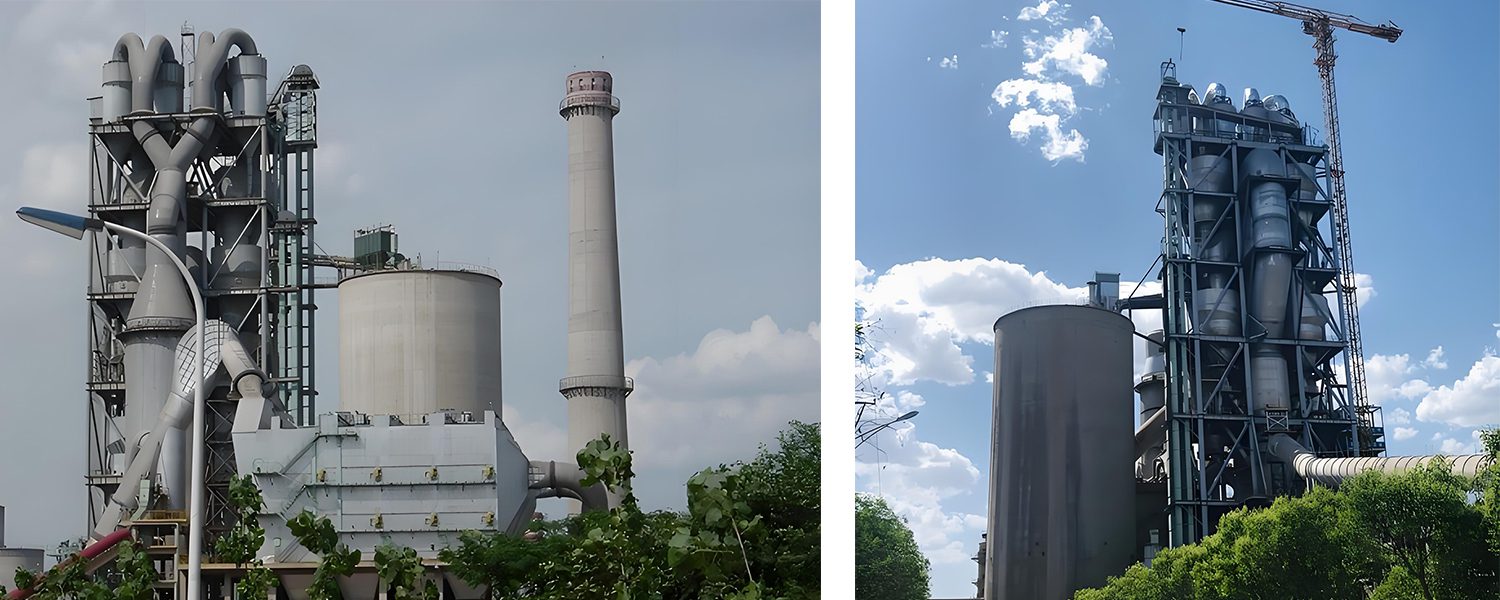
II. Retos del precalentador de 7 etapas del horno de cemento
(A) Aumento de los costes y la dificultad de la construcción
Pasar de un precalentador de 5 etapas a uno de 7 aumenta los costes de inversión. La mayor altura del bastidor y del equipo complica la instalación. Esta complejidad requiere más recursos para el izado del equipo y una instalación precisa, lo que alarga los plazos del proyecto y aumenta la presión financiera.
(B) Impacto en el secado de la materia prima
La temperatura más baja de la primera etapa significa que la caldera de precalentamiento de la cola del horno tiene una temperatura de entrada de unos 200°C y una temperatura de salida tan baja como 120°C. Si las materias primas tienen un alto contenido de humedad, el molino puede tener dificultades para alcanzar los objetivos de producción. Para satisfacer las necesidades de secado, las empresas pueden tener que aumentar la carga de los ventiladores de alta temperatura, lo que eleva el consumo de energía y afecta a la estabilidad de la producción.
(C) Reducción de la generación de energía a partir del calor residual
La menor temperatura de los gases de combustión de cola del horno provoca una disminución de la generación de calor residual. La temperatura baja de 35-40°C en un sistema de 5 etapas a 22-24°C por tonelada de clinker en un sistema de 7 etapas. Aunque el precalentador de 7 etapas supone un ahorro de energía, la menor generación de potencia de calor residual significa un menor rendimiento de la recuperación de energía. Las empresas deben optimizar sus estrategias de gestión energética para encontrar nuevas fuentes de energía.
(D) Desafíos en el control de la temperatura de los gases de combustión
Para cumplir los requisitos medioambientales, bolsa de recogida de polvo se utiliza en la cabeza y la cola del horno. Si la caldera de calor residual no puede funcionar simultáneamente, la producción máxima diaria de un sistema de horno de 6 etapas puede alcanzar sólo 60-70% de su capacidad diseñada. Incluso con ajustes como pequeñas corrientes de aire o capas más gruesas, las temperaturas de los gases de combustión pueden superar los límites, con el riesgo de dañar los filtros de mangas y aumentar los costes de mantenimiento.
(E) Elevados costes de modernización de las antiguas líneas de producción
Los hornos de cemento existentes se enfrentan a elevados costes de adaptación. Cada etapa de una línea de producción antigua suele experimentar una caída de presión de unos 1200 Pa. La actualización a un precalentador de 7 etapas requiere modificaciones para conseguir un diseño de baja caída de presión. Si las empresas añaden una etapa sin actualizar el colector de polvo, aumentará la resistencia del sistema, lo que disparará los costes operativos.
III. Conclusión y perspectivas
En resumen, el precalentador de 7 etapas del horno de cemento ofrece ventajas significativas para reducir el consumo de energía, mejorar la eficacia de la separación, apoyar las aplicaciones de combustibles alternativos y lograr emisiones ultrabajas. Sin embargo, también presenta retos, como los elevados costes de construcción y las repercusiones en el secado de las materias primas y la generación de calor residual.
Para las nuevas líneas de producción, adoptar el diseño de baja caída de presión de los precalentadores de 6 o 7 etapas es una decisión acertada. Esta elección permite a las empresas beneficiarse de los avances tecnológicos, evitando al mismo tiempo complicaciones y aumentos de costes. Para las empresas de líneas de producción existentes que estén considerando una actualización, es esencial una evaluación exhaustiva de las condiciones de producción, los costes energéticos, los requisitos medioambientales y los presupuestos para tomar decisiones informadas.
A medida que la industria del cemento avance y se enfrente a requisitos medioambientales más estrictos, es probable que el precalentador de 7 etapas consiga nuevos avances.
En Darkonos dedicamos a ofrecer soluciones innovadoras adaptadas a tus necesidades. Si tienes preguntas o necesitas ayuda con nuestros productos, por favor Contacto. Podemos ofrecerte soluciones personalizadas para apoyar tu transición hacia operaciones más eficientes y sostenibles. Trabajemos juntos para conducir a la industria cementera hacia un futuro más ecológico, inteligente y eficiente.