En los talleres industriales existen muchos tipos de colectores de polvo, cada uno con sus ventajas e inconvenientes. Los colectores de polvo más comunes incluyen colectores de polvo de cartucho, colectores de polvo de mangas y colectores ciclónicos de polvo. En cambio, los precipitadores electrostáticos y los precipitadores húmedos se utilizan menos debido a su elevado coste de inversión y a su limitada aplicabilidad. Aunque el precipitador electrostático tiene un alto rendimiento, su economía no es elevada. Los colectores de polvo húmedo son más adecuados para tratar polvo húmedo, pegajoso o peligroso. Por lo tanto, la selección del colector de polvo adecuado es muy importante para mejorar la calidad del aire y la eficacia de la producción.
¿Qué es un filtro ciclónico?
Los filtros ciclónicos se utilizan ampliamente para controlar las emisiones de partículas en el aire. Su estructura simple, su facilidad de instalación y su sencillo mantenimiento los hacen populares en muchas instalaciones de procesamiento de grano, incluyendo la limpieza del grano, el secado, la producción de semillas, el almacenamiento y el procesamiento de piensos. Estos dispositivos no tienen piezas móviles, lo que se traduce en bajos costes operativos y reducidos índices de averías, gestionando eficazmente el polvo generado durante la producción de grano.
El colector de polvo ciclónico es un dispositivo de eliminación de polvo seco, que puede capturar eficazmente partículas con un tamaño de entre 5 y 10 micras. Su principio de funcionamiento es que el aire polvoriento entra en el colector de polvo a través del ventilador y gira en forma de espiral en la carcasa. La fuerza centrífuga y la fuerza de fricción separan el polvo del flujo de aire, hacen que se adhiera a la pared y, finalmente, se hunda hasta el fondo bajo la acción de la gravedad.
Además, el diseño mejorado integra deflectores anulares en la carcasa. Tras el tratamiento preliminar, las partículas finas no recogidas chocarán con estos deflectores, se separarán aún más bajo la acción de la gravedad y la fricción y, finalmente, el polvo se depositará en la cámara designada. Este diseño no sólo es compacto y ahorra espacio, sino que también mejora significativamente la eficacia de eliminación del polvo.
Ventajas de los captadores ciclónicos de polvo
1. Estructura sencilla, bajo coste de funcionamiento: El colector ciclónico de polvo no tiene piezas móviles ni partes vulnerables, tiene un bajo coste de funcionamiento y un bajo índice de averías. Su diseño puede eliminar eficazmente el polvo y es fácil de fabricar, instalar y mantener.
2. Tratamiento eficaz del polvo: El ciclón es un sistema de eliminación de polvo seco, que puede recuperar eficazmente el polvo valioso. El polvo acumulado en el fondo bajo la acción de la gravedad puede descargarse fácilmente a través de la válvula de descarga y enviarse al depósito de recogida para su tratamiento.
3. Capacidad de funcionamiento en paralelo: El ciclón puede utilizarse en paralelo para manejar un gran volumen de aire. Durante el funcionamiento, el aire entra a una velocidad tangencial elevada, normalmente de 12 a 25 m/s, para garantizar un flujo de aire uniforme y mejorar la eficacia de eliminación del polvo sin aumentar la resistencia.
4. Resistencia a altas temperaturas: El colector ciclónico de polvo está hecho de acero al carbono y puede soportar altas temperaturas de más de 400 ° C. En condiciones especiales, el uso de materiales resistentes a altas temperaturas puede mejorar aún más su resistencia a las altas temperaturas.
Desventajas de los separadores de ciclón
1. Baja eficacia en la manipulación de partículas pequeñas: el separador ciclónico no es válido para partículas de polvo inferiores a 5 micras o que contengan humedad y viscosidad. Cuando el aire polvoriento entra en el separador de polvo, es posible que la fuerza centrífuga no pueda separar eficazmente estas partículas finas y húmedas, lo que provocaría un efecto de filtrado deficiente.
2. Fácil de llevar: El movimiento giratorio del gas provocará el desgaste de la superficie interior del colector de polvo. El impacto continuo de las partículas de polvo aumentará el riesgo de daños con el paso del tiempo.
Principio de funcionamiento y diseño estructural
Principio de funcionamiento
El colector ciclónico de polvo se compone de un tubo de alimentación, un tubo de descarga, una cámara colectora de polvo, un deflector, una tolva colectora de polvo y una válvula de descarga. Su estructura sencilla, fácil de fabricar, instalar y mantener, es una opción ideal para el procesamiento de granos. Cuando el aire polvoriento fluye a través del colector de polvo a una velocidad de unos 12-25 M/s, la fuerza centrífuga que actúa sobre las partículas de polvo puede alcanzar de 5 a 2500 veces la gravedad. Esto lo hace más eficaz que la cámara de decantación por gravedad tradicional. El deflector se añade para separar aún más las partículas de polvo por colisión, con el fin de mejorar la eficacia.
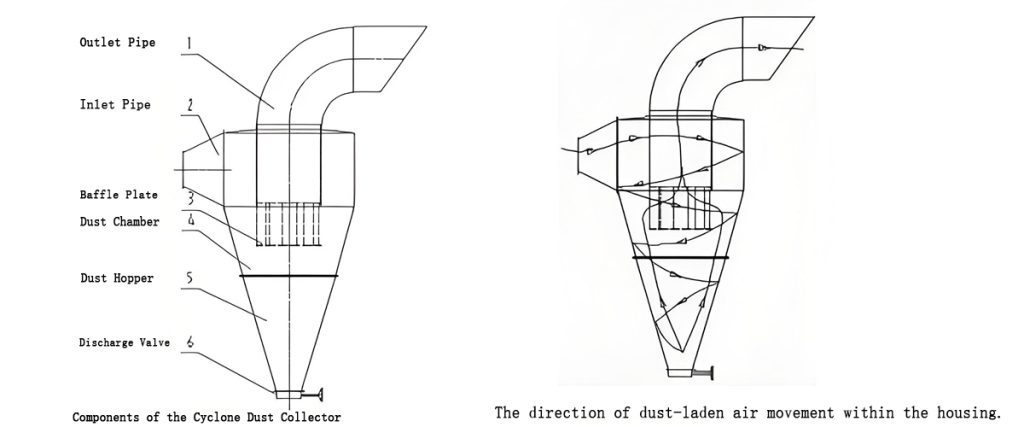
Diseño estructural de componentes clave
1.Tubo de entrada: El tubo de entrada dirige el flujo de aire hacia el colector ciclónico. Conecta el ventilador a la carcasa del colector de polvo. Las entradas tangenciales son habituales, con ángulos que suelen ser de 45°, 120°, 180° o 270°. La eficacia del colector ciclónico depende del área de entrada y del caudal de aire. Un área de entrada menor aumenta la velocidad tangencial, mejorando el tratamiento del polvo.
2.Tubo de salida: El tubo de salida expulsa el aire tratado. A medida que el aire se dirige en espiral hacia el fondo, crea un vórtice interno ascendente que permite una descarga suave a través de la salida. La altura y la sección transversal de la salida afectan directamente a la resistencia y a la eficacia de la captación de polvo.
3.Placas deflectoras: Las placas deflectoras del interior del colector facilitan una separación adicional del polvo. A medida que fluye el aire, las partículas de polvo más grandes y pesadas se depositan en la tolva, mientras que las partículas más ligeras chocan con los deflectores y quedan atrapadas, cayendo al recipiente de recogida.
4.Cámara de polvo: El diseño de la cámara de polvo minimiza las interrupciones del flujo de aire. La cámara es cilíndrica y debe ser más alta que la entrada para garantizar una eliminación eficaz del polvo. El polvo cae a la tolva por gravedad, donde se acumula para facilitar su eliminación.
5.Tolva de polvo: Típicamente de forma cónica, la tolva dirige el flujo de aire principal hacia abajo, mejorando el movimiento en espiral del aire cargado de polvo. El ángulo de la tolva debe superar los 60° para facilitar la descarga del polvo.
6.Válvula de descarga: La válvula de descarga es esencial para eliminar el polvo acumulado. Debe diseñarse para que sea segura y fácil de usar, garantizando un cierre hermético para evitar fugas de aire, que pueden afectar significativamente a la eficacia.
Diseño y eficacia de la aplicación
El diámetro del colector ciclónico de polvo afectará a su eficacia. Cuanto menor sea el diámetro, menor será el radio de rotación y mayor la fuerza centrífuga, con lo que mejorará la eficacia de eliminación del polvo. Sin embargo, si el diámetro es demasiado pequeño, las partículas de polvo pueden chocar con la carcasa, reduciendo así la eficacia de eliminación del polvo. En general, el rango de diámetro óptimo es de 800 mm a 2500 mm. Otros factores, como el tamaño de las partículas, la viscosidad y la velocidad del flujo de aire, también afectan al rendimiento. La eficacia del ciclón tradicional se sitúa entre 60% y 75%. Un diseño mejorado (como el deflector) mejora la eficacia al aumentar la superficie de choque de las partículas, de modo que se capturan más partículas de polvo sin tratar.
En una palabra, el ciclón destaca en diversas aplicaciones industriales, especialmente en el entorno del procesamiento de granos, por su gran eficacia, sencillez y adaptabilidad.
Para más información sobre los separadores ciclónicos y cómo pueden beneficiar a sus operaciones, por favor Contacto. ¡Estamos aquí para ayudarte a encontrar las mejores soluciones para tus necesidades de captación de polvo!