As awareness of environmental protection and energy conservation grows, bulk cement, which is easy to transport and has low pollution with accurate measurement, has become one of the main building materials. However, the functions of silos de cemento have evolved from simple storage to include dust removal, arch breaking, and measurement. The arching phenomenon in cement silos is a common and challenging issue that needs urgent attention.
The Arching Phenomenon and Its Impact
The arching phenomenon occurs when cement forms a dome-shaped cavity at the outlet of the silo, preventing it from falling. This issue hinders the transportation of cement, disrupts the normal operation of the batching plant, and causes uneven feeding, which directly affects the accuracy of weighing and batching.
Causes of Arching
Several factors contribute to arching:
Internal Friction and Cohesion of Cement
These forces create shear stress and result in a certain overall strength that hinders particle movement and reduces flowability.External Friction of Cement
This refers to the friction between cement and the walls of the silo. It depends on the roughness of the walls and the angle of the conical section. Greater roughness and smaller angles increase external friction, making arching more likely.Temperature of External Air
Temperature and humidity affect the cohesion of cement, reducing its flowability and increasing the risk of arching.Hydraulics at the Silo Outlet
A smaller hydraulic radius at the outlet reduces the core flow area within the silo, making arching more likely.
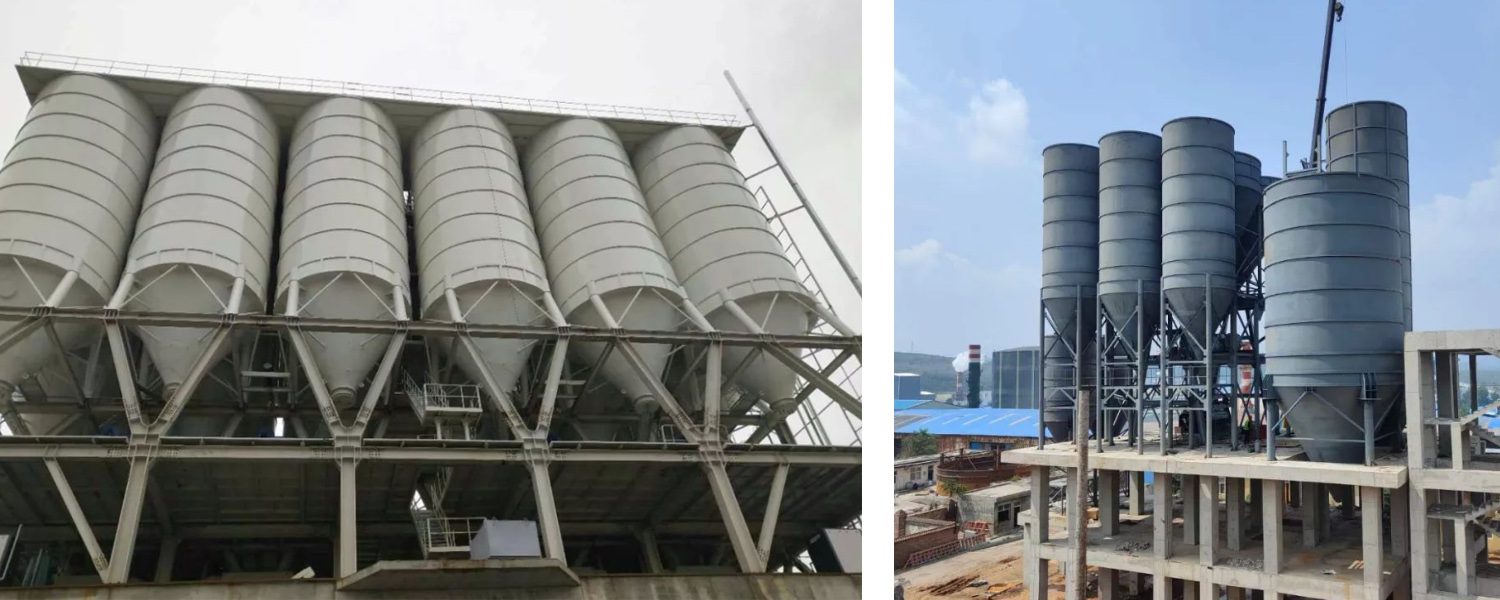
Preventive Measures
To effectively prevent arching in cement silos, we should take the following measures during design, construction, and operation:
1. Side Discharge Design
Using a side discharge design is an effective way to prevent arching. Adding more discharge points or using inclined discharge can reduce vertical pressure and help break the arch. Discharge points should be compatible with the transportation equipment. Too many discharge points increase costs and complicate operations.
2. Reduce Internal Friction
Design the silo with smooth internal walls to create optimal sliding conditions. While most silos use reinforced concrete, consider lining the funnel section with steel plates or applying coatings to reduce internal friction.
3. Control Moisture
Cement has high moisture absorption. Therefore, controlling moisture intrusion is crucial. Reduce moisture brought in by the cement itself, prevent rainwater infiltration, and limit moisture from pneumatic conveying systems.
4. Dehumidification and Drying of Compressed Air
During compression, moisture in the air condenses. Implement strict dehumidification measures to ensure that compressed air remains dry during storage, transport, and use. This prevents cement from clumping and arching.
5. Increase the Angle of the Conical Section
Set the angle of the conical section to be greater than the external friction angle of cement (approximately 32°) to reduce external friction. A typical range for this angle is between 55° and 65°.
6. Increase the Diameter of the Silo Outlet
Widening the outlet diameter helps improve the flowability of cement and reduces the occurrence of arching.
Conclusión
By applying these measures, we can effectively prevent arching in cement silos, enhance cement transportation efficiency, and ensure a stable supply of building materials. Continuous optimization of design and operational processes is essential to meet the growing market demand.
If you need high-quality cement silos or want to learn more, please Contacto. Darko will provide you with professional solutions and excellent service!