Introduction to Double Dump Valves
Double dump valves (also known as dual-flap valves o twin gate discharge valves) are essential components in powder and granular material handling systems. Widely used in cement plants, food processing, and metallurgy industries, these valves excel in:
✔ Make sure air doesn’t escape in pneumatic expressing systems.
✔ Ensuring continuous material flow control
✔ Providing airtight sealing for dust collection
1. Core Working Principle of Double Dump Valves
1.1 Basic Structure
Every double dump valve contains three critical components:
Upper and lower valve flaps (typically made of wear-resistant steel)
Heavy counterweight mechanism (for automatic flap reset)
Sealing gasket (usually food-grade rubber or PTFE)
1.2 Material Flow Process
The patented alternating flap system operates in 4 stages:
Upper flap opens – Material enters the intermediate chamber
Upper flap seals – Creates an airlock to prevent pressure loss
Lower flap discharges – Material exits by gravity
Lower flap resets – Counterweight ensures complete closure
Key Benefit: This sequential operation maintains constant system pressure while allowing uninterrupted material transfer – a critical advantage over rotary valves in high-pressure systems.
2. Electric Double Dump Valve Operation
2.1 Key Components
Part | Function |
---|---|
IP65-rated actuator | Weatherproof electric motor drive |
Chain/belt transmission | Converts rotary to linear motion |
Position sensors | Provides open/close feedback to PLC |
2.2 Working Cycle
Opening Sequence:
① Motor energizes → ② Gearbox rotates shaft → ③ Upper flap opens (0-90°) → ④ Time delay (2-5 sec) → ⑤ Lower flap opens
Closing Sequence:
① Lower flap seals → ② Upper flap closes → ③ Limit switch signals completion
Pro Tip: Electric models achieve <0.5% leakage rates when paired with inflatable seals for abrasive materials like fly ash.
3. Pneumatic Double Dump Valve Mechanism
3.1 Air Cylinder Operation
Single-acting cylinders (spring return) for compact installations
Double-acting cylinders for high-speed cycling (up to 60 cycles/minute)
3.2 Critical Sealing Technology
En cone-and-spring sealing system provides:
Primary seal: Metal-to-metal contact between flap and seat
Secondary seal: Compressible elastomer gasket (FDA-approved options available)
Industry Application: Particularly effective in explosive environments (ATEX Zone 22) where electric sparks must be avoided.
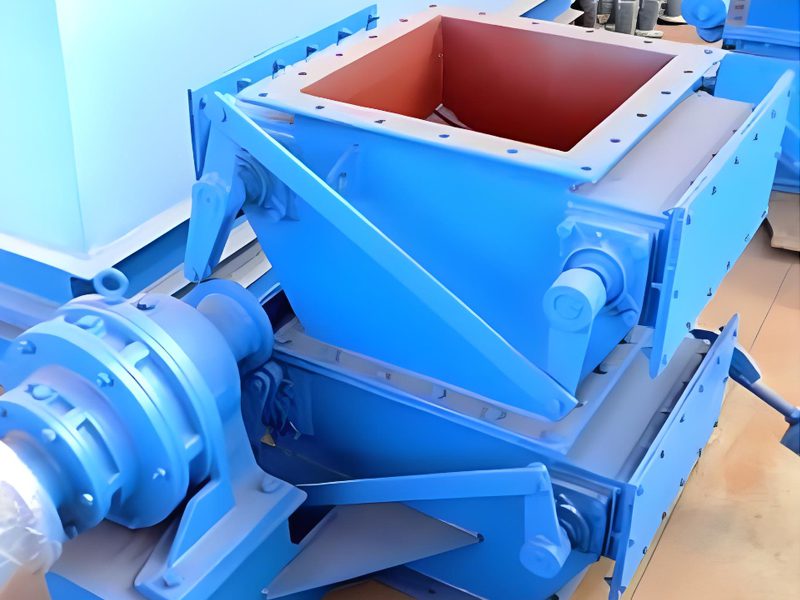
Comparative Analysis: Electric vs Pneumatic
Característica | Electric | Pneumatic |
---|---|---|
Response Time | 3-10 seconds | <1 second |
Mantenimiento | Annual lubrication | Quarterly diaphragm checks |
Uso de la energía | 0.5-2 kW | 4-6 CFM @ 80 psi |
Best For | Precise positioning | Rapid cycling |
Troubleshooting Common Issues
Problem 1: Material bridging
Solución: Instale vibrators o air cannons on valve body
Problem 2: Seal degradation
Diagnosis: Check for excessive play in linkage arms (>3mm indicates wear)
Problem 3: Incomplete closure
Fije: Adjust counterweight position or increase cylinder pressure by 10%
Industry-Specific Applications
✔ Cement Plants
Handles clinker dust at 300°C with water-cooled bearings
✔ Food Processing
316 stainless steel models with sanitary clamps meet USDA standards
✔ Power Generation
Explosion-proof versions for coal fly ash collection
FAQs (Featured Snippet Optimization)
Q: How often should double dump valves be maintained?
A: Perform visual inspections weekly y complete overhaul every 2,000 operating hours
Q: Can double dump valves handle sticky materials?
A: Yes, when equipped with Teflon-coated flaps y air purge connections
Q: What's the typical lifespan?
A: 5-7 years for standard models, 10+ years with hardened alloy components
Technical Specifications Table
Parameter | Range |
---|---|
Sizes | 4″ to 24″ diameter |
Temperatura | -40°F to 750°F |
Presión | Up to 15 PSI (standard) |
Materiales | Cast iron, SS304, SS316, AR steel |
For double dump valve selection consultation or technical support, please contact us.