La alta eficacia y el bajo consumo energético de la proceso de molienda del cemento siempre han sido los objetivos de las empresas de producción. "Mejorar la capacidad de molienda" es un tema constante. Nos esforzamos continuamente por mejorar la eficacia de molienda de molinos de bolas. Nuestro objetivo es reducir el consumo de energía de molienda y los costes de producción, logrando al mismo tiempo la máxima finura y rendimiento.
Con la aplicación de nuevas normas sobre el cemento, ahora hay mayores exigencias en cuanto a la finura del cemento, la superficie específica y la composición de las partículas. Las empresas cementeras suelen intentar aumentar la resistencia reduciendo la cantidad de materiales mezclados o aumentando la superficie específica del cemento. Sin embargo, la forma más sencilla de conseguir una mayor superficie específica es reducir el rendimiento del molino y aumentar el tiempo de molienda. Esto conduce a una "sobremolienda", que aumenta la cantidad de microfinos de menos de 3 micrómetros. La composición de las partículas se vuelve entonces pobre. Aunque la resistencia no mejora mucho, el consumo de energía de molienda aumenta significativamente.
Este método de reducir la producción y aumentar el tiempo de molienda para mejorar la finura del cemento o aumentar el contenido de clínker aumentará inevitablemente los costes de producción. Por lo tanto, debemos centrarnos en las modificaciones internas del molino, los materiales de pretrituración y la optimización de la clasificación de los medios de molienda para mejorar el contenido de partículas de 3-30 micrómetros y aumentar la resistencia del cemento.
Formas generales de mejorar la capacidad de los molinos de cemento
1. Reducir el tamaño de las partículas de los materiales entrantes
Reducir el tamaño de las partículas de los materiales entrantes (clínker) puede disminuir el consumo de energía por unidad de producto y mejorar la capacidad de molienda del cemento. El tamaño de las partículas de material entrante es un factor importante que afecta al rendimiento del molino. Las partículas más pequeñas disminuyen el diámetro medio de las bolas de acero. Con la misma carga, aumenta el número de bolas de acero, y también la superficie total. Esto aumenta el área de contacto entre las bolas de acero y el material, mejorando así la eficacia de la molienda. Así pues, adoptar un enfoque de "triturar más, moler menos" mediante la trituración previa puede reducir el consumo de energía y aumentar la capacidad del molino.
2. Ajustar la estructura interna del molino
Implantamos un proceso de trituración previa, que redujo el tamaño de las partículas de los materiales entrantes. Sin embargo, la capacidad de trituración no mejoró. Observamos un consumo de energía y una carga elevados en el clasificador O-Sepa, con una tasa de carga cíclica que alcanzaba los 240% y una eficacia de clasificación de sólo unos 25%. Un análisis granulométrico lo confirmó, mostrando una curva pronunciada en la primera cámara y una curva casi horizontal en la segunda.
Claramente, la fuerza de impacto en la primera cámara es demasiado fuerte, mientras que la capacidad de molienda en la segunda cámara es insuficiente. Para solucionarlo, añadimos 3 toneladas de pequeñas bolas de acero a la segunda cámara. Este ajuste aumentó la producción a unas 70 toneladas por hora. Para mejorar aún más, acortamos la longitud de la primera cámara de 5,35 metros a 4,85 metros. Desplazamos la placa divisoria hacia delante y aumentamos la longitud de la segunda cámara de 7,25 metros a 7,75 metros para aumentar la capacidad de la cámara de molienda fina y mejorar la eficacia. La primera cámara utiliza revestimientos escalonados curvados para aumentar la caída de las bolas de molienda y mejorar la capacidad de impacto. La segunda cámara emplea un revestimiento de doble curvatura para las funciones de clasificación y elevación, logrando una producción de 80 toneladas por hora, mejorando la eficacia y reduciendo el consumo de energía.
3. Reforzar el secado del material
Necesitamos mejorar el secado del material para mantener el contenido de humedad de los materiales entrantes entre 1-2%. El exceso de humedad durante el funcionamiento puede provocar la formación de bolas, afectando negativamente a la capacidad del molino.
4. Mejorar la ventilación interna
Una buena ventilación interna influye significativamente en la calidad y el rendimiento del producto. Una ventilación eficaz permite eliminar a tiempo el polvo fino para evitar la sobremolienda. También evacua el calor generado durante la molienda, bajando la temperatura interna y reduciendo la posibilidad de deshidratación del yeso y de obstrucciones. Una buena ventilación reduce las capas amortiguadoras dentro del molino y acelera los caudales, aumentando el rendimiento del molino. Sin embargo, una ventilación excesiva puede agrandar las partículas de polvo, afectando negativamente a la finura del cemento. Cuando la ventilación supera un determinado nivel, puede aumentar el consumo de energía por unidad. La práctica demuestra que existe un volumen de ventilación óptimo entre el rendimiento máximo del molino y el consumo mínimo de energía.
Normalmente, la velocidad del viento interno de los molinos de circuito cerrado es de 0,8-1,0 m/s, mientras que los molinos de circuito abierto requieren velocidades del viento más altas debido a las temperaturas más elevadas. Si el molino de bolas tiene problemas de ventilación, podemos mejorarlo abriendo orificios de ventilación en la entrada de alimentación y dando forma escalonada al conducto de descarga. También podemos agrandar el orificio central de la placa divisoria y la rejilla de descarga, mejorando el aire de bloqueo en el puerto de descarga. Estas medidas solucionan la obstrucción de material y aumentan el área de ventilación.
5. Determinar razonablemente la finura objetivo de los productos de cemento
En la producción real, si la finura objetivo de los productos de cemento se fija demasiado alta, puede anular los efectos de otras medidas. Esta restricción limita el rendimiento del molino y obstaculiza los esfuerzos por reducir el consumo de energía. Por tanto, es esencial determinar la finura objetivo de los productos de cemento basándose en las condiciones reales.
6. Optimizar la carga de las bolas de acero
Aumentar el número de bolas de acero en el molino incrementa la superficie de contacto entre las bolas de acero y el material, lo que aumenta el rendimiento del molino. Reducir el diámetro de las bolas de acero aumenta la superficie por unidad de volumen, lo que también eleva el rendimiento del molino. Sin embargo, el consumo de energía tiende a aumentar con la cantidad de bolas de acero cargadas. Generalmente, dentro de un cierto rango, el consumo de energía es proporcional a la cantidad de bolas de acero e inversamente proporcional a su diámetro. Sin embargo, una carga excesiva aumenta las colisiones y la eficacia de la molienda, lo que conlleva un mayor consumo de energía. El molino debe tener una carga óptima de bolas de acero que minimice el consumo de energía, que debe determinarse mediante ensayos de las relaciones de carga y el diámetro de bolas óptimos.
7. El papel de las ayudas a la molienda
Añadir una pequeña cantidad de ayuda a la molienda durante el proceso de molienda puede eliminar la adherencia y aglomeración de los polvos finos. Esto acelera el proceso de molienda, mejorando la eficacia y la calidad y reduciendo al mismo tiempo el consumo unitario de energía. El uso de coadyuvantes de molienda puede dar lugar a productos con mayores áreas de superficie específica y reducir los casos de sobremolienda. Además, aumenta el caudal de materiales dentro del molino, lo que acorta el tiempo de residencia y afecta a la finura del producto. En la molienda en circuito abierto, debemos ajustar las condiciones internas para satisfacer los requisitos de finura del producto. En la molienda en circuito cerrado, debemos mantener la finura de salida dentro de los rangos normales, evitando cualquier aumento gradual del residuo de tamiz. De lo contrario, esto podría reducir el rendimiento del molino y aumentar la tasa de carga cíclica, lo que provocaría una sobrecarga del elevador y bloqueos, pudiendo causar paradas de producción. En resumen, seleccionar y utilizar los auxiliares de molienda es una tarea científica rigurosa. Debemos considerar cuidadosamente los cinco puntos siguientes:
Ten en cuenta las propiedades de los materiales entrantes y realiza pruebas comparativas a pequeña escala. La eficacia de los coadyuvantes de molienda varía según el material, por lo que, para conseguir resultados óptimos, primero debemos realizar pruebas a pequeña escala en condiciones técnicas específicas y luego aplicar las mejores soluciones a mayor escala.
Presta atención a las condiciones de molienda y selecciona distintos tipos de coadyuvantes de molienda. Los coadyuvantes de molienda se presentan en forma gaseosa, sólida y líquida con diversos tipos. Su adaptabilidad y eficacia varían, y los requisitos difieren entre circuitos abiertos y cerrados, lo que exige pruebas cuidadosas.
Asegúrate de que el uso de coadyuvantes de molienda no afecte negativamente a los procesos posteriores. Al utilizar coadyuvantes de molienda en las fábricas de cemento, ten en cuenta su impacto en el envasado, los procesos de manipulación a granel, la construcción y la calidad de los productos de cemento.
Centrarse en la fuente y el coste de los auxiliares de molienda. Los beneficios económicos de los auxiliares de molienda están estrechamente relacionados con su precio y el suministro del mercado. Las empresas deben evaluar y calcular estos factores antes de tomar decisiones óptimas.
Asegúrate de que los coadyuvantes de molienda cumplen las normas de protección del medio ambiente. Muchos aditivos se formulan utilizando subproductos de plantas químicas, que a menudo contienen sustancias nocivas. Al seleccionar los auxiliares de molienda, no te dejes engañar por los precios bajos; asegúrate de que los auxiliares no contaminan el medio ambiente ni perjudican la salud de los trabajadores. En la práctica, los coadyuvantes de molienda funcionan mejor en las grandes fábricas de cemento. Dados sus costes más elevados, para determinar su uso deben sopesarse las ventajas de reducir el consumo de energía y aumentar la producción.
8. Optimización de la estructura y los parámetros técnicos del clasificador
Las tecnologías clave del clasificador son la "dispersión", la "clasificación" y la "recogida". Dispersión significa que el material que entra en el clasificador debe dispersarse lo más posible, creando espacio entre las partículas. Así, el diseño de la placa de dispersión, su velocidad, el espacio de dispersión, el contenido de humedad de los materiales y el caudal afectan directamente a la velocidad de dispersión. La clasificación consiste en utilizar el flujo de aire para separar las partículas gruesas de las finas durante su tiempo limitado en el clasificador. Factores como el caudal de gas, la velocidad del aire, los patrones de flujo de aire, los puntos de interacción gas-sólido y la configuración del propio clasificador influyen significativamente en la eficacia de la clasificación. La recogida se refiere a la capacidad del clasificador para capturar polvos gruesos y finos, que depende del método de recogida y del diseño de los componentes de recogida.
En 1979, la empresa japonesa Onoda desarrolló el clasificador O-Sepa. Este clasificador conserva las ventajas de los clasificadores ciclónicos, pero emplea un rotor de jaula con un principio de clasificación de flujo de aire en espiral planar, lo que mejora significativamente la eficacia de la clasificación. Representado por el clasificador de tipo jaula, se conoce como clasificador de alta eficacia y se considera la tercera generación de clasificadores tras los clasificadores centrífugos y de ciclón.
Su eficacia de clasificación suele superar la 80%. Sin embargo, no incluye un dispositivo de recogida de polvo fino y requiere filtros de mangas más grandes o colectores de polvo eléctricos, lo que aumenta la inversión en equipos y complica la disposición de los procesos, lo que limita su adopción generalizada. El clasificador O-Sepa, junto con colectores de polvo de bolsa de alta eficiencia y molinos de bolas, reduce las cargas cíclicas de 200%-300% en sistemas centrífugos a 100%-200%. Al moler cemento, puede conseguir más de 65% de distribución de partículas en el rango de 3-30 micrómetros, lo que da como resultado una alta eficacia de clasificación, un bajo consumo de energía, un alto rendimiento y una distribución razonable de las partículas.
9. Aumenta adecuadamente la velocidad de la fresadora
Aumentar la velocidad es especialmente eficaz para los molinos más pequeños. Estos molinos tienen fuerzas de impacto más débiles debido a sus diámetros más pequeños. Aumentar la velocidad mejora la capacidad de trituración del molino:
- Aumentar el número de impactos en cada medio de molienda dentro del molino.
- Aumentar la fricción y la acción de molienda entre los medios de molienda y entre éstos y el revestimiento.
10. Bajar la temperatura del clínker entrante
Reforzar la gestión del material. Deben hacerse ajustes en función de la temperatura del clinker en la zona de almacenamiento. Los operarios deben seguir estrictamente las normas y ser evaluados en consecuencia. Utiliza termómetros para controlar las temperaturas y evitar que entre clinker a alta temperatura en el molino.
Implementa la pulverización de agua en la nevera. El agua debe pulverizarse en el centro del enfriador utilizando tubos galvanizados con pequeños orificios para controlar el flujo de agua entre 500-600 kg/h. Esto puede reducir la temperatura del cemento saliente aproximadamente un 10℃.
Aunque estas medidas de pulverización reducen eficazmente las temperaturas, tienen efectos secundarios. El vapor de agua puede arrastrar polvo de clínker al interior de la trituradora en el extremo del enfriador, formando aglomeraciones en las paredes interiores, lo que a la larga puede perturbar el funcionamiento normal de la trituradora. Por tanto, controla regularmente la temperatura del clínker y ajusta el rociado de agua en consecuencia. Limpia periódicamente la trituradora de clínker.
11. Características y triturabilidad de los materiales entrantes
Los tipos y proporciones de los materiales entrantes afectan directamente al rendimiento del molino, la calidad y el consumo específico de energía. Cualquier material mezclado que se utilice en el cemento reducirá generalmente la resistencia, pero el grado de reducción varía en función de la actividad de los materiales. Entre los materiales mezclados más utilizados, la escoria tiene la actividad más alta.
Sin embargo, si la superficie específica de la escoria es inferior a 300 m²/kg, sus ventajas en la resistencia del cemento no se manifiestan. La molturabilidad de los materiales influye significativamente en el rendimiento del molino y en la calidad del producto. Las normas nacionales definen coeficientes de molturabilidad basados en la energía específica necesaria para la molienda. Como la mayoría de las empresas carecen de equipos de ensayo especializados, las pruebas de molienda a pequeña escala comparando los materiales con arena estándar pueden ayudar a determinar los parámetros del proceso de molienda. Tras medir los coeficientes de molturabilidad de las materias primas y combustibles, podemos ajustar la carga y la graduación de los medios de molienda basándonos en métodos científicos.
El coeficiente de triturabilidad está estrechamente relacionado con la estructura del material. Incluso dentro de un mismo material, los coeficientes de triturabilidad pueden variar. Por ejemplo, la piedra caliza densa y bien cristalizada tiene un coeficiente de triturabilidad bajo y es más difícil de moler. La triturabilidad del clínker depende de la composición de sus minerales y del ambiente de enfriamiento. Las pruebas demuestran que unos valores elevados de KH y P, un alto contenido de C3S, un bajo C4AF y un enfriamiento rápido producen una textura más quebradiza y unos coeficientes de triturabilidad más elevados. Por el contrario, los valores bajos de KH y P, los contenidos altos de C2S y C4AF y el enfriamiento lento dan lugar a clinkers más densos y resistentes, con coeficientes de triturabilidad más bajos, lo que los hace más difíciles de moler.
Los coeficientes de triturabilidad de la escoria pueden variar significativamente. La escoria que sufre un enfriamiento rápido después de ser producida suele ser porosa y fina, lo que da lugar a un coeficiente de triturabilidad más alto, de aproximadamente 1,2-1,3. Por el contrario, la escoria que se enfría mucho antes de enfriarse rápidamente forma partículas cristalinas más densas y pesadas, lo que da lugar a un coeficiente de triturabilidad más bajo, de aproximadamente 0,7-0,9, que dificulta su trituración.
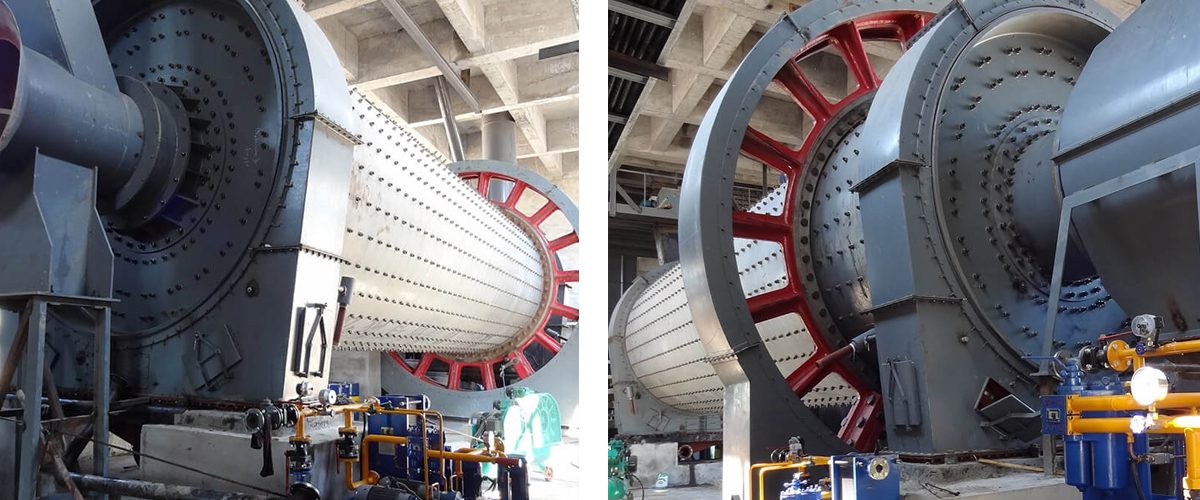
Otras formas de mejorar la capacidad de los molinos de cemento
1. Base para un ajuste razonable de los medios de molienda
El ajuste razonable de los medios de molienda depende de las propiedades físicas y químicas de los materiales molidos, del método de molienda y de la finura requerida del producto. El análisis de los residuos de tamizado es un medio eficaz para juzgar si la clasificación de los medios de molienda es razonable.
La base para ajustar los medios de molienda incluye
- Cuando el tamaño de las partículas de los materiales entrantes es fijo, las bolas de acero más pequeñas tienen una superficie total mayor que las bolas de acero más grandes, lo que aumenta sus oportunidades de contacto con los materiales. A la inversa, las bolas de acero más grandes proporcionan mayor energía y capacidad de trituración por impacto. Para materiales con tamaños medios de partícula más grandes y mayor dureza, deben utilizarse diámetros medios de bolas más grandes; para materiales más blandos, son adecuados diámetros más pequeños. Para molinos de menor diámetro, se utilizan diámetros medios de bola más pequeños.
- Si la triturabilidad de los materiales entrantes es buena, pueden seleccionarse bolas de acero pequeñas; si la triturabilidad es mala, son necesarias bolas de acero más grandes.
- La selección del diámetro de las bolas también está relacionada con la cantidad de material que pasa por el molino por unidad de volumen. En la molienda en circuito cerrado, el retorno de partículas gruesas aumenta el rendimiento por unidad de volumen, permitiendo cierta amortiguación de las bolas de acero durante el impacto. Por lo tanto, se prefieren bolas de acero más grandes en escenarios de alto retorno, mientras que en otros casos se seleccionan bolas más pequeñas.
- Si el requisito de finura de salida es fino, deben utilizarse bolas de acero pequeñas; en caso contrario, son adecuadas las grandes.
- Los molinos de una sola cámara suelen utilizar bolas de acero, mientras que los molinos de dos cámaras suelen utilizar bolas de acero en la primera cámara y secciones de acero en la segunda.
- Los tamaños de los medios de molienda deben estar bien ajustados. Las especificaciones de las bolas de acero suelen oscilar entre 3 y 5 niveles, mientras que las de los perfiles de acero oscilan entre 2 y 5 niveles.
- La proporción de bolas de acero de distinto tamaño puede seguir el principio de "pequeño en ambos extremos, grande en el centro". Cuando utilices dos tipos de secciones de acero, cada una debe ocupar la mitad.
- Al tiempo que se cumplen los requisitos de tamaño de las partículas, el tamaño medio de éstas debe reducirse al mínimo para aumentar el área de contacto y la frecuencia de impacto, y la relación entre el diámetro y la longitud de las secciones de acero debe mantenerse pequeña debido al rápido desgaste radial. La diferencia entre la longitud y el diámetro de las secciones de acero debe ser de unos 5 mm.
2. Ajustar razonablemente la tasa de retorno y la clasificación de los medios de molienda
En general, para reducir el exceso de molienda, la tasa de llenado de la primera cámara en la molienda en circuito cerrado suele ser mayor que la de la segunda cámara, lo que acelera el flujo de material. Una tasa de retorno de 100-150% suele producir el mayor rendimiento por hora. Si la tasa de retorno es demasiado alta, aunque la finura cumpla las normas, la superficie específica disminuye. A medida que los medios de molienda se desgastan durante la producción, disminuye la tasa de llenado. Al principio, esto no se observa como una disminución de la producción horaria, sino como un aumento de la tasa de retorno, una reducción de la superficie de cemento y un descenso de la resistencia a la compresión a los 3 días. Cuando la tasa de retorno es demasiado alta, se produce una sobresaturación, que a su vez provoca un descenso de la producción horaria. Por tanto, es esencial determinar si hay que suplementar los medios de molienda en función de los índices de retorno y las áreas de superficie específicas. Si el rendimiento por hora disminuye significativamente, es necesario vaciar el molino y rehacer la clasificación de las bolas de molienda.
3. Medios de molienda en cámaras de molienda fina
Los medios de molienda son una de las principales medidas para optimizar el molino. Actualmente, los molinos de cemento extranjeros en cámaras de molienda fina tienden a utilizar bolas de acero pequeñas en lugar de secciones de acero, porque las secciones de acero consumen unos 20-30% más de energía.
Las bolas pequeñas de acero de alta calidad se desgastan menos que las secciones de acero y producen partículas de cemento más esféricas, superiores a las producidas por las secciones de acero. Sin embargo, las secciones de acero tienen sus ventajas, como un flujo de material más rápido y la prevención de la aglomeración del cemento en el molino. En los últimos años, ha habido un debate permanente sobre si utilizar secciones de acero o bolas de acero en las cámaras de molienda fina. Algunos abogan por las secciones de acero, mientras que otros prefieren las bolas de acero. Esta decisión requiere un análisis específico desde el punto de vista de la molienda. La función de molienda del molino abarca tanto la trituración como la molienda. Optimizar las condiciones del molino implica equilibrar estas dos capacidades para mejorar la eficacia de la molienda, garantizando que tanto el rendimiento como la finura del producto se sitúen en niveles aceptables. Analizar correctamente la adecuación de las capacidades de trituración y molienda en distintas condiciones es crucial para determinar si utilizar secciones de acero o bolas de acero en las cámaras de molienda fina.
- Cada cámara del molino posee funciones tanto de trituración como de molienda, aunque en distinta medida. La función principal de la cámara de molienda fina es la molienda, y las capacidades de molienda de las bolas de acero pequeñas y las secciones son diferentes. La eficacia de la molienda depende principalmente de la superficie de contacto entre las bolas y los materiales. Una mayor superficie de contacto proporciona más oportunidades de molienda, lo que conduce a mayores tasas de generación de producto en una unidad de tiempo. A igualdad de calidad, las secciones tienen una mayor superficie de contacto debido a su naturaleza de contacto lineal, en comparación con las bolas. Para cámaras individuales, con la misma carga de bolas de molienda y el mismo material de alimentación, el rendimiento por unidad de tiempo en una cámara de secciones es mayor que en una cámara de bolas, como demuestran la teoría de la molienda y la aplicación práctica. Cabe señalar que los tamaños actuales de los medios de molienda en las cámaras de molienda fina suelen ser demasiado grandes en comparación con los materiales, en parte debido a las restricciones en la anchura de los tamices.
Conclusión
La práctica ha demostrado que las principales vías para conseguir una molienda de cemento de alta calidad, energéticamente eficiente y de alto rendimiento incluyen: "añadir procesos de pre-trituración antes de la molienda, realizar mejoras estructurales dentro del molino y seleccionar clasificadores eficientes después de la molienda". La pretrituración es el "requisito previo", las modificaciones internas son los "cimientos" y la selección óptima después de la molienda es la "garantía". Para más información o consultas Contacto!