El consumo energético de los sistemas de molienda es un indicador clave de su rendimiento. Actualmente, la tecnología de molienda está evolucionando hacia sistemas completos sin bolas, como molinos verticales or roller presses, and larger equipment. With advancements in cement technology, the overall energy consumption in cement production shows the following trends:
- Molino de bolas Era: Más de 100 kWh/t
- Era de trituración parcial de la cama: Unos 90 kWh/t
- Era sin pelotas: Por debajo de 80 kWh/t
Esta tendencia indica que la tecnología de molienda está mejorando continuamente para conseguir un menor consumo de energía y una mayor eficacia de producción.
Métodos para reducir el consumo de energía en los sistemas de molinos de bolas
1. El impacto de los materiales en el consumo energético del sistema de molienda
1.1 El efecto de la triturabilidad del material
El rendimiento del sistema de molienda de cemento está estrechamente relacionado con la molturabilidad del clínker. La composición mineral y la velocidad de enfriamiento del clínker afectan a su molturabilidad. Por ejemplo, los clínker con alto contenido en C3S y bajo contenido en C4AF suelen presentar una buena molturabilidad. Por el contrario, los clinkers con alto contenido en C2S y C4AF conllevan un mayor consumo de energía. Por tanto, optimizar la composición mineral y las condiciones de enfriamiento del clínker reduce eficazmente el consumo de energía.
1.2 El impacto del tamaño de las partículas de material
Reducing the particle size of the feed material significantly increases the mill’s yield, thereby lowering energy consumption. When the average particle size of the feed material decreases from 30 mm to 2 mm–3 mm, the mill’s yield can increase by over 50%. Additionally, employing a “more crushing, less grinding” pre-crushing process effectively minimizes over-grinding and improves mill efficiency.
1.3 El impacto de la temperatura y la humedad del material
Cuando la temperatura del material de alimentación supera los 80 °C, la temperatura interna del molino puede superar los 120 °C, lo que reduce la eficacia de la molienda y aumenta el consumo de energía. Por tanto, es esencial controlar la temperatura del clínker y mantener el contenido de humedad entre 1,0% y 1,5% para garantizar un funcionamiento estable del molino.
2. El impacto de la ventilación de las fábricas en el consumo de energía
Aumentar la ventilación dentro del molino reduce los efectos de amortiguación y aumenta la velocidad del flujo de material, con lo que disminuye la temperatura y aumenta el rendimiento del molino. La velocidad del flujo de aire dentro del molino debe mantenerse entre 0,9 y 1,1 m/s para evitar la sobremolienda y el aumento del consumo de energía. Además, mejorar el sellado del sistema para reducir las fugas de aire es crucial para disminuir el consumo de energía.
3. Mantenimiento e inspección periódicos del molino
Revisar y mantener regularmente el molino y optimizar parámetros como la carga de bolas, la tasa de llenado y la eficiencia de selección pueden ayudar a mantener la estabilidad del sistema y una alta eficiencia operativa. Es necesario ajustar correctamente la configuración del cuerpo de molienda para conseguir un rendimiento óptimo del molino.
4. El impacto de la distribución granulométrica en la calidad del producto y el consumo de energía
La distribución granulométrica óptima para el cemento oscila entre 3 μm y 32 μm, con partículas finas que no superen 10%. El análisis periódico de la distribución granulométrica ayuda a ajustar oportunamente la carga de las bolas, mejorando la eficacia del molino y reduciendo el consumo de energía.
Optimización de los sistemas combinados de molienda
En los sistemas tradicionales de molienda combinada, las prensas de rodillos y los molinos de bolas realizan tareas de molienda diferentes. Optimizando la gestión de los molinos de bolas, podemos reducir eficazmente el consumo de energía y mejorar la calidad del cemento.
- Ventajas de las prensas de rodillos: Aumentar la presión de trabajo de la prensa de rodillos aumenta significativamente el rendimiento en condiciones de funcionamiento estables.
- Aumento de la superficie total de las bolas de acero: Ajustar el diámetro y la cantidad de bolas de acero aumenta la capacidad de molienda del molino, mejorando así la eficacia de la molienda.
- Ajuste de la estructura del molino: Shortening the coarse grinding chamber and extending the effective length of the fine grinding chamber helps improve the mill’s fine grinding capability.
Métodos para reducir el consumo de energía en los sistemas de molinos verticales
Los molinos verticales son equipos de molienda eficientes y que ahorran energía. Su consumo de energía procede principalmente del motor principal y del ventilador de circulación. Aquí tienes sugerencias para reducir el consumo de energía en los sistemas de molinos verticales:
1. Selección de los parámetros energéticos óptimos
Los operadores deben ajustar los parámetros operativos basándose en las tendencias de los parámetros del sistema para conseguir un alto rendimiento y un bajo consumo de energía.
2. Uso racional del caudal de aire del sistema
Controlar el flujo de aire del molino y minimizar las fugas de aire puede reducir eficazmente el consumo de energía del ventilador de circulación.
3. Ajuste del anillo de retención del material
Comprobar y ajustar periódicamente la altura del anillo de retención de material evita un rectificado ineficaz debido a un grosor inadecuado de la capa de material.
4. Aumentar el rendimiento y la tasa de funcionamiento de los equipos
Garantizar el funcionamiento continuo de los equipos y evitar paradas innecesarias ayuda a mejorar la estabilidad y a reducir el consumo de energía.
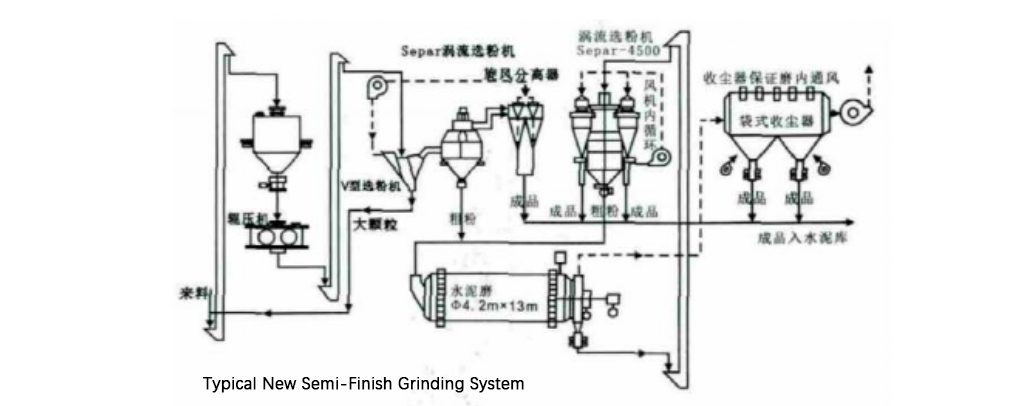
Conclusión
Todos los procesos y pasos de la producción de cemento tienen potencial para reducir el consumo de energía. Optimizando el sistema de molienda de forma integral, podemos reducir significativamente el consumo de energía, reducir los costes de producción y mejorar la competitividad en el mercado. Como profesionales de la industria del cemento, dominar las tecnologías y los métodos de gestión que ahorran energía contribuirá a alcanzar los objetivos del desarrollo sostenible.
Para más información o consultas, no dudes en Contacto.