Les convoyeurs réversibles répondent principalement au besoin de transporter des matériaux dans les deux sens, avant et arrière. Ils sont largement utilisés pour le transport sur de courtes distances. Cependant, lorsque la distance de transport est plus longue, les limitations techniques réduisent leurs applications. En 2022, l'entreprise C propose d'utiliser un convoyeur à glissière pneumatique réversible d'une capacité de 300t/h et d'une distance de 70 mètres pour le stockage de poudre minérale. Bien que Darko ait une certaine expérience des convoyeurs réversibles à courte distance. convoyeurs à glissière d'airC'est la première fois que nous essayons d'obtenir une telle capacité et une telle distance avec plusieurs points de décharge. Par conséquent , Darko s'est concentrée sur les questions techniques suivantes :
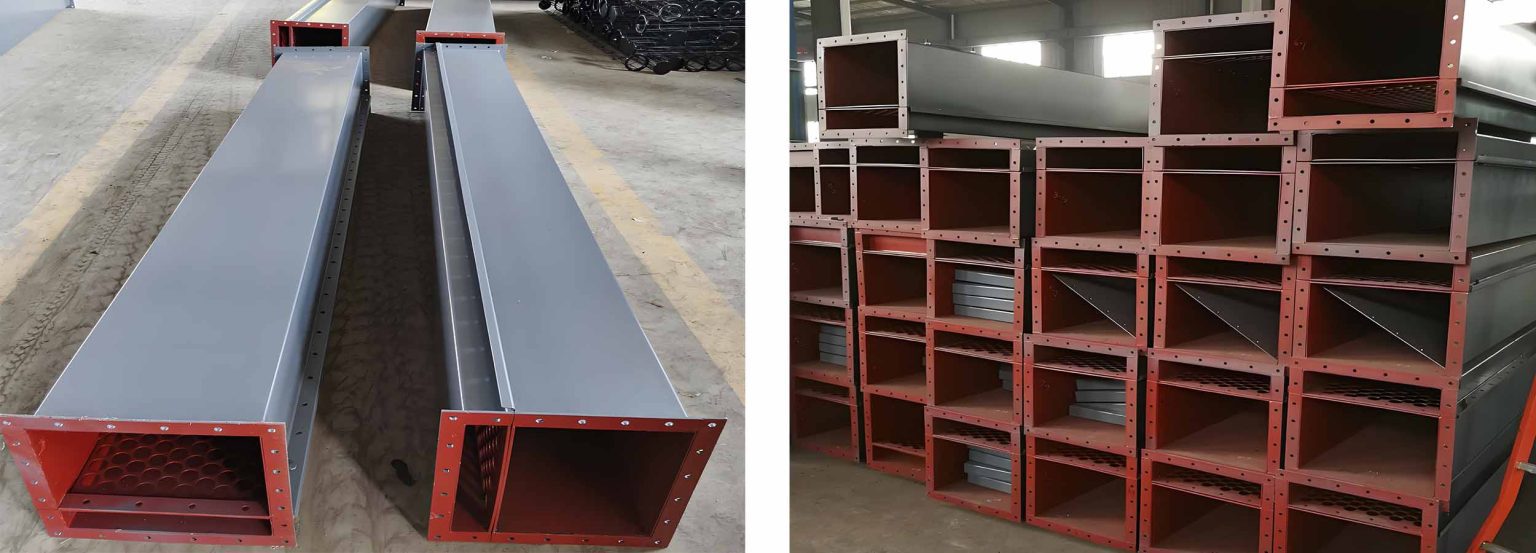
1. Conception du système d'entraînement
Tout d'abord, nous avons déterminé que l'entraînement devait se trouver à une extrémité du convoyeur. Cette conception évite d'avoir deux entraînements aux deux extrémités, ce qui simplifie le fonctionnement. Lorsqu'une extrémité est entraînée, l'autre reste inactive. Cette configuration réduit le risque d'accidents mécaniques et assure une production sans heurts.
Ensuite, nous avons envisagé de placer l'entraînement au milieu. Cependant, nous avons constaté que cela compliquerait la structure et augmenterait le stress sur la chaîne, réduisant ainsi sa durée de vie. Nous avons donc décidé de placer l'entraînement à une extrémité pour plus de simplicité.
2. Tension de la chaîne
Une fois que nous avons choisi l'entraînement à une extrémité, la tension de la chaîne est devenue critique. La longue distance de transport nécessite une tension efficace. Nous avons opté pour un système de tension arrière, qui comprend une tension par poids et une tension par vis. Après évaluation, nous avons choisi une méthode de tension arrière simple pour minimiser l'usure et prolonger la durée de vie de la chaîne et des composants.
3. Traitement de la transition de la chaîne
Après avoir choisi les méthodes d'entraînement et de tension, nous nous sommes concentrés sur la gestion des transitions de la chaîne. Une mauvaise gestion des transitions peut entraîner des blocages de chaîne et affecter le fonctionnement normal. Dans le cas d'un fonctionnement réversible, nous devons gérer la tension des chaînes supérieure et inférieure. Nous avons donc ajouté une structure de transition entre le pignon d'entraînement et la chaîne inférieure pour assurer un fonctionnement sans heurts.
4. Conception de la décharge intermédiaire
Le convoyeur à glissière pneumatique réversible est installé en haut de l'installation de stockage, principalement pour l'entrée des matériaux. Il doit donc s'adapter à plusieurs points de décharge. Pour éviter les blocages, nous avons installé des ouvertures de décharge au milieu et veillé à ce que l'ouverture située sous le pignon d'entraînement soit toujours ouverte. Cette conception permet de gérer différents types de matériaux et d'éviter les mélanges, qui peuvent nuire à la qualité des produits. Nous avons mis en place un soufflage d'air à haute pression aux points de décharge intermédiaires pour résoudre efficacement ce problème.
Conclusion
Grâce à l'optimisation de la conception du convoyeur à glissière d'air réversible, Darko répond aux besoins de transport de grande capacité et de longue distance tout en assurant un fonctionnement stable et une entrée efficace des matériaux. Nous nous engageons à fournir des solutions de haute qualité pour améliorer l'efficacité de la production. Pour plus d'informations, n'hésite pas à nous contacter.