Industrial work creates a lot of dust. When dust accumulates and encounters an ignition source, it can lead to catastrophic explosions. To keep things safer in areas with lots of dust, using Explosion-Proof Dust Collectors is crucial. These systems are essential for effective explosion prevention and enhancing safety in dust-prone environments.
What Are Explosion-Proof Dust Collectors?
Explosion-Proof Dust Collectors are specially designed for environments where explosive dust may be present. Their primary function is to control dust generated during industrial processes and maintain a clean workspace. These collectors not only prevent injuries from dust explosions but also confine the impact of potential explosions.
Typically, explosion-proof models take action before an explosion occurs. They can quickly reinforce structures or extinguish sparks. Unlike standard dust collectors, atex filters include various safety features. These features ensure safe operation in hazardous environments, such as explosion-proof motors and valves that prevent dust and harmful gases from entering electrical systems.
Darko's Atex Dust Collectors
Darko offers ATEX-compliant dust collection systems that ensure safety in flammable environments. Their dépoussiéreurs can be customized to meet your needs. The experienced team will work closely with you to develop tailored dust solutions that fit your unique requirements.Contact our experts to learn learn how to prevent dust explosions.
Design Principles of Explosion-Proof Dust Collectors
1. Pressure Relief Device Design
The goal of explosion-proof design is to extinguish combustible explosions at their initial stages. The pressure relief device in the dust collector manages this situation effectively. The relief pressure should be set to half of the dust collector’s design pressure, typically between 5-7.5 kPa. When pressure reaches 10 kPa, operators must activate the relief mechanism.
To help with pressure relief, the device should be tilted just a little, so air doesn’t get in. This design allows gravity to assist in automatic resetting. Sufficient space must be reserved for relief outlets, connecting to external safety systems.
2. Explosion Venting Device
The explosion venting device is important for keeping the production process safe. Install platforms and railings under the venting devices as well.These areas must be accessible only during maintenance and marked with warning signs.
3. Airflow, Pressure, and Velocity Determination
The dust collector’s intake system consists of ductwork and airflow regulation valves. During design, consider the negative pressure resistance of duct walls. The airflow regulation valve is a standard component, with thickness generally around 5 mm. The main duct airflow velocity should effectively reduce dust concentration, preventing buildup. For wood dust, the main duct speed should be no less than 20 m/s, while for magnesium-aluminum dust, it should be at least 23 m/s.
4. Use of Inerting Systems
When you’re using inert gases in dust collectors, it’s really important to keep an eye on the oxygen levels inside. The airflow into the collector should not exceed 50% of the lower explosion limit. Inerting systems should have monitoring capabilities to trigger alarms in case of anomalies.
5. Automation and Alarm Integration
Automation and alarm integration are essential features of explosion-proof systems. These systems automatically detect potential hazards and relay alarm information to central control systems, minimizing the risk of dust explosions.
Considerations for Dust Collectors in Flammable Environments
In places where there’s flammable dust, it’s really important to step up fire and explosion safety measures. Dust collectors must receive special treatment to bolster their explosion-proof capabilities. Common flammable dusts include flour, coal dust, wood chips, and certain metals under specific conditions.
To ensure safe operation, dust collectors must maintain reliable sealing to prevent air intake or gas leakage. The design of dust collectors should adhere to principles that enhance their explosion-proof capabilities:
Safety Measures for Dust Collectors
Structural Design: Bag dust collectors for combustible gases should ideally be round to promote smooth dust flow and prevent accumulation.
Fireproof and Explosion-Proof Materials: Use specially designed fireproof and explosion-proof filter bags, and incorporate pressure relief systems.
Continuous Dust Cleaning: Ensure regular dust cleaning to avoid sediment buildup.
Safety Valves in Dust Collector Systems
Duct Design: Minimize dead spots in ducts to maintain airflow and increase speed, preventing gas stagnation.
Emergency Relief Valves: Install safety valves in the ductwork before the fan to allow for quick pressure relief in case of gas explosions. The upper safety valve should be positioned at the top of the duct.
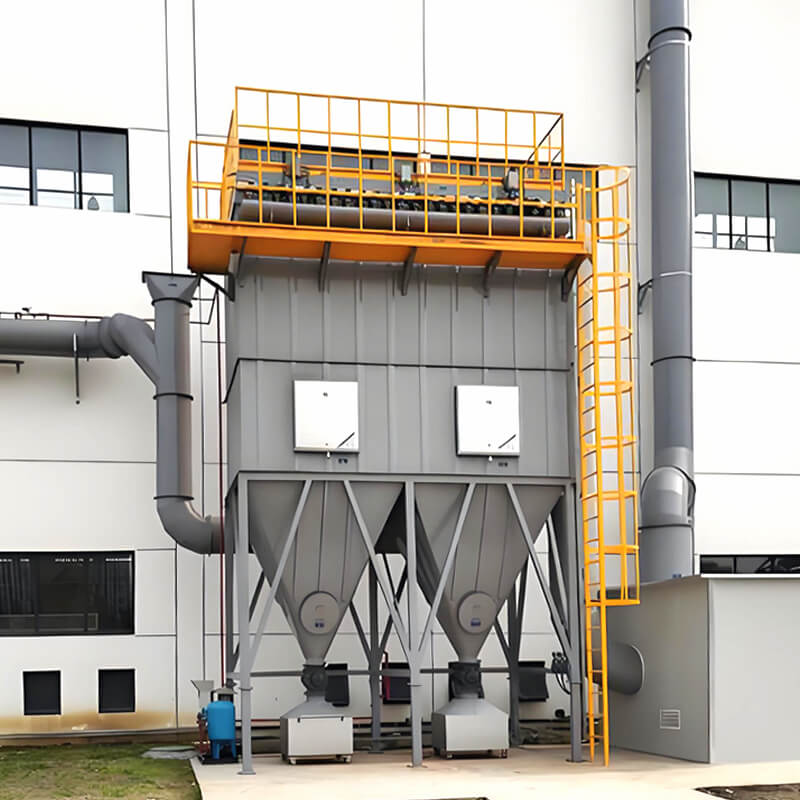
Conclusion
Improving the safety features of dust collection systems is really important when dealing with flammable dust, as it helps prevent accidents. Key strategies include maintaining airtight seals, designing circular dust collectors for efficient airflow, using fireproof materials, and implementing regular dust cleaning protocols.
If you need explosion-proof products or customized industrial dust solutions, please contact Darko! Our team is ready to assist you.