Dans la production moderne de ciment, le bon fonctionnement de transporteur pneumatique à glissière est cruciale. Récemment, une cimenterie a rencontré plusieurs incidents de blocage au cours d'opérations d'essai. Ces problèmes ont eu de graves répercussions sur la production normale. Cet article explore les causes de ces blocages et les solutions mises en œuvre.
Qu'est-ce qu'un convoyeur à air comprimé ?
Un convoyeur à glissière d'air est un système de manutention de produits en vrac qui utilise une couche d'air pour transporter des matériaux secs et poudreux le long d'un canal incliné. Il comporte une surface poreuse qui permet à l'air de circuler, créant ainsi un lit fluidisé qui permet de déplacer les matériaux en douceur et sans à-coups. Ce système est économe en énergie et couramment utilisé dans des industries telles que le ciment et la transformation des aliments.
Comment fonctionnent les convoyeurs à glissière d'air
Les convoyeurs à glissière d'air transportent des matériaux secs et poudreux à l'aide d'une couche d'air le long d'un canal incliné. Ils comportent une surface poreuse qui permet à l'air de circuler, créant ainsi un lit fluidisé. Cette conception réduit les frottements et permet le déplacement en douceur des matériaux sans composants mécaniques. Par conséquent, les convoyeurs à glissière d'air fonctionnent efficacement et sont couramment utilisés dans des industries telles que le ciment et la transformation des aliments pour assurer une manipulation en douceur des matériaux en vrac.
Impact matériel
Le taux d'humidité des matières premières contribue de manière significative aux blocages. Par exemple, l'argile peut avoir un taux d'humidité de 8% à 10%. La cimenterie utilise un broyeur sécheur à balayage d'air à une chambre. Lorsque le flux d'air est trop important, le taux d'humidité du matériau broyé peut dépasser 1%. Les matériaux collants à haute température peuvent obstruer les pores de la couche d'aération, ce qui entraîne un flux d'air irrégulier et provoque des blocages dans le convoyeur à glissière d'air. De plus, pendant les arrêts, les matériaux laissés dans le convoyeur peuvent refroidir et se condenser, ce qui aggrave le blocage. Pour résoudre ces problèmes, l'usine a mis en place les mesures suivantes :
- Contrôle rigoureusement l'humidité des matériaux: La teneur en humidité de l'argile entrante est maintenue en dessous de 6%. La température des gaz provenant du broyeur est contrôlée entre 90 et 100°C, ce qui permet de s'assurer que le taux d'humidité du matériau broyé ne dépasse pas 0,8%.
- Mesures de nettoyage d'urgence: En cas d'arrêts longs et inattendus, les opérateurs doivent ouvrir le couvercle du convoyeur et dégager manuellement le matériel.
Impact de l'usine
Au cours de l'essai initial du moulin à cimentLa grille de décharge était trop large et des problèmes avec le tamis rotatif ont permis à des débris de fer, à de petites billes d'acier et à des matériaux grossiers de se mélanger au ciment broyé. Ces matériaux sont entrés dans le convoyeur à glissière d'air par l'intermédiaire de la grille de décharge. élévateur à godets et s'accumule dans la couche d'aération. Lorsque suffisamment de matière s'accumule, l'air injecté ne peut pas la fluidifier correctement, ce qui entraîne des blocages. Pour lutter contre ce phénomène, l'atelier a pris les mesures suivantes :
- Ajuster l'espacement des grilles d'évacuation du broyeur: Cela garantit une décharge en douceur et empêche les matériaux grossiers et les impuretés de pénétrer dans le convoyeur.
- Mettre en place des points de surveillance: Des dispositifs de surveillance ont été installés à la sortie de l'élévateur à godets et à l'entrée du convoyeur. Des contrôles réguliers permettent d'évacuer les déchets de fer et les matériaux grossiers accumulés.
Impact du convoyeur
(1) Problèmes d'étanchéité
Le corps inférieur du convoyeur n'était pas correctement scellé, ce qui provoquait des fuites d'air. Cela réduisait la différence de pression à travers la couche d'aération, empêchant une bonne fluidification des matériaux et rendant le transport difficile. Dès sa découverte, les mesures suivantes ont été prises :
- Améliorer l'étanchéité: Des pinces supplémentaires ou du ruban d'étanchéité ont été utilisés pour remédier aux fuites d'air.
(2) Dommages à la couche d'aération
Les dommages causés à la couche d'aération peuvent provoquer un court-circuit de l'air, ce qui entraîne des jets d'air qui obstruent le flux de matière. Par conséquent, des blocages se produisent. Pour résoudre ce problème, l'usine a pris des mesures immédiates :
- Inspecte régulièrement la couche d'aération: Tout dommage doit être traité rapidement avec des réparations ou des remplacements.
(3) Problèmes de conception de l'échappement
Le convoyeur supérieur doit maintenir une pression nulle ou légèrement négative. Cependant, la conception de l'usine reliait l'échappement du convoyeur au boîtier de l'élévateur à godets, qui n'était pas relié au système de dépoussiérage. L'échappement et la pression positive dans le convoyeur supérieur étaient donc inadéquats, ce qui rendait difficile la fluidification des matériaux. Pour résoudre ce problème, l'usine a mis en œuvre les solutions suivantes :
- Redessiner les sorties d'échappement: L'échappement du convoyeur a été raccordé à l'équipement approprié pour assurer un flux d'air régulier.
- Contrôler l'entrée d'air: L'ouverture des vannes d'air a été ajustée en fonction des caractéristiques des matériaux pour assurer un débit d'air régulier et réduire les risques de blocage.
(4) Impact des conditions météorologiques
Les convoyeurs à glissière d'air extérieur de l'usine étaient exposés à l'eau de pluie, qui s'infiltrait par les interstices et rendait les matériaux collants, ce qui entraînait des blocages. Pour atténuer ce problème, l'usine a pris les mesures suivantes :
- Installer une protection contre la pluie: Les convoyeurs extérieurs ont été modifiés avec des mesures de protection pour empêcher la pluie de pénétrer et d'affecter les propriétés du matériau.
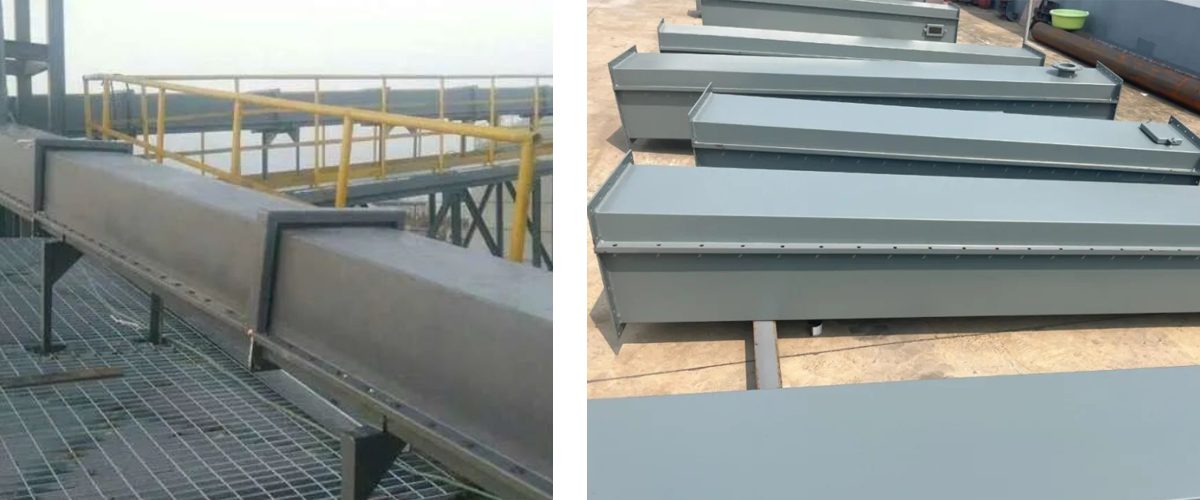
En conclusion, grâce à une analyse approfondie et à des solutions efficaces pour les blocages des convoyeurs à glissière d'air, la cimenterie a amélioré ses procédures d'exploitation et mis en place des mesures préventives. Après plus d'un an et demi de production, le fonctionnement des convoyeurs à glissière d'air s'est stabilisé, assurant une production de ciment sans heurts.
Pour plus d'informations ou une assistance technique, n'hésite pas à nous contacter. Nous sommes impatients de collaborer avec toi pour améliorer l'efficacité et la sécurité de la production de ciment.