Belt conveyors are super important in factories and production lines. They help save time and cut down on labor costs a lot. However, common faults such as belt misalignment, spillage, and fire can seriously impact production efficiency and safety. To protect our valuable production lines, it is essential to understand these faults and take effective preventive measures.
Common Faults
1. Belt Misalignment
Belt misalignment is one of the most common issues. It can arise from several factors. Here are key measures to solve this problem:
Adjust the Carrying Roller Group: If the belt misaligns in the middle, adjust the position of the roller group. The mounting holes are designed as elongated holes for easier adjustment.
Install Self-aligning Roller Groups: These rollers create lateral force to help the belt center itself. This method is suitable for short conveyors or bi-directional operations. However, use it cautiously on long conveyors to avoid affecting belt life.
Adjust Drive and Redirect Rollers: Ensure all conveyor rollers are perpendicular to the centerline of the conveyor. Misalignment will cause the belt to shift. Move the bearing seats according to the direction of misalignment.
Adjust Tensioning Points: Ensure the tensioning roller’s axis is perpendicular to the belt. When using spiral or hydraulic tensioning, make sure the bearing seats move simultaneously.
Check Loading Points: The position where material drops affects belt alignment. Consider the relative height of the upper and lower conveyors to reduce side impacts.
Adjust for Bi-directional Operation: For bi-directional conveyors, adjust each direction separately, focusing on the drive and redirect rollers.
2. Spillage Issues
Spillage is another common problem with belt conveyors. The main causes include:
Spillage at Loading Points: Spillage often occurs at the loading chute or guide trough. Overloading or damaged rubber skirts can cause materials to spill. Keeping up with regular check-ups and maintenance is really important.
Suspended Belt in Troughs: A small radius in the trough can cause the belt to suspend, leading to spillage. Use larger radius curves in design to prevent this.
Spillage from Misalignment: When the belt misaligns, materials can spill from the lower side. Adjust the belt promptly.
3. Accident Analysis
Causes of Fire Accidents
Belt conveyor fires can occur suddenly and develop rapidly, leading to severe consequences. The main causes include:
- Slippage: Loose belts, excessive loads, or insufficient friction can cause slippage and generate enough heat to start a fire.
- Electrical Equipment Failure: Short circuits or equipment explosions can also trigger fires.
Causes of Belt Misalignment Accidents
Belt misalignment can reduce the conveyor’s lifespan and lead to downtime and safety issues. The main causes are:
- Equipment Issues: Problems like cylinder errors or unresponsive rollers can lead to misalignment.
- Improper Installation: Misalignment during installation can cause problems.
- Inadequate Maintenance: Delayed cleaning can lead to dust buildup and misalignment.
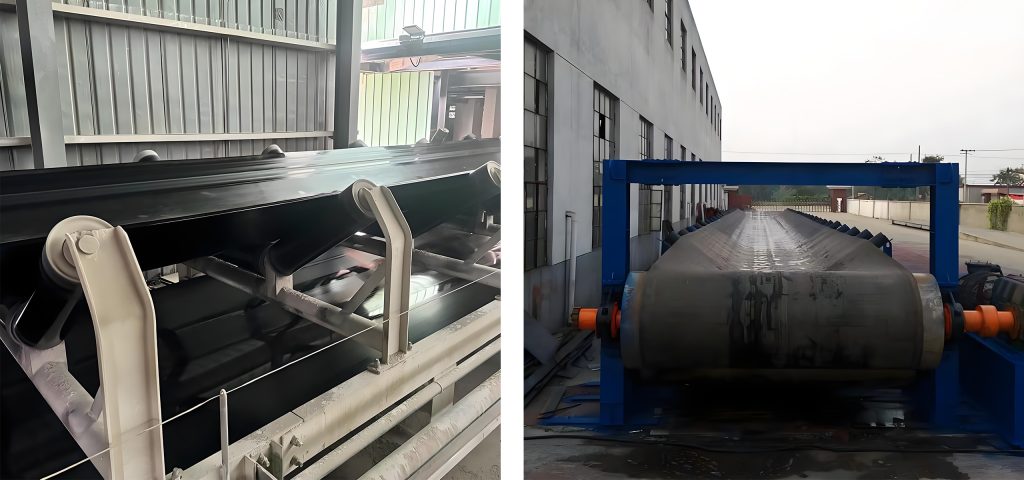
Mesures préventives
1. Fire Prevention
- Use flame-retardant belts to control fire spread.
- Strengthen electrical equipment maintenance to prevent fires.
- Keep the work area clean and check conveyors regularly for debris.
- Install temperature monitoring et smoke alarms to enhance safety.
2. Preventing Misalignment
- Purchase quality equipment to ensure manufacturing precision.
- Follow proper installation guidelines to maintain alignment.
- Regularly clean dust and adjust misalignment as needed.
3. Preventing Tears
- Repair worn chutes promptly to prevent impacts on the belt.
- Address misalignment issues immediately to avoid tearing.
- Install tear monitoring devices to detect and address issues quickly.
As a professional belt conveyor manufacturer, Darko is committed to providing high-performance equipment that has undergone rigorous testing. Our products ensure efficient and stable operations, providing strong support for your production line. We can meet the most demanding application needs with durable, wear-resistant, and high-temperature belts.If you have any questions about our products or services, please feel free to nous contacter.
If you follow these steps, you can really cut down on problems and safety issues with belt conveyors. Together, we can ensure production safety and enhance operational efficiency!