Une entreprise exploite six silos de stockage de ciment. Ces silos ont une structure cylindrique en acier et en béton. Chaque silo a des dimensions de 18 x 45 m et peut contenir jusqu'à 10 000 tonnes de différents types de ciment en fonction de la demande du marché. Le système de broyage du ciment utilise un mode de broyage combiné "presse à rouleaux + broyeur à boulets". L'entreprise propose des options d'expédition en sac et en vrac.
Aperçu des problèmes de prise en masse du ciment
Lors de l'expédition et du déblaiement du ciment, la société a constaté des niveaux variables de colmatage des parois et de colmatage du ciment dans les silos. Dans certains cas, le colmatage des parois dépassait 0,5 mètre. Lorsque les silos se déchargent, le ciment tombe souvent en gros morceaux et bloque la sortie de décharge. Ce blocage interrompt le processus d'expédition et doit être éliminé avant la reprise des opérations. Pendant les saisons de pointe, l'agglomération réduit l'efficacité du chargement et affecte la satisfaction des clients quant à la qualité du ciment.
Les passages d'accès étroits créent des risques de chute d'objets, des niveaux élevés de poussière, un manque d'oxygène, des blessures mécaniques et des risques électriques. Certaines cimenteries ont commencé à utiliser des machines pour le déblaiement au lieu de recourir à des méthodes manuelles. Cependant, ce changement peut réellement augmenter leurs coûts d'exploitation.
Pour réduire le mottage des parois et le mottage du ciment pendant la décharge, l'entreprise a analysé les causes et mis en œuvre des mesures ciblées à différentes étapes, notamment le stockage, le transport, les opérations de broyage, la gestion et le contrôle de la décharge. Ces mesures ont donné des résultats positifs.
Analyse des causes de la prise en masse du ciment
Le ciment est un liant hydraulique. Ses caractéristiques d'hydratation sont la principale raison de la formation de mousses lors du stockage. Idéalement, il est préférable que la teneur en humidité du ciment soit plus faible. Cependant, des taux d'humidité élevés résultent souvent d'un excès d'humidité dans les matériaux mélangés et de l'eau introduite lors de la production et du transport. Pour éviter que le ciment ne s'agglomère, il est très important de gérer les niveaux d'humidité lors de la fabrication et du transport, de le stocker correctement et de traiter les parois des silos pour éviter l'agglomération.
Problèmes courants et mesures de production
Le processus de production du ciment comprend plusieurs étapes : stockage des matériaux, dosage et transport, systèmes de broyage, transport des produits, sommet, intérieur et fond des silos, et déchargement. Vous trouverez ci-dessous les problèmes les plus courants et les mesures de production correspondantes pour chaque étape :
1. Problèmes de stockage des matériaux
- Stockage extérieur: Veillez à ce que les matériaux mixtes soient stockés à l'intérieur afin de réduire l'humidité grâce au séchage naturel.
- Défauts de conception: Utilisez une stratégie d'empilage par zone et mettez en œuvre un système "premier entré, premier sorti" pour maintenir la qualité des matériaux.
- Contrôle de la qualité des matières premières: Contrôler strictement la qualité des matériaux entrants afin d'empêcher l'entrée de matériaux de qualité inférieure.
2. Problèmes de transport par lots
- Protection contre la pluie: Assurer l'étanchéité des couloirs de transport et systèmes de dépoussiérage pour éviter les fuites d'eau de pluie.
- Contrôle de l'humidité de l'air: Nettoyez régulièrement les filtres huile-eau et vidangez l'eau des réservoirs d'air.
3. Problèmes liés au système de broyage
- Conception de la soupape d'air froid: Installez des bâches de protection contre la pluie pour éviter les infiltrations d'eau.
- Contrôle de l'humidité: Ajustez le mélange de matériaux en fonction des conditions climatiques saisonnières afin de maintenir l'humidité du ciment fini ≤0,5%.
4. Problèmes de transport des produits finis
- Scellement des goulottes de transport: Veillez à ce que le système de transport soit étanche afin d'éviter toute pénétration d'humidité.
- Vérification du système de dépoussiérage: Inspectez régulièrement l'étanchéité du système de dépoussiérage pour garantir des performances optimales.
5. Problèmes liés au sommet du silo
- Mesures d'imperméabilisation: Contrôler régulièrement et réparer les installations d'étanchéité sur les sommets des silos.
- Contrôle de la pression négative: Maintenez la pression négative du dépoussiéreur au sommet du silo dans une fourchette raisonnable afin d'éviter la formation d'une croûte.
6. Problèmes à l'intérieur du silo
- Gestion du temps de stockage: Réduisez les quantités stockées en hiver pour éviter un stockage prolongé.
- Problèmes d'agglomération: Utiliser de nouveaux matériaux comme les membranes anticorrosion en nano-céramique pour minimiser l'adhérence des murs.
7. Problèmes de fond de silo
- Dysfonctionnements du robinet à boisseau sphérique électrique: Effectuez un entretien régulier pour garantir le bon fonctionnement et éviter les zones mortes.
- Inspection de la goulotte: Remplacez rapidement les bâches endommagées afin d'assurer un transport sans heurts.
8. Problèmes de décharge
- Ajout de disjoncteurs forfaitaires: Installer briseurs de grumeaux sous les vannes de déchargement pour briser le ciment en petits morceaux afin de faciliter le transport.
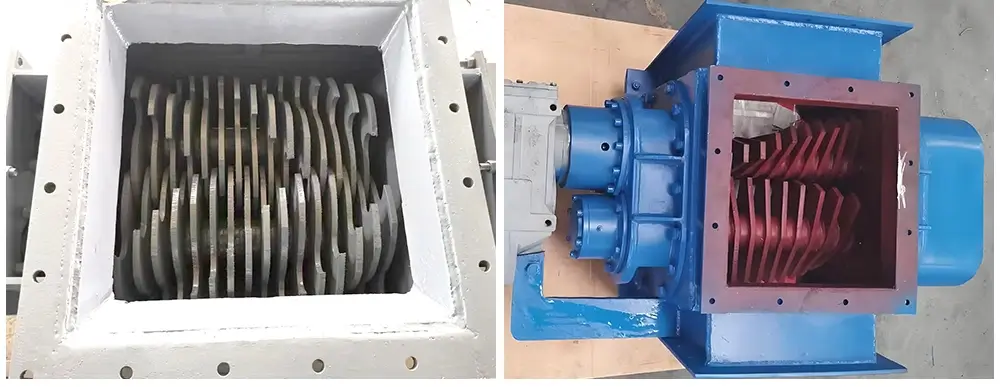
Conclusion
La mise en œuvre de ces mesures ciblées a permis à l'entreprise de réduire considérablement l'agglomération du ciment dans les entrepôts. Elle a fait un excellent travail de gestion de l'humidité dans les différents matériaux, a amélioré la conception de la protection contre la pluie et a utilisé des silos capables de supporter des taux de décharge élevés. Ces efforts ont permis de garantir un déchargement en douceur du ciment. Ces dernières années, la fréquence des incidents liés à la prise en masse a considérablement diminué, ce qui a permis de garantir une production efficace et d'améliorer la compétitivité du marché.
Pour plus d'informations ou de soutien, veuillez nous contacter.
Les Darko se réjouit de pouvoir vous fournir des produits et des services de haute qualité.