Preventing dust explosions requires a multi-faceted approach. Dust explosions happen when dust concentrations reach a certain level, mix with air, and encounter an ignition source. Fine dust particles create a flammable mixture in the air. When ignited, they release a large amount of energy, leading to an explosion. Therefore, controlling dust concentration and cleaning promptly are crucial to preventing explosions.
Here are some key preventive measures:
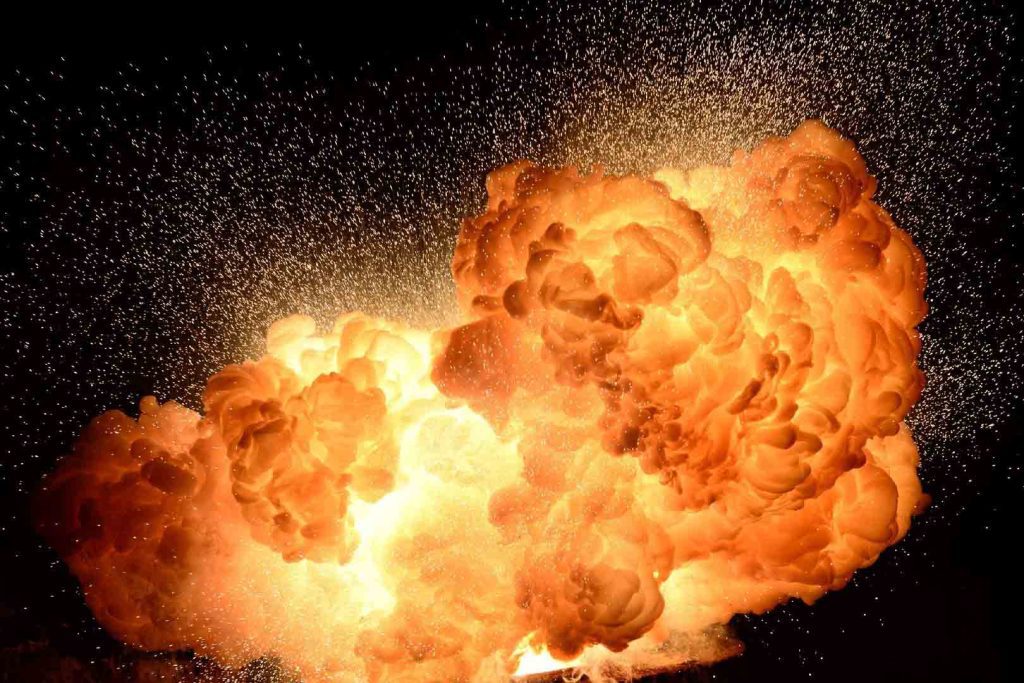
Control Dust Concentration
Ensure Equipment Sealing: Make sure that all equipment, containers, and conveying systems are well-sealed to minimize dust leakage.
Improve Ventilation and Dust Removal: Install effective ventilation and dust removal systems. This will enhance dust extraction and reduce dust levels in the workshop. Darko’s dust collectors provide high filtration efficiency and reliability to help companies manage dust effectively.
Manage Dust Accumulation and Cleaning: Keep the floors, walls, and ceilings of the workshop smooth and free of protrusions to make cleaning easier. Use explosion-proof vacuum cleaners for regular cleaning. Additionally, spray water to dampen dust when possible. Increasing air humidity to over 65% helps dust settle and absorbs heat from dust oxidation, which reduces static electricity risks.
Control Ignition Sources
Choose Equipment Wisely: When maintaining dust-laden equipment, it is essential to use tools that do not create sparks from impact or friction. Additionally, ensure that all electrical equipment meets explosion-proof standards. Furthermore, avoid installing machinery that generates static electricity or sparks, and implement static grounding measures to enhance safety.
Manage Open Flames: Designate areas with combustible dust as no-fire zones. Moreover, control the use of open flames strictly. Before welding in these areas, ensure that all materials are cleared from the equipment. Additionally, take steps to prevent slag from falling into machines or onto materials.
Install Spark Detection and Extinguishing Systems: In suitable workshops, it is important to install spark detection and fire extinguishing systems. Specifically, these systems can detect sparks in dust removal ducts or powder conveying pipes. In addition, they use water mist to extinguish sparks quickly and effectively.
Control Oxygen Content
In some cases, fill the grinder with inert gases like nitrogen or carbon dioxide. This lowers the oxygen content in the system and helps prevent dust explosions.
Implement Additional Measures
Handle Materials Properly: Screen, de-stone, and remove metals from crushed materials to prevent sparks from impurities entering the crusher.
Control Temperature: Ensure that the surface temperature of heating devices and high-temperature pipes does not exceed the ignition temperature of the dust cloud.
Conduct Regular Inspections and Maintenance: Regularly check electrical equipment to prevent aging or short circuits that can create ignition sources.
Provide Personnel Training: Strengthen safety education for staff. Increase their awareness of dust explosion hazards and teach them basic emergency response skills.
Develop an Emergency Plan
Create an emergency plan for dust explosions. This plan should include steps for emergency evacuation, initial fire-fighting, and personnel rescue. It ensures a timely and effective response in the event of a dust explosion.
By implementing these measures, companies can significantly lower the risk of dust explosions while protecting their personnel and property. At Darko, we are committed to providing efficient dust management solutions. Our products help companies effectively control dust and maintain safe operations. If your company has any questions about dust collection systems, please don’t hesitate to reach out to us.