の中で セメント 産業界の効率的な運営 クリンカーバルクローダー,集塵機と関連設備が重要である。S社は、毎時450トンの生産能力を持つセメントクリンカ製造ラインを運営しており、4つのバルクローディングシステムを備えている。オペレーターは、タービン減速機を動力源とするホイストを使って排出管を制御し、さまざまな高さの車両に対応している。しかし、実際の操業中、この設備は生産効率や環境衛生に影響を与えるいくつかの問題に直面しました。
特定された問題点
について クリンカーバルクローディング 排出システムは、伸縮式メインパイプ4セクションと伸縮式集塵パイプ4セクションで構成されています。積み込みの際、伸縮する継ぎ手やフックの位置により、排出管周辺の隙間から粉塵が逃げ、装置周辺に粉塵が堆積する。この問題は風の強い時に悪化する。さらに、3ヶ月使用すると、伸縮パイプの壁がひどく摩耗する。オペレーターは、パイプのミスアライメントやフックの摩耗といった問題に頻繁に遭遇する。これらの問題は、メンテナンスを複雑にし、ダウンタイムを増加させ、クリンカ装入効率に大きな影響を与え、メンテナンスコストと労働強度を上昇させる。
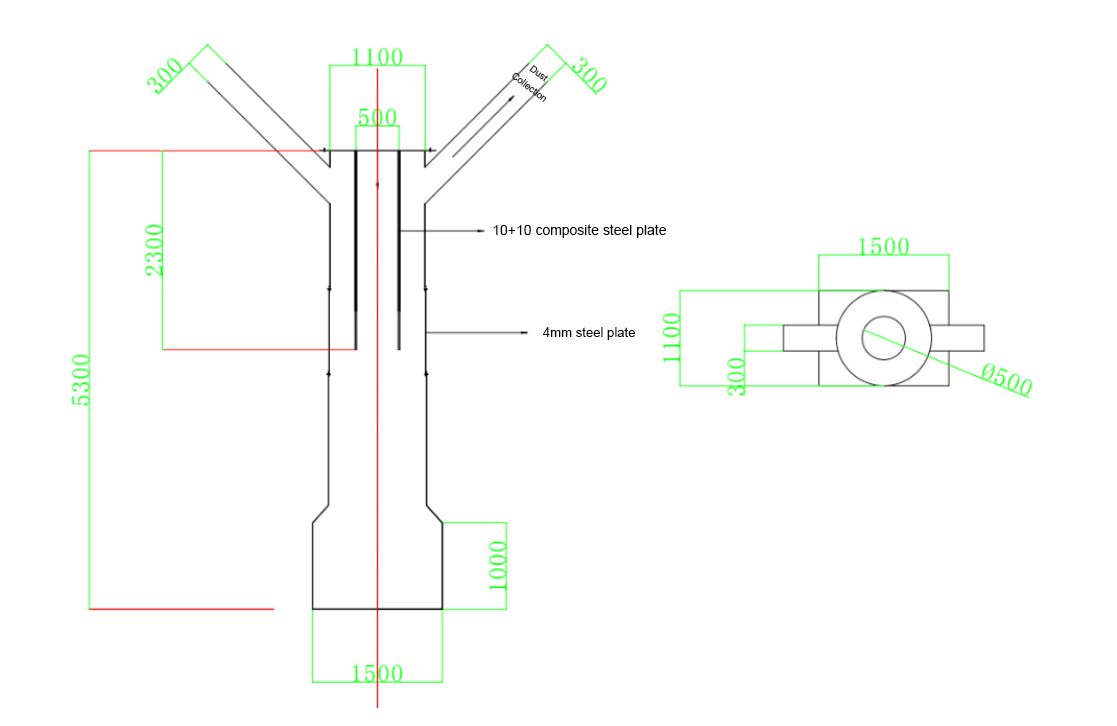
是正措置
これらの問題に対処するため、ダーコの技術チームは徹底的な分析を行い、一連の是正措置を提案した:
1) 放電装置の再設計
密閉性を向上させ、粉塵排出を削減するため、技術チームはクリンカ排出装置を再設計した。新しい設計では、複合鋼板製の耐摩耗性パイプが採用された。集塵アウトレットは排出パイプ上部の両側に配置されています。この内部ローディングと内部エアフロー設計により、粉塵排出が効果的に削減される。
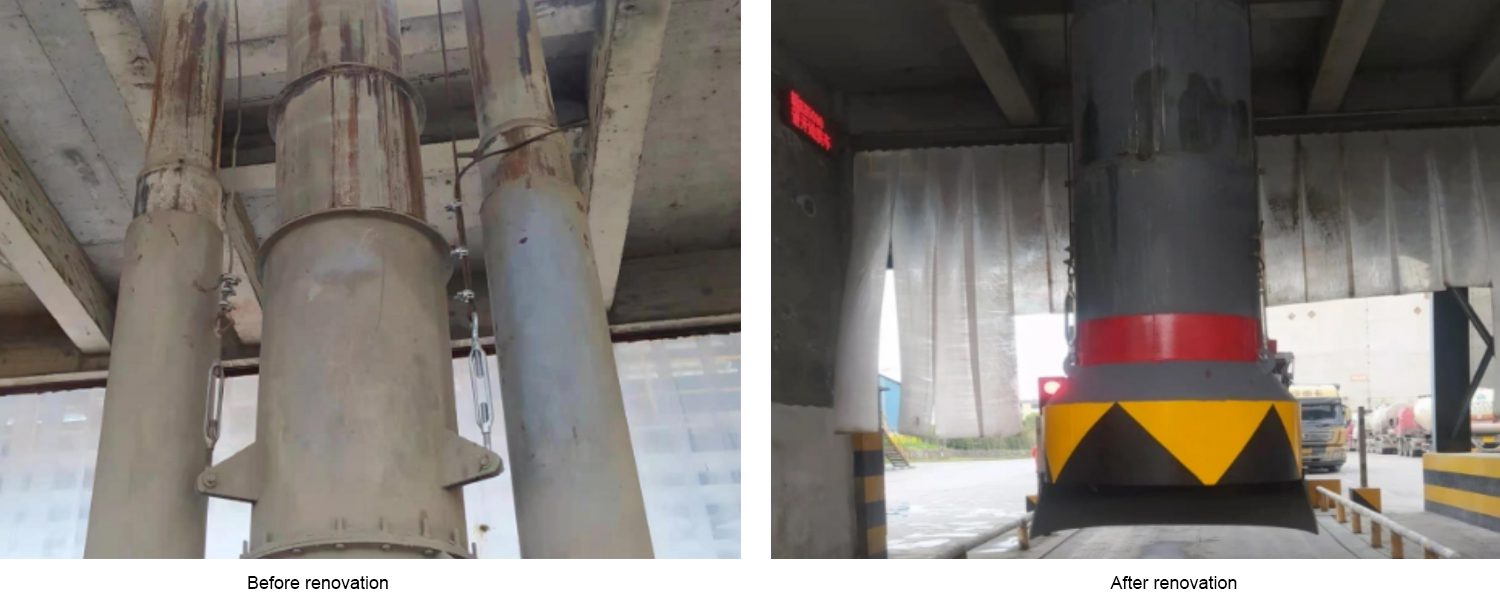
2) シーリング性能の向上
空気漏れと粉塵のオーバーフローという以前の問題に対処するため、技術チームはメインパイプをスチールケーブルで接続し、柔軟な構造を作り上げた。設置時には、伸縮式パイプフードの負圧を最大にするため、部品間にシーリングガスケットを追加した。これにより、外部の空気が集塵システムに入るのを防ぎ、集塵効率を高めることができる。
3) 定期的なメンテナンスと点検
集塵機が扱う粉塵濃度が高く、処理量が多いこと、特に雨天時にはクリンカ粉塵が塊を形成する傾向があることから、技術チームは定期的な検査計画を策定した。これにより、集塵システムが正常に作動するようになります。定期的な点検は、潜在的な問題を迅速に特定・解決し、継続的かつ効率的な設備稼働を保証するのに役立つ。
改造後の結果
改造後、クリンカ・バルクローダは内部ローディング・集塵システムに変わり、フードの詰まりによる粉塵排出がなくなった。2021年10月以降、パイプのずれの問題は再発しておらず、長年の粉塵オーバーフローの問題が効果的に解決された。さらに、この改造により従業員の労働環境が大幅に改善され、会社の経済的利益と全体的な環境条件が向上した。