について パルスジェットバッグフィルター は、99%を超える粉塵除去効率を誇る高効率集塵装置です。微粒子を効果的に捕集し、排出ガス中の粉塵濃度を10mg/m³以下に抑え、クリーンな空気を確保します。
The bag dust collector is very adaptable. It can handle airflow rates from tens of thousands to hundreds of thousands of cubic meters per hour. This pulse jet dust collector is widely used in high-pollution industries. For example, it is essential in スチール, セメント化学物質 パワー を生成する。さらに、セメント製造、カーボンブラック製造、飼料加工などの工程では、材料回収器としても機能する。
構造と動作原理
The pulse bag dust collector consists of several key components:
- Cleaning System
- Sealed Dust Collection Chamber
- Main Frame
- Dust Hopper
- Operational Electrical Control System
Function of the Dust Filter Bags
During operation, dust-laden gas flows through the dust collector filter bags. The gaps between the filter fibers trap particles larger than the gap diameter. Dust adheres to the filter surface in this process, known as screening.
Initially, new フィルターバッグ have larger fiber gaps, resulting in poor dust collection efficiency. Over time, a thick layer of dust accumulates on the filter surface, enhancing the screening effect. After the dust collection process, some residual dust remains on the surface and inside the filter bags. This allows the filter to maintain good dust collection efficiency. Materials like needle-punched felt or plush filter cloth form a dense, porous layer. This optimizes the screening effect and does not rely solely on the dust layer.
Dust Collection Process
The cleaning of the filter bags is achieved using compressed air. The cleaning system consists of an air storage tank, a blowing pipe, and an electromagnetic pulse control valve. Each row of filter bags has a blowing pipe equipped with a nozzle aimed at the center of the filter bag. Each blowing pipe has a pulse valve connected to the compressed air tank.
During the cleaning process, the electromagnetic valve opens the pulse valve, allowing compressed air to flow through the nozzle into the filter bag. The air, along with surrounding gas, enters the filter bag, causing it to vibrate and creating a reverse airflow from inside to outside, effectively removing dust from the outer surface of the filter bag.
The pulse jet cleaning method generates the most dust removal energy. It is a typical external cleaning method that has strong cleaning capability and minimizes residual dust in the filter bag fibers. Filter bags are usually made from felt or needle-punched fabrics. The pulse jet action causes noticeable deformation of the filter bags, generating significant stress. Therefore, the filter material must have high tensile strength. Additionally, frequent friction between the filter bags and their support frame requires durable materials, such as wear-resistant or woven filter bags.
洗浄方法の種類
Bag filters can be classified into three categories based on their cleaning methods:
Mechanical Vibration Type
This type has a simple structure and reliable operation, but its cleaning efficiency is low and it can easily damage filter bags. Therefore, this cleaning method is used less frequently.Reverse Jet Type
This type can be further divided into chamber reverse jet and nozzle reverse jet.- Chamber Reverse Jet: This design uses a chamber structure to introduce clean air from the atmosphere or dust collection system into different bag chambers for cleaning. However, its cleaning efficiency is low, and the investment cost is high.
- Nozzle Reverse Jet: This type uses a high-pressure fan or compressor to provide reverse airflow for cleaning through a moving nozzle. Although it has strong cleaning capability, it is complex and costly, with a high risk of damaging the filter bags.
Pulse Jet Type
This type can be classified based on the pressure of the injected air into low pressure (below 0.25 MPa), medium pressure (0.25 MPa to 0.5 MPa), and high pressure (above 0.5 MPa). It can also be divided into rotary pulse jet and inline pulse jet types.- Rotary Pulse Jet: This type uses a modular structure and can perform online or offline cleaning. It has fewer pulse valves and operates reliably, but its complexity requires strict installation and maintenance.
- Inline Pulse Jet: Also known as tube jet pulse dust collectors, the blowing pipes are fixed within the collector's upper shell. Each pulse valve’s blowing pipe typically has multiple nozzles aimed at the filter bags below, allowing for efficient pulse jet cleaning. Its advantages include a simple structure, fewer moving parts, low failure rates, and reliable operation. It can flexibly design the distribution of filter bags according to process requirements, resulting in low operating costs. It also ensures sufficient cleaning pressure at the bottom of the filter bags using compressed air. Overall costs are low, and chamber-type bag dust collectors can achieve online maintenance. However, this type requires more pulse valves.
効率に影響を与える要因
Several factors influence the efficiency of pulse bag filters:
- ダストの特徴: The size and density of particles affect filtering performance.
- Quality of Filtering Material: The quality of the material directly impacts overall performance.
- Airflow Velocity: Proper settings can significantly improve capture rates.
- Design: Well-planned inlet and outlet layouts help avoid inefficiencies.
- Cleaning Method: Effective cleaning is crucial for maintaining filter bag performance.
メンテナンスの重要性
Regular inspections are essential for achieving optimal operation of pulse bag dust collectors. Maintaining the dust collection chamber, tightening screws to prevent leaks, and regularly replacing worn seals all contribute to extending the lifespan of the equipment.
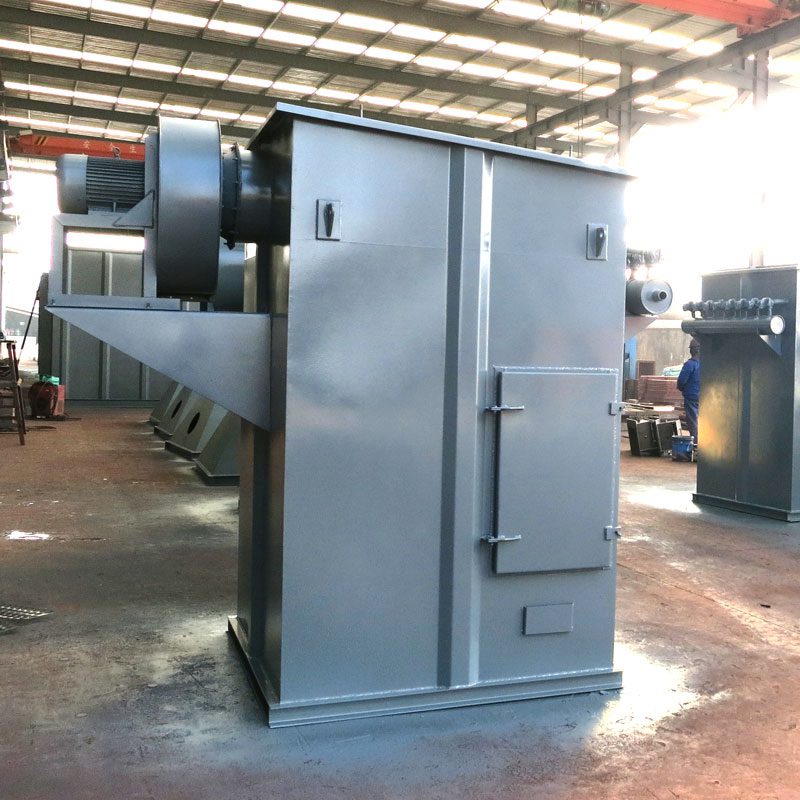
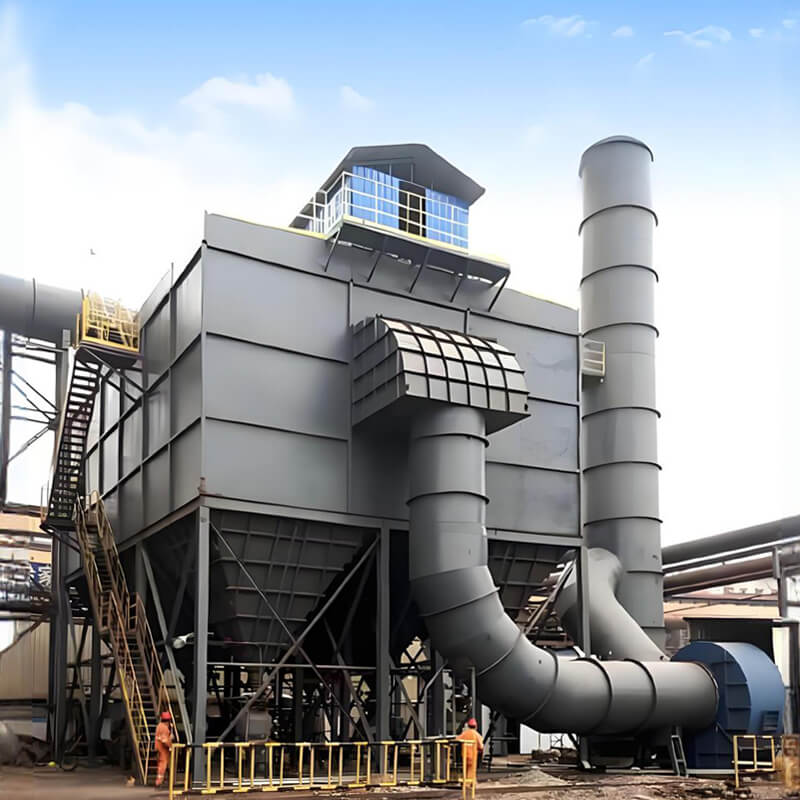
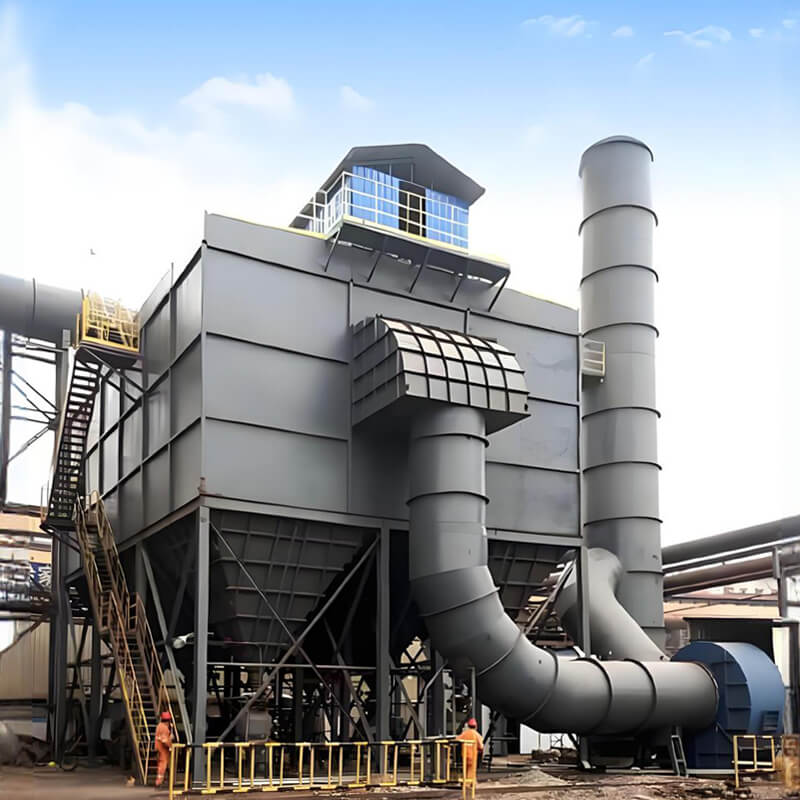
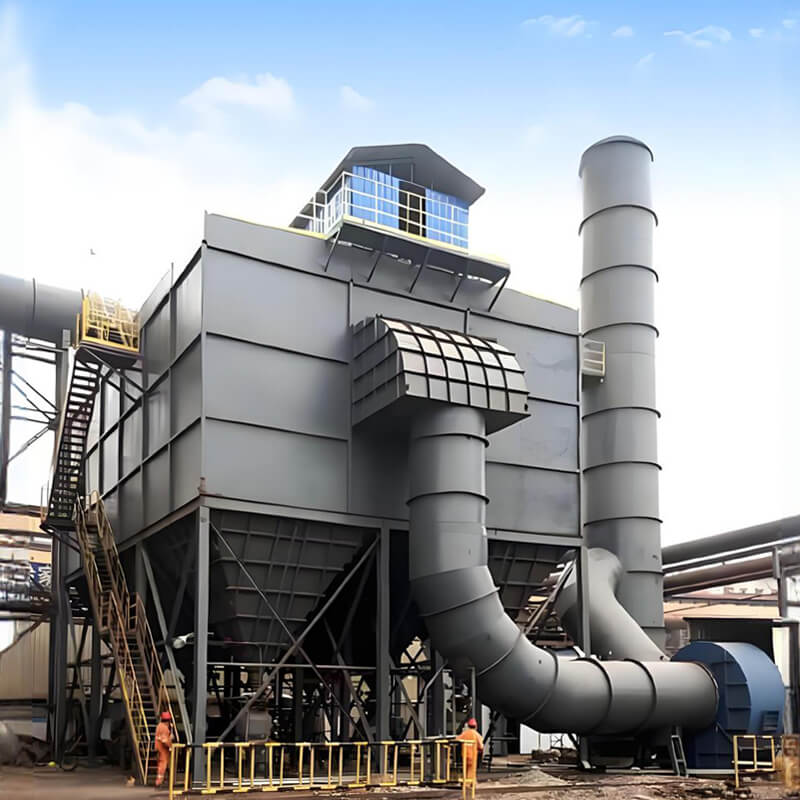
ダーコを選ぶ理由
で ダーコ当社は、高品質のセメント機械設備の製造に専念しています。先進的なパルスジェットバッグフィルターなど、環境に優しいソリューションの提供に注力しています。当社の製品ラインは以下の通りです。 セメントサイロ, バルクローディングシステムそして バルブこれらはすべて、お客様の業務効率と持続可能性を高めるために設計されています。
結論
パルスジェットバッグフィルターは、産業環境において必要不可欠です。きれいな空気を確保し、公衆衛生を守り、製品の品質を向上させます。適切な集塵装置を選択することで、クリーンな生産と持続可能な発展に大きく貢献します。パルスジェットバッグフィルターに関するご質問や、弊社製品に関するお問い合わせは、お気軽に下記までご連絡ください。 お問い合わせ!