現代の産業において、立形粉砕システムの効率は生産コストとエネルギー消費に直接影響します。ここでは、消費電力を削減し、システム抵抗を最小限に抑え、日々のオペレーションを最適化するための効果的な戦略をいくつかご紹介します。
1.メインモーターの電流を減らす
マテリアルハンドリングに機械式リフティングを使用し、エアリフティングよりも効果的に消費電力を下げる。この方法によって バーチカルミル竪型粉砕機の大半は、外部循環エレベーターを備えている。現在、ほとんどの竪型ミルは外部循環エレベーターを備えています。しかし、外部循環とシステム出力の最適なバランスを、生産中の継続的な調査を通じて見つける必要があります。
理論的には、材料層が低いほど、高い層よりもモーター電流が大幅に低下する。したがって、材料層の厚さをコントロールすることが非常に重要です。ダムリングを使ってこの厚さを調整します。ダムリングの高さを最適化することで、ミル内の材料層をより適切な厚さにすることができます。層厚を薄くすることで、単位体積の材料における有効な力が増加し、油圧シリンダーの作動圧力が下がり、ミル内の圧力差が小さくなるため、メインモーター電流が小さくなります。
機器の選定や工程設計の際には、適切な外部循環の比率とノズルリングの適切な風速を考慮する。外部循環エレベーターの容量がシステム要件に適合していることを確認してください。さらに、吐出時の過度の微粉を防ぐためには、空気量のコントロールが不可欠です。
2.システム抵抗の低下
循環ファンが消費するエネルギーは、風圧、風量、ファンの効率と密接な関係がある。システム抵抗が高い場合、ファン効率は低下し、消費電流の増加につながる。したがって、システム抵抗を減らすことは、ファンの効率を高め、消費電流を下げるために不可欠である。
熱風入口、分級機出口、サイクロン出口、ノズルリング出口の主要箇所に圧力検出装置を設置し、主な抵抗源を特定する。これらの場所の圧力差を比較することで、主な抵抗源を突き止めることができます。
3.システムの空気漏れに対処する
竪型ミルシステムのエア漏れは、主にミルと集塵機で発生します。リーク率が8%以下であることを確認してください。主なリーク源は、ミル入口のロックエア装置、ローラシール、接続フランジ、および エキスパンションジョイント.集塵機では、ケーシングカバーと接続フランジで重大な漏れが発生することがよくあります。
エア漏れはファンによる電流消費を増加させ、エネルギーコストを上昇させ、工場の生産高に影響を与える可能性がある。したがって、エア漏れを適時に管理することは、システムの効率を向上させるために不可欠である。
4.日常業務の洞察
通常ローラー直径の3%から5%の範囲内で、投入原料の粒度をコントロールします。ローラスリーブと粉砕テーブルライナーに摩耗が発生したら、ローラと粉砕テーブルの間のギャップを調整します。アキュムレータの圧力を定期的にチェックし、ローラの使用圧力の 60% から 70% 以内に維持します。
粉砕圧力を高くすることは必ずしも有益ではありません。出力が臨界値に達した場合、モーター電流がさらに増加するとエネルギー消費が悪化し、安全運転が危ぶまれます。したがって、実際の生産条件に基づいて最適な圧力を決定してください。さらに、粉砕と分級効率を安定させるために、出口ガス温度を85℃前後に維持してください。
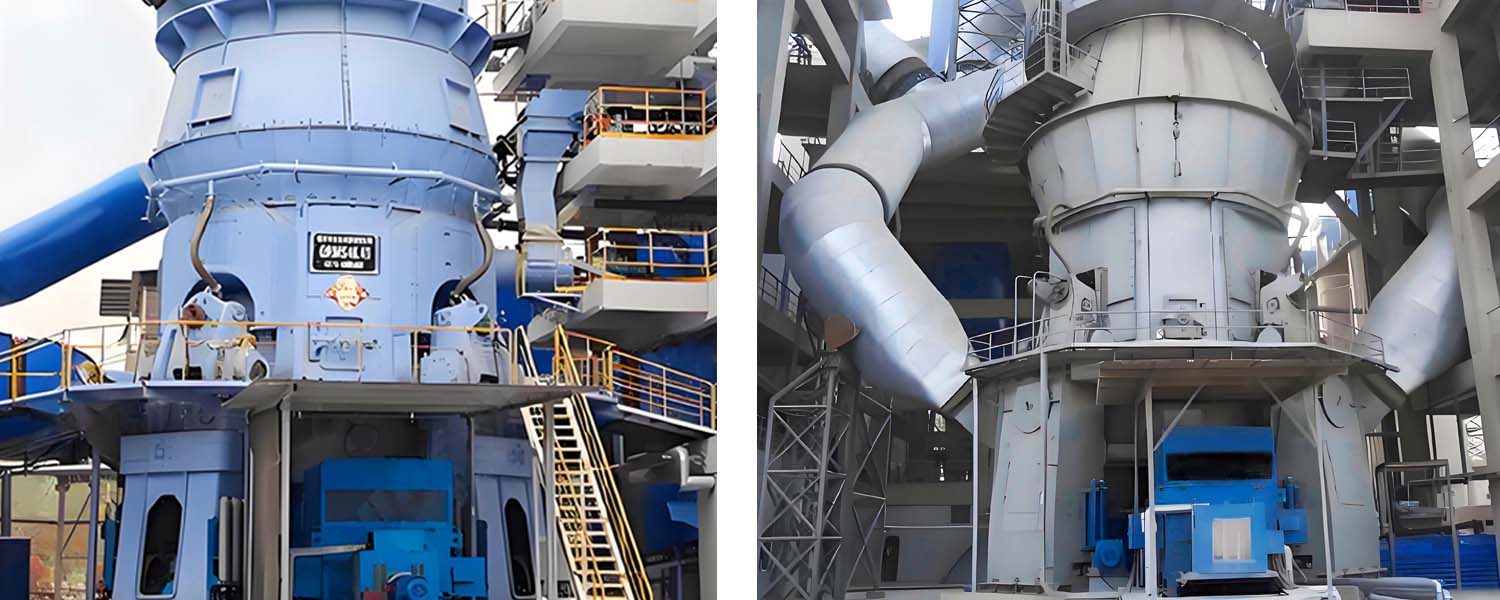
5.中央制御操作の考慮点
研削圧力: 粉砕圧力はある限界値を超えないようにしてください。それ以上上げると、メインモーターの電流とエネルギー消費量が上昇する可能性があります。この点を最適化するために、圧力と出力を相関させた曲線を作成する。
出口ガス温度 出口ガス温度は85℃前後で安定させてください。逸脱は粉砕・分級効率に大きな影響を与えます。
バルブ設定: インレットエアバルブ、循環エアバルブ、ファンアウトレットバルブ、バイパスエアバルブを含むすべてのバルブを開き、システム抵抗を最小にします。バイパスバルブが開いたままでよいかを確認するには、バイパ スバルブを閉じてインレット負圧を観察します。上昇する場合は、バイパスバルブを再び開きます。
負圧制御: 集塵機最後尾の負圧を-500Pa以内に維持する。この圧力は、工場に流入する補助空気量に影響し、排気ファンの電流を減少させる。負圧が下がらない場合は、現場を監視し、粉塵が逃げる場所に対処しながら、徐々に最後尾の排出量を下げるよう中央制御装置に指示してください。
スタートアップとシャットダウンの時間を制御する: 最初の補助装置の始動からミルへの供給までの時間が4分を超えないようにしてください。シャットダウン中、メンテナンスが必要ない場合は、粉砕機から原料を空にする必要はありません。
これらの戦略を実行することで、企業はエネルギー消費を抑え、生産工程を最適化しながら、竪型粉砕システムの効率を大幅に向上させることができます。縦型粉砕システムの効率向上に関するご質問やサポートが必要な場合は、下記までお気軽にお問い合わせください。 お問い合わせ.私たちはプロフェッショナルなソリューションを提供します!