原料用竪型粉砕機は、竪型粉砕機における主要な粉砕機器である。 セメント 生産に直結する。操業の安定性は、生産効率と製品品質に直接影響する。しかし、多くの企業では、竪型ミルシステムの空気漏れの問題に直面することが多い。これはエネルギー消費を増加させるだけでなく、設備の故障につながる可能性もあり、生産ラインの継続性と信頼性に影響を与える。本稿では、原料の空気漏れの原因について分析する。 垂直ミル そして、それに対応する解決策を提案する。
I.竪型ミルにおけるエア漏れの影響
1.エネルギー消費の増加: 竪型ミルシステムの空気漏れは熱損失を引き起こす。ミルの内部温度は低下する。必要な温度を維持するためには、追加の熱風供給が必要となり、エネルギー消費量の増加につながる。
2.アウトプットの減少: 空気が漏れると、原料の一部が失われる。粉砕機内の原料が減少すると負荷が下がり、生産量が低下する。
3.機器の故障: 長時間の空気漏れは、内部部品、特にシールやパイプの摩耗を加速させる。これは機器の寿命を縮め、メンテナンスコストを増加させる。
4.製品の品質低下: 空気漏れは原料の粉砕効率に影響し、製品が細かくなりすぎたり粗くなったりする。
II.竪型ミルにおける空気漏れの原因
1.シールの老朽化または損傷: ローラーシールやフィーダーシールなどのシールは、長期間の運転で老朽化したり破損したりして、空気漏れを引き起こすことがある。
2.パイプ接続の緩み: 竪型ミルと集塵機の間の換気パイプの取り付けが緩かったり、接続が不適切な場合、空気漏れが発生することがあります。
3.ロック式フィーダーの不合理な設計: ブレード付き分割ホイールのような従来のロック式フィーダーは、隙間が大きすぎたり小さすぎたりすると、エア漏れを起こすことがある。
4.非効率的なローラーシール構造: 現在のローラーシールのデザインは単純で、シール効果が低い。特に下部のシールではスペースが限られているため、効果的なシールを確保するのが難しい。
5.スラグ排出設計の欠陥: スラグ排出口からベルトコンベアへの直接シュートは、主要な漏出ポイントである。当初の設計で使用されていたシングル・フラップ・バルブは、大きな材料によって簡単に詰まってしまい、ミルが停止してしまう。
III.竪型ミルにおける空気漏れの解決策
1.老朽化したシールを交換する: 効果的なシーリングを確保するため、老朽化または損傷したシールを定期的に点検し、交換する。
2.パイプの接続を強化する: 換気パイプの接続が確実かつ堅固であることを確認するため、換気パイプを徹底的に点検し、緩んでいる接続部があれば補強する。
3.ロッキングフィーダー設計の最適化: ミルヘッドでマテリアルシールを実施する。空気漏れにつながる間隔の過不足を避けるため、分割ホイールの隙間を調整する。
4.ローラーシール構造の改善: ローラーシールを円形のシリコンウェーブシールに変更する。このデザインは、より優れた弾力性とシール効果を提供し、効果的に空気漏れを減らします。
5.スラグ排出口の再設計: 排出ポートを無動力フラップロックバルブに変更する。この設計では、バルブ本体と材料カーテンを組み合わせ、システムの負圧を利用して密閉構造を作り、空気漏れの問題に効果的に対処する。
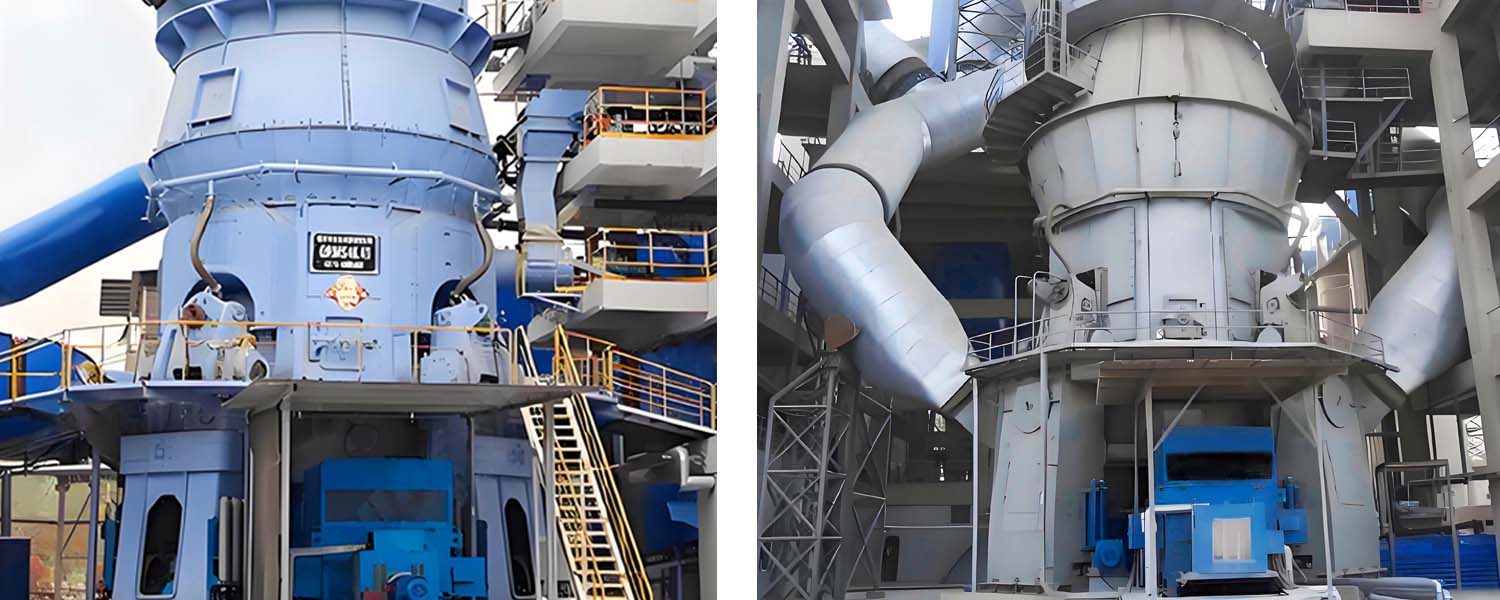
IV.ケーススタディ
4500 t/dのクリンカ生産ラインを持つセメント企 業において、原料システムはTRM53.4原料竪型ミルを装備 している。深刻な空気漏れのため、キルンテー ルの酸素含有量は10.3%に達し、原料プロセスの電 力消費量は16.5kWh/tであった。循環ファンの電気消費量は8.6 kWh/tと高く、出力温度は45~55℃と低かった。
このため、原料工場の省エネルギーニーズは著しく制限されていた。空気漏れに対処し、ファンの効率を改善した後、この企業はロッキングフィーダーの交換、ローラーシールの改良、排出口の再設計などの対策を実施した。
その結果、空気漏れは大幅に減少し、電気消費量は3.8kWh/t減少し、出力温度は上昇し、時間当たりの生産量は向上した。これらのアップグレードの後、この企業は年間約258万元のエネルギーコストを節約し、大きな経済的利益を達成した。