The LS screw conveyor is widely used for material transport. The name “LS” stands for “screw” and “horizontal” transport. This equipment comes in various diameters, including 100, 160, 200, 250, 315, 400, 500, 630, 800, 1000, and 1250 mm. The maximum length of a single unit can reach 35 meters (30 meters for LS1000 and LS1250). It operates effectively in temperatures ranging from -20℃ to 50℃ and can transport materials at angles less than 20° and temperatures not exceeding 200℃.
Advantages
- Simple Structure: The design is compact, and the cross-section is small, leading to lower manufacturing costs.
- High Flexibility: It allows for intermediate loading and unloading at multiple locations.
- Safe Operation: The design ensures ease of use and safety.
- Good Sealing: The cover design effectively isolates materials from the outside, preventing leaks.
Disadvantages
- High Power Consumption: Moving materials requires overcoming friction between materials and the casing or screw.
- Material Crushing: The screw action may crush materials during transport.
- Severe Wear: The screw and casing wear out easily over time.
Due to these pros and cons, the LS screw conveyor suits various powdery, granular, and small block materials, such as coal powder, flour, cement, sand, grains, briquettes, and stones. However, it is not suitable for perishable, sticky, or easily clumping materials since they may stick to the screw and cause operational issues.
Additionally, the effective flow cross-section is small, making it unsuitable for large block materials. To ensure normal operation, maintain a uniform feed to avoid material blockages and overloads.
Installation Requirements
The installation of the screw conveyor must meet the following technical conditions to ensure proper operation:
- Foundation Requirements: Complete the foundation at least 20 days before installation for stability.
- Parts Inventory: Check all components before installation to ensure nothing is missing and clean them.
- Symmetrical Installation: Align the casing and end frames symmetrically in the vertical plane.
- Horizontal Alignment: Keep the centerline of the casing consistent in the horizontal plane.
- Smooth Connections: Ensure there are no significant height differences at the joint surfaces of adjacent casings.
- Stable Base: Secure the base after installation and tighten the corner bolts.
- Bearing Support: Ensure the intermediate suspension bearing supports the connecting shaft properly to avoid bending or suspension.
- Tight Connections: Tighten all connection screws to a reliable degree.
- Lubrication Check: Check the oil level after installation to ensure it is sufficient.
- No-Load Testing: Conduct at least 4 hours of no-load testing after installation to observe smooth operation and check for leaks, overheating, or looseness.
Address any issues immediately to ensure proper function.
Operation and Maintenance
The LS screw conveyor transports powdery and small block materials. It often operates in harsh environments, making proper operation and maintenance essential:
- Uniform Feeding: Ensure consistent feeding to prevent material blockage and overload.
Start Without Material: Start the machine when empty, then add materials. - Stopping Conditions: Only stop the machine after all materials are transported.
- Avoid Large Blocks: Prevent hard, large materials from entering to avoid damaging the screw.
- Regular Inspections: Check the operational status regularly and ensure all fasteners are secure.
- Connection Checks: Pay special attention to bolts connecting the screw pipe flange and the shaft; address any issues promptly.
- Safe Operation: Do not remove the cover during operation for safety.
- Regular Lubrication: Ensure all moving parts receive regular lubrication.
Daily Maintenance
- Perform maintenance at the start of each shift, taking about 10 minutes.
- After 720 hours of operation, conduct a primary maintenance check, taking 4 hours.
- After 2400 hours of operation, conduct a secondary maintenance check, taking 16 hours.
Use lubricants with the same properties as substitutes. Regularly clean the equipment to ensure the cleanliness of the drive mechanism and other components.
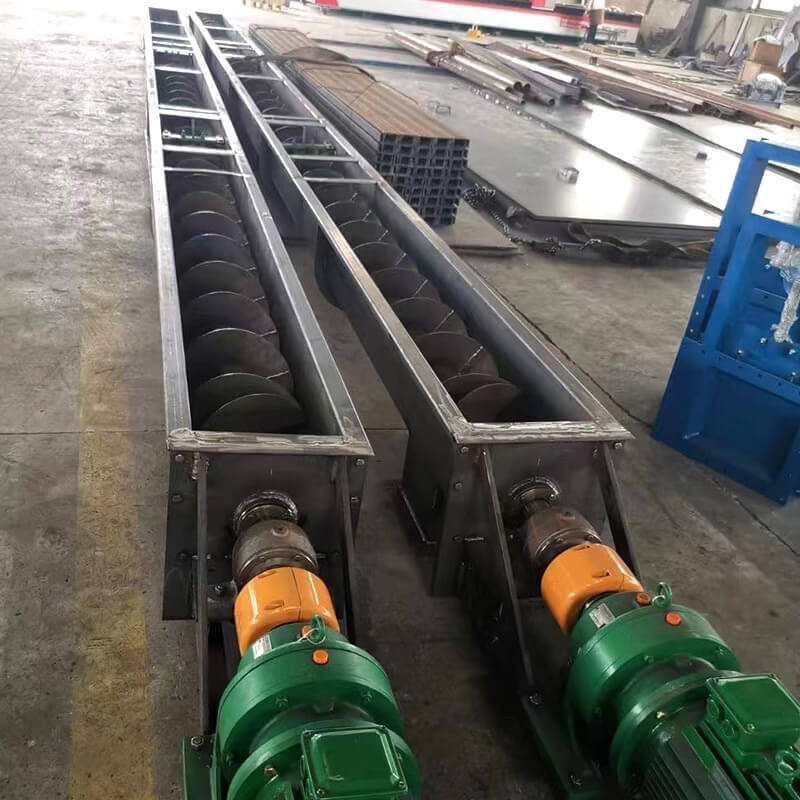
Conclusion
The LS screw conveyor is an efficient material handling device. With proper installation, operation, and maintenance, it can maximize performance and ensure long-term stable operation. For more information or inquiries, please contact us. We are ready to provide you with professional support and services.