O desalinhamento da correia é um problema comum e desafiador na operação de transportadores de correia. A causa principal do desalinhamento reside nas forças externas líquidas que actuam sobre a correia no sentido da largura, que não é zero, ou na tensão de tração desigual perpendicular à largura da correia. Este desequilíbrio faz com que a força de reação dos rolos ou dos tambores exerça uma força lateral sobre a correia, conduzindo ao desalinhamento. Este artigo analisa as causas do desalinhamento da correia e fornece medidas corretivas eficazes.
Causas do desalinhamento da correia
1. Desalinhamento dos centros
As estruturas da cabeça, da cauda e do meio podem não estar corretamente alinhadas. Este desalinhamento ocorre frequentemente devido a uma instalação incorrecta, fazendo com que a linha central longitudinal da correia não seja perpendicular ao eixo do tambor, afectando o funcionamento.
2. Posição incorrecta do rolo
Todos os rolos devem ser instalados perpendicularmente à linha central da correia e paralelamente ao plano horizontal. Se este requisito não for cumprido, a correia deslocar-se-á para um dos lados.
3. Junta incorrecta da correia
Quer utilize juntas mecânicas ou vulcanizadas, quaisquer irregularidades na junta podem levar a uma tensão desigual em ambos os lados, causando um desalinhamento durante o funcionamento.
4. Estrutura do rolo desalinhada
A linha central do grupo de rolos deve estar alinhada com a linha central da estrutura da máquina. O erro admissível não é superior a 3,0 mm. Se a estrutura do rolo estiver incorretamente instalada ou se os parafusos estiverem soltos, a correia pode ficar desalinhada.
5. Danos na correia
Se o grau de dano for inconsistente em ambos os lados da correia, pode causar um estiramento desigual e resultar em desalinhamento.
6. Ponto de descarga incorreto
Uma descarga irregular de material pode levar a uma distribuição desigual da força na correia, provocando o seu desalinhamento. Se o ponto de descarga estiver descentrado, deve ser imediatamente ajustado.
7. Impacto da queda de material
Quando o material cai sobre a correia, o seu peso e inércia podem fazer com que a correia se desloque.
8. Material acumulado
Os materiais pegajosos podem acumular-se nos rolos ou tambores, provocando uma tensão desigual e causando um desalinhamento.
9. Ângulo incorreto do rolo
Se o ângulo de instalação do rolo não for exato, pode fazer com que a correia se desloque na secção de transporte.
10. Questões relacionadas com a qualidade das correias
Se a densidade da correia for irregular, isso pode levar a uma tensão irregular e resultar em desalinhamento.
11. Problemas com o dispositivo de tensionamento
A instalação ou o ajuste incorreto do dispositivo de tensionamento pode levar a uma tensão desigual e causar desalinhamento.
12. Envelhecimento devido à utilização a longo prazo
Com o tempo, as correias podem soltar-se, aumentando o risco de desalinhamento.
13. Inclinação do quadro
Se a estrutura estiver inclinada, pode exercer uma força lateral sobre a correia.
14. Vibração do equipamento
Vibrações fortes durante o funcionamento, especialmente o movimento radial dos rolos, podem causar o desalinhamento da correia.
15. Raio de curvatura pequeno
Se o raio de curvatura de uma secção côncava for demasiado pequeno, a correia pode levantar durante o arranque.
Medidas corretivas para o desalinhamento da correia
Para resolver as causas acima referidas, podem ser aplicadas as seguintes medidas:
Alinhe os quadros da cabeça, da cauda e do meio: Certifique-se de que os três componentes estão alinhados na mesma linha central.
Posição correta do rolo: Certifique-se de que o eixo do rolo é perpendicular à correia e paralelo ao plano horizontal.
Ajuste as articulações da correia: Remova todas as juntas mal alinhadas e certifique-se de que estão direitas.
Realinhe as armações dos rolos: Desloque o quadro do rolo no lado desalinhado e recalibre-o conforme necessário.
Melhorar a manutenção: Inspeccione regularmente a correia e repare ou substitua imediatamente quaisquer secções danificadas.
Ajuste o ponto de descarga: Certifique-se de que o ponto de descarga está centrado no tapete.
Conceba guias de materiais adequados: Evite a queda direta de objectos de grandes dimensões e instale rolos amortecedores no ponto de descarga.
Limpar material acumulado: Mantenha as superfícies do rolo e do tambor limpas e mantenha o funcionamento dos dispositivos de limpeza.
Ajuste a posição do grupo de rolos: Modifique os orifícios de instalação com base na direção do desalinhamento.
Escolha fabricantes de renome: Assegurar um equipamento de qualidade e um bom serviço pós-venda.
Instale corretamente os dispositivos de tensionamento: Certifique-se de que a linha central é perpendicular ao eixo do rolo e siga os requisitos de instalação.
Realizar inspecções regulares: Substitua imediatamente as correias envelhecidas ou deformadas.
Inclinação correta do quadro: Volte a instalar o quadro para garantir que está nivelado.
Identifique e resolva os problemas de vibração: Resolva as fontes de vibração do equipamento.
Adicione rolos de pressão: Instale rolos de pressão nas secções côncavas para evitar que a correia se levante.
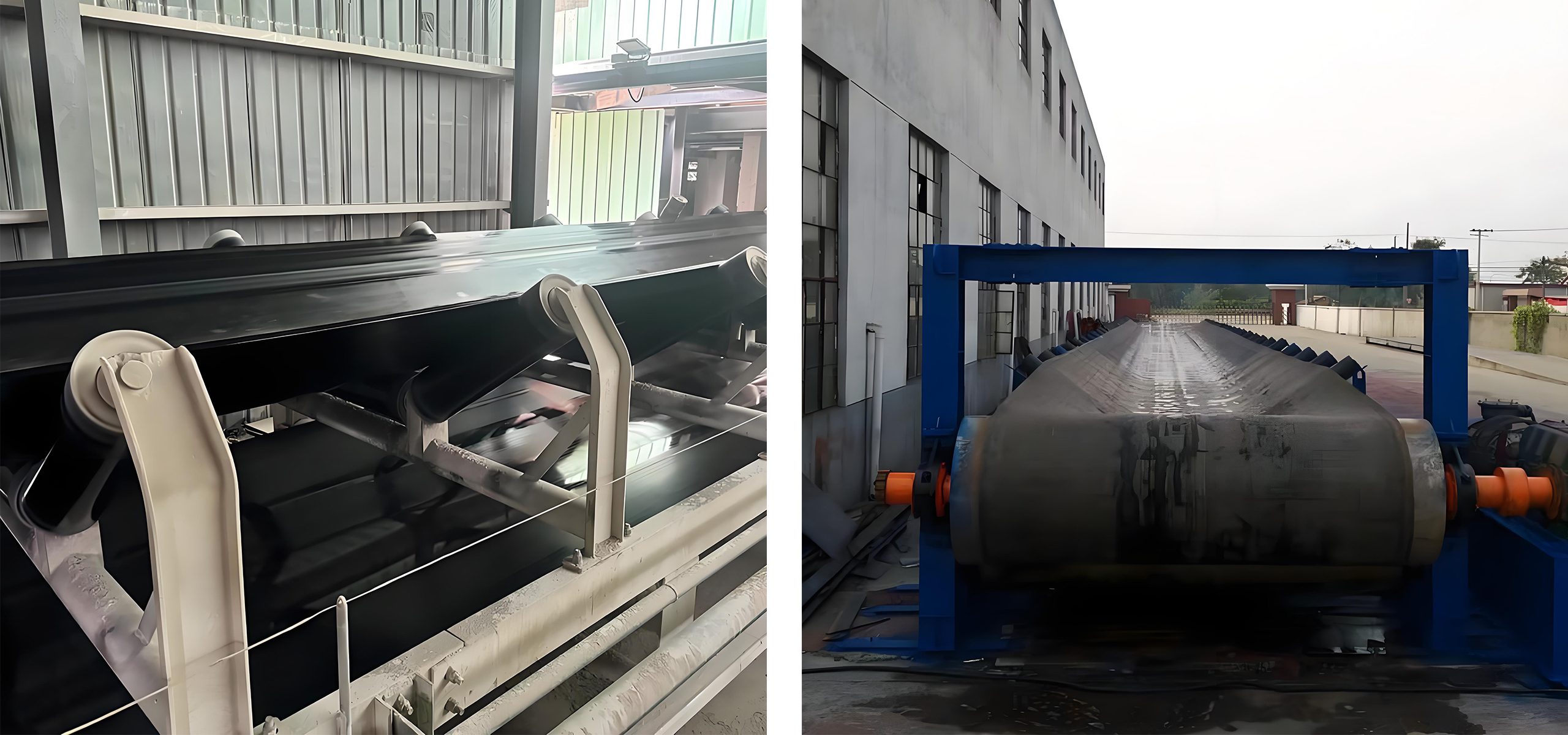
No funcionamento dos transportadores de correia, é essencial monitorizar de perto o desalinhamento da correia. A identificação atempada das causas e a implementação de medidas adequadas são fundamentais para manter um funcionamento eficiente e estável. Ao seguir estas acções corretivas, pode reduzir eficazmente os riscos associados ao desalinhamento e aumentar a eficiência da produção. Para mais informações ou assistência, não hesite em contactar contactar-nos! Estamos aqui para o ajudar e apoiar.