A elevada eficiência e o baixo consumo de energia do processo de moagem de cimento sempre foram os objectivos das empresas de produção. "Melhorar a capacidade do moinho" é um tema constante. Esforçamo-nos continuamente para melhorar a eficiência de moagem de moinhos de bolas. O nosso objetivo é reduzir o consumo de energia de moagem e os custos de produção, ao mesmo tempo que obtemos a máxima finura e rendimento.
Com a implementação de novas normas de cimento, existem agora maiores exigências relativamente à finura do cimento, à área de superfície específica e à composição das partículas. As empresas de cimento tentam frequentemente aumentar a resistência reduzindo a quantidade de materiais misturados ou aumentando a área de superfície específica do cimento. No entanto, a forma mais simples de obter uma área de superfície específica mais elevada é reduzir a produção do moinho e aumentar o tempo de moagem. Isto leva a uma "sobre-moagem", que aumenta a quantidade de micro-finos com menos de 3 micrómetros. A composição das partículas torna-se então pobre. Embora a resistência não melhore muito, o consumo de energia de moagem aumenta significativamente.
Este método de reduzir a produção e aumentar o tempo de moagem para melhorar a finura do cimento ou aumentar o teor de clínquer irá inevitavelmente aumentar os custos de produção. Por conseguinte, devemos concentrar-nos nas modificações internas do moinho, nos materiais de pré-britagem e na otimização da classificação dos meios de moagem para melhorar o teor de partículas de 3-30 micrómetros e aumentar a resistência do cimento.
Formas gerais de melhorar a capacidade do moinho de cimento
1. Reduzir o tamanho das partículas dos materiais recebidos
A redução do tamanho das partículas dos materiais recebidos (clínquer) pode diminuir o consumo de energia por unidade de produto e melhorar a capacidade de moagem do cimento. A dimensão das partículas do material recebido é um fator importante que afecta o rendimento do moinho. As partículas mais pequenas diminuem o diâmetro médio das esferas de aço. Com a mesma carga, o número de esferas de aço aumenta, assim como a área total da superfície. Isto aumenta a área de contacto entre as esferas de aço e o material, melhorando assim a eficiência da moagem. Assim, a adoção de uma abordagem "triturar mais, moer menos" através da pré-trituração pode reduzir o consumo de energia e aumentar a capacidade do moinho.
2. Ajusta a estrutura interna do moinho
Implementámos um processo de pré-trituração, que reduziu o tamanho das partículas dos materiais recebidos. No entanto, a capacidade de moagem não melhorou. Observámos um elevado consumo de energia e carga no classificador O-Sepa, com uma taxa de carga cíclica que atingiu 240% e uma eficiência de classificação de apenas cerca de 25%. Uma análise granulométrica confirmou este facto, mostrando uma curva acentuada na primeira câmara e uma curva quase horizontal na segunda câmara.
Claramente, a força de impacto na primeira câmara é demasiado forte, enquanto a capacidade de trituração na segunda câmara é insuficiente. Para resolver este problema, adicionámos 3 toneladas de pequenas esferas de aço à segunda câmara. Este ajuste aumentou a produção para aproximadamente 70 toneladas por hora. Para melhorar ainda mais, reduzimos o comprimento da primeira câmara de 5,35 metros para 4,85 metros. Deslocámos a placa divisória para a frente e aumentámos o comprimento da segunda câmara de 7,25 metros para 7,75 metros para aumentar a capacidade da câmara de moagem fina e melhorar a eficiência. A primeira câmara utiliza revestimentos curvos escalonados para aumentar a queda do meio de moagem e melhorar a capacidade de impacto. A segunda câmara utiliza um revestimento de dupla curvatura para as funções de classificação e elevação, atingindo uma produção de 80 toneladas por hora, melhorando a eficiência e reduzindo o consumo de energia.
3. Reforça a secagem do material
Precisamos de melhorar a secagem do material para manter o teor de humidade dos materiais recebidos entre 1-2%. O excesso de humidade durante o funcionamento pode provocar o esmagamento, afectando negativamente a capacidade do moinho.
4. Melhora a ventilação interna
Uma boa ventilação interna tem um impacto significativo na qualidade e no rendimento do produto. Uma ventilação eficaz permite a remoção atempada do pó fino para evitar a moagem excessiva. Também transporta o calor gerado durante a moagem, baixando a temperatura interna e reduzindo a possibilidade de desidratação e bloqueios do gesso. Uma boa ventilação reduz as camadas tampão dentro do moinho e acelera as taxas de fluxo, aumentando a produção do moinho. No entanto, a ventilação excessiva pode aumentar as partículas de pó, afectando negativamente a finura do cimento. Quando a ventilação excede um determinado nível, pode aumentar o consumo de energia por unidade. A prática mostra que existe um volume de ventilação ideal entre a produção máxima do moinho e o consumo mínimo de energia.
Normalmente, a velocidade do vento interno dos moinhos de circuito fechado é de 0,8-1,0 m/s, enquanto os moinhos de circuito aberto exigem velocidades de vento mais elevadas devido às temperaturas mais altas. Se o moinho de bolas tiver problemas de ventilação, podemos melhorá-lo abrindo portas de ventilação na entrada de alimentação e moldando a calha de descarga em degraus. Também podemos alargar o orifício central da placa divisória e da grelha de descarga, melhorando o bloqueio do ar na porta de descarga. Estas medidas resolvem o bloqueio de material e aumentam a área de ventilação.
5. Determina razoavelmente a finura pretendida dos produtos de cimento
Na produção atual, se o objetivo de finura dos produtos de cimento for demasiado elevado, pode anular os efeitos de outras medidas. Esta restrição limita a produção do moinho e dificulta os esforços para reduzir o consumo de energia. Por conseguinte, é essencial determinar o objetivo de finura dos produtos de cimento com base nas condições reais.
6. Optimiza o carregamento das esferas de aço
Aumentar o número de esferas de aço no moinho aumenta a área de contacto entre as esferas de aço e o material, levando a um maior rendimento do moinho. A redução do diâmetro das esferas de aço aumenta a área de superfície por unidade de volume, o que também aumenta a produção do moinho. No entanto, o consumo de energia tende a aumentar com a quantidade de esferas de aço carregadas. Geralmente, dentro de um determinado intervalo, o consumo de energia é proporcional à quantidade de esferas de aço e inversamente proporcional ao seu diâmetro. No entanto, a carga excessiva aumenta as colisões e a eficiência de moagem, levando a um maior consumo de energia. O moinho deve ter uma carga óptima de bolas de aço que minimize o consumo de energia, o que deve ser determinado através de ensaios de rácios de carga e diâmetros de bolas óptimos.
7. O papel dos auxiliares de moagem
A adição de uma pequena quantidade de auxiliar de moagem durante o processo de moagem pode eliminar a aderência e a aglomeração de pós finos. Isto acelera o processo de moagem, melhorando a eficiência e a qualidade, ao mesmo tempo que reduz o consumo unitário de energia. A utilização de auxiliares de moagem pode produzir produtos com áreas de superfície específicas mais elevadas e reduzir os casos de moagem excessiva. Além disso, a taxa de fluxo de materiais dentro do moinho aumenta, encurtando o tempo de residência e afetando a finura do produto. Na moagem em circuito aberto, temos de ajustar as condições internas para satisfazer os requisitos de finura do produto. Na moagem em circuito fechado, devemos manter a finura de saída dentro das faixas normais, evitando qualquer aumento gradual no resíduo da peneira. Caso contrário, isto pode reduzir o rendimento do moinho e aumentar a taxa de carga cíclica, levando à sobrecarga do elevador e a bloqueios, podendo causar paragens de produção. Em resumo, a seleção e utilização de auxiliares de moagem é uma tarefa científica rigorosa. Devemos considerar cuidadosamente os cinco pontos seguintes:
Considera as propriedades dos materiais recebidos e realiza testes comparativos em pequena escala. A eficácia dos auxiliares de moagem varia de acordo com o material, por isso, para obter os melhores resultados, devemos primeiro realizar testes em pequena escala sob condições técnicas específicas e, em seguida, implementar as melhores soluções em maior escala.
Presta atenção às condições de moagem e seleciona diferentes tipos de auxiliares de moagem. Os adjuvantes de moagem estão disponíveis nas formas gasosa, sólida e líquida, com vários tipos. A sua adaptabilidade e eficácia variam, e os requisitos diferem entre circuitos abertos e fechados, exigindo testes cuidadosos.
Assegura-te de que a utilização de adjuvantes de moagem não afecta negativamente os processos subsequentes. Ao utilizar auxiliares de moagem em moinhos de cimento, considera o seu impacto na embalagem, nos processos de manuseamento a granel, na construção e na qualidade dos produtos de cimento.
Concentra-te na origem e no custo dos auxiliares de moagem. Os benefícios económicos dos auxiliares de moagem estão intimamente relacionados com o seu preço e oferta no mercado. As empresas devem avaliar e calcular estes factores antes de fazerem as melhores escolhas.
Certifica-te de que os auxiliares de moagem cumprem as normas de proteção ambiental. Muitos aditivos são formulados utilizando subprodutos de fábricas de produtos químicos, contendo frequentemente substâncias nocivas. Ao selecionar os adjuvantes de moagem, não te deixes enganar pelos preços baixos; certifica-te de que os adjuvantes não poluem o ambiente nem prejudicam a saúde dos trabalhadores. Na prática, os auxiliares de moagem funcionam melhor em grandes moinhos de cimento. Dado o seu custo mais elevado, os benefícios da redução do consumo de energia e do aumento da produção devem ser ponderados em relação a esses custos para determinar a sua utilização.
8. Otimização da estrutura e dos parâmetros técnicos do classificador
As principais tecnologias do classificador incluem "dispersão", "classificação" e "recolha". Dispersão significa que o material que entra no classificador deve ser espalhado o mais possível, criando espaço entre as partículas. Assim, a conceção da placa de dispersão, a sua velocidade, o espaço de dispersão, o teor de humidade dos materiais e o caudal afectam diretamente a taxa de dispersão. A classificação refere-se à utilização do fluxo de ar para separar as partículas grossas e finas durante o seu tempo limitado no classificador. Factores como o caudal de gás, a velocidade do ar, os padrões de fluxo de ar, os pontos de interação gás-sólido e a configuração do próprio classificador influenciam significativamente a eficiência da classificação. A recolha refere-se à capacidade do classificador para capturar pós grossos e finos, o que depende do método de recolha e da conceção dos componentes de recolha.
Em 1979, a empresa japonesa Onoda desenvolveu o classificador O-Sepa. Este classificador mantém as vantagens dos classificadores de ciclone, mas utiliza um rotor de gaiola com um princípio de classificação de fluxo de ar em espiral plana, melhorando significativamente a eficiência da classificação. Representado pelo classificador tipo gaiola, este é conhecido como um classificador de alta eficiência e é considerado a terceira geração de classificadores após os classificadores centrífugos e ciclónicos.
A sua eficiência de classificação é geralmente superior à do 80%. No entanto, não inclui um dispositivo de recolha de pó fino e requer filtros de mangas maiores ou colectores de pó eléctricos, o que aumenta o investimento em equipamento e complica a disposição dos processos, limitando a sua adoção generalizada. O classificador O-Sepa, juntamente com colectores de pó de saco de alta eficiência e moinhos de bolas, reduz as cargas cíclicas de 200%-300% em sistemas centrífugos para 100%-200%. Na moagem de cimento, pode atingir mais de 65% de distribuição de partículas na gama de 3-30 micrómetros, resultando numa elevada eficiência de classificação, baixo consumo de energia, elevado rendimento e distribuição razoável de partículas.
9. Aumenta adequadamente a velocidade do moinho
O aumento da velocidade é particularmente eficaz para os moinhos mais pequenos. Estes moinhos têm forças de impacto mais fracas devido aos seus diâmetros mais pequenos. Aumentar a velocidade aumenta a capacidade de trituração do moinho:
- Aumenta o número de impactos em cada meio de moagem dentro do moinho.
- Aumenta o atrito e a ação de trituração entre os meios de trituração e entre os meios de trituração e o revestimento.
10. Baixa a temperatura do clínquer recebido
Reforçar a gestão dos materiais. Devem ser efectuados ajustamentos com base na temperatura do clínquer na área de armazenamento. Os operadores devem seguir rigorosamente os regulamentos e ser avaliados em conformidade. Utiliza termómetros para monitorizar as temperaturas e evitar que o clínquer a alta temperatura entre na fábrica.
Implementa a pulverização de água no refrigerador. A água deve ser pulverizada no meio do arrefecedor usando tubos galvanizados com pequenos orifícios para controlar o fluxo de água entre 500-600 kg/h. Isto pode reduzir a temperatura do cimento de saída em aproximadamente 10℃.
Embora estas medidas de pulverização reduzam efetivamente as temperaturas, têm efeitos secundários. O vapor de água pode transportar pó de clínquer para dentro do triturador na extremidade do refrigerador, formando aglomerados nas paredes internas, o que pode eventualmente perturbar o funcionamento normal do triturador. Por isso, monitoriza regularmente as temperaturas do clínquer e ajusta a pulverização de água em conformidade. Limpa periodicamente o triturador de clínquer.
11. Caraterísticas e capacidade de trituração dos materiais recebidos
Os tipos e as proporções dos materiais recebidos afectam diretamente a produção do moinho, a qualidade e o consumo específico de energia. Quaisquer materiais misturados utilizados no cimento reduzirão geralmente a resistência, mas o grau de redução varia com base na atividade dos materiais. Entre os materiais misturados normalmente utilizados, a escória tem a atividade mais elevada.
No entanto, se a área de superfície específica da escória for inferior a 300 m²/kg, as suas vantagens em termos de resistência do cimento não se manifestam. A capacidade de moagem dos materiais tem um impacto significativo no rendimento do moinho e na qualidade do produto. As normas nacionais definem os coeficientes de moabilidade com base na energia específica necessária para a moagem. Uma vez que a maioria das empresas não dispõe de equipamento de ensaio especializado, os ensaios de moagem em pequena escala, comparando os materiais com areia padrão, podem ajudar a determinar os parâmetros do processo de moagem. Depois de medir os coeficientes de moabilidade das matérias-primas e dos combustíveis, podemos ajustar a carga e a classificação dos meios de moagem com base em métodos científicos.
O coeficiente de trituração está fortemente correlacionado com a estrutura do material. Mesmo dentro do mesmo material, os coeficientes de trituração podem diferir. Por exemplo, o calcário denso e bem cristalizado tem um coeficiente de moabilidade baixo e é mais difícil de moer. A moabilidade do clínquer depende da composição dos seus minerais e do ambiente de arrefecimento. As evidências mostram que valores elevados de KH e P, um elevado teor de C3S, um baixo teor de C4AF e um arrefecimento rápido produzem uma textura mais frágil e coeficientes de moabilidade mais elevados. Por outro lado, valores baixos de KH e P, teores elevados de C2S e C4AF e um arrefecimento lento conduzem a clínqueres mais densos e resistentes, com coeficientes de moabilidade mais baixos, tornando-os mais difíceis de moer.
Os coeficientes de moabilidade das escórias podem variar significativamente. As escórias que sofrem um arrefecimento rápido depois de serem produzidas são frequentemente porosas e finas, dando origem a um coeficiente de moabilidade mais elevado, de cerca de 1,2-1,3. Em contraste, a escória que arrefece significativamente antes de ser rapidamente extinta forma partículas cristalinas mais densas e pesadas, resultando num coeficiente de moabilidade mais baixo, de cerca de 0,7-0,9, o que torna a sua moagem mais difícil.
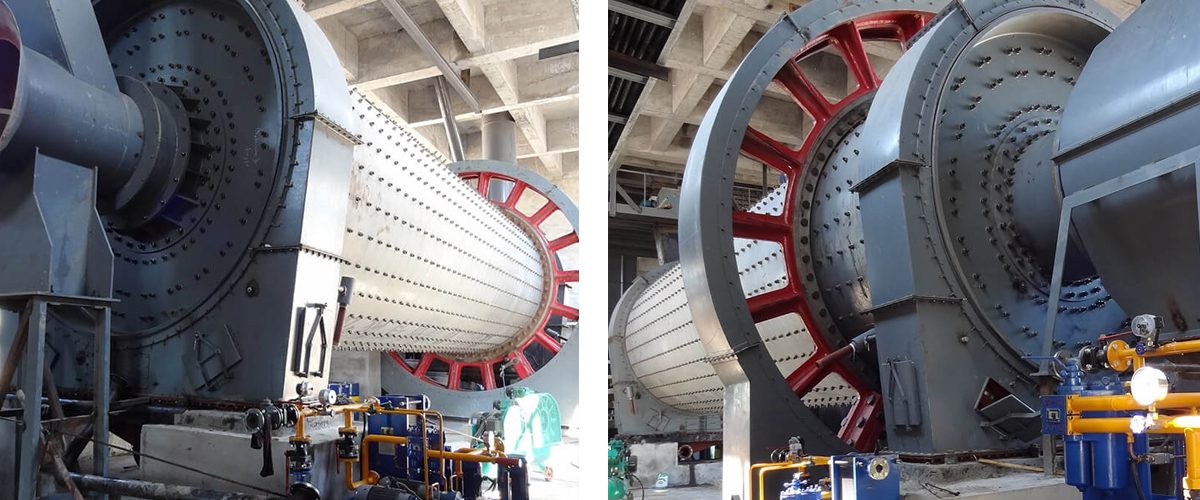
Outras formas de melhorar a capacidade do moinho de cimento
1. Base para um ajustamento razoável dos corpos moentes
O ajuste razoável dos meios de moagem depende das propriedades físicas e químicas dos materiais moídos, do método de moagem e da finura necessária do produto. A análise de resíduos de peneira é um meio eficaz para avaliar se a classificação dos meios de moagem é razoável.
A base para o ajuste dos meios de moagem inclui:
- Quando a dimensão das partículas dos materiais recebidos é fixa, as esferas de aço mais pequenas têm uma área de superfície total maior do que as esferas de aço maiores, aumentando as suas oportunidades de contacto com os materiais. Por outro lado, as esferas de aço maiores fornecem maior energia e capacidade de esmagamento por impacto. Para materiais com tamanhos médios de partículas maiores e maior dureza, devem ser utilizados diâmetros médios de esferas maiores; para materiais mais macios, são adequados diâmetros menores. Para moinhos de menor diâmetro, são utilizados diâmetros médios de esferas menores.
- Se a capacidade de trituração dos materiais recebidos for boa, podem ser selecionadas pequenas esferas de aço; se a capacidade de trituração for fraca, são necessárias esferas de aço maiores.
- A seleção do diâmetro da esfera também está relacionada com a quantidade de material que passa através do moinho por unidade de volume. Na moagem em circuito fechado, o retorno de partículas grossas aumenta o rendimento por unidade de volume, permitindo algum amortecimento das bolas de aço durante o impacto. Portanto, bolas de aço maiores são preferidas em cenários de alto retorno, enquanto bolas menores são selecionadas em outros casos.
- Se o requisito de finura de saída for fino, devem ser utilizadas pequenas esferas de aço; caso contrário, são adequadas esferas maiores.
- Os moinhos de uma câmara utilizam geralmente bolas de aço, enquanto os moinhos de duas câmaras utilizam normalmente bolas de aço na primeira câmara e secções de aço na segunda.
- Os tamanhos dos meios de moagem devem ser bem combinados. As especificações das esferas de aço variam normalmente de 3 a 5 níveis, enquanto as secções de aço variam de 2 a 5 níveis.
- A proporção de esferas de aço de diferentes tamanhos pode seguir o princípio de "pequeno em ambas as extremidades, grande no meio". Quando utilizas dois tipos de secções de aço, cada uma deve ocupar metade.
- Ao mesmo tempo que cumpre os requisitos de tamanho das partículas, o tamanho médio das partículas deve ser minimizado para aumentar a área de contacto e a frequência de impacto, mantendo a relação diâmetro/comprimento das secções de aço reduzida devido ao rápido desgaste radial. A diferença entre o comprimento e o diâmetro das secções de aço deve ser de cerca de 5 mm.
2. Ajusta razoavelmente a taxa de retorno e a classificação dos meios de moagem
Em geral, para reduzir o excesso de moagem, a taxa de enchimento da primeira câmara na moagem em circuito fechado é frequentemente superior à da segunda câmara, o que acelera as taxas de fluxo de material. Uma taxa de retorno de 100-150% produz normalmente a maior produção horária. Se a taxa de retorno for demasiado elevada, embora a finura possa cumprir as normas, a área de superfície específica diminui. À medida que os meios de moagem se desgastam durante a produção, a taxa de enchimento diminui. Inicialmente, isto não é observado como um declínio na produção horária, mas como um aumento nas taxas de retorno, uma redução na área de superfície do cimento e uma queda na resistência à compressão de 3 dias. Quando a taxa de retorno se torna demasiado elevada, leva a uma sobre-saturação, o que provoca uma queda na produção horária. Por conseguinte, é essencial determinar se é necessário suplementar os meios de moagem com base nas taxas de retorno e nas áreas de superfície específicas. Se a produção horária cair significativamente, é necessário limpar o moinho e refazer a classificação dos corpos moedores.
3. Meios de moagem em câmaras de moagem fina
Os meios de moagem são uma das principais medidas para otimizar o moinho. Atualmente, os moinhos de cimento estrangeiros em câmaras de moagem fina tendem a utilizar pequenas esferas de aço em vez de secções de aço, porque as secções de aço consomem cerca de 20-30% mais energia.
As pequenas esferas de aço de alta qualidade desgastam-se menos do que as secções de aço e produzem partículas de cimento mais esféricas, que são superiores às produzidas pelas secções de aço. No entanto, as secções de aço têm as suas vantagens, tais como taxas de fluxo de material mais rápidas e a prevenção da aglomeração de cimento no moinho. Nos últimos anos, tem havido um debate permanente sobre a utilização de perfis de aço ou de esferas de aço nas câmaras de moagem fina. Alguns defendem as secções de aço, enquanto outros preferem as esferas de aço. Esta decisão requer uma análise específica do ponto de vista da moagem. A função de moagem do moinho engloba tanto a trituração como a moagem. A otimização das condições do moinho envolve o equilíbrio dessas duas capacidades para aumentar a eficiência da moagem, garantindo que tanto a produção quanto a finura do produto estejam em níveis aceitáveis. Analisar corretamente a correspondência entre as capacidades de trituração e moagem em diferentes condições é crucial para determinar se devem ser utilizadas secções de aço ou esferas de aço nas câmaras de moagem fina.
- Cada câmara do moinho possui funções de trituração e moagem, embora em graus diferentes. A principal função da câmara de moagem fina é a moagem, e as capacidades de moagem das pequenas esferas e secções de aço são diferentes. A eficiência da trituração depende principalmente da área da superfície de contacto entre os meios de trituração e os materiais. Uma maior área de superfície de contacto proporciona mais oportunidades de moagem, levando a maiores taxas de produção de produto numa unidade de tempo. Com a mesma qualidade, as secções têm uma maior área de superfície de contacto devido à sua natureza de contacto linear em comparação com as bolas. Para câmaras simples, com a mesma carga de corpos moedores e o mesmo material de alimentação, a produção por unidade de tempo numa câmara de secção é superior à de uma câmara de esferas, tal como comprovado pela teoria de moagem e pela aplicação prática. É de salientar que as dimensões actuais dos corpos moentes nas câmaras de trituração fina são geralmente demasiado grandes em comparação com os materiais, em parte devido a restrições na largura dos crivos.
Conclusão
A prática tem demonstrado que as principais vias para alcançar uma moagem de cimento de alta qualidade, eficiente em termos energéticos e de elevado rendimento incluem: "adicionar processos de pré-trituração antes da moagem, efetuar melhorias estruturais no moinho e selecionar classificadores eficientes após a moagem". A pré-trituração é o "pré-requisito", as modificações internas são a "base" e a seleção óptima após a moagem é a "garantia". Para mais informações ou pedidos de informação, por favor contactar-nos!