Высокая эффективность и низкое энергопотребление Процесс измельчения цемента всегда были целями производственных компаний. "Повышение производительности мельниц" - постоянная тема. Мы постоянно стремимся повысить эффективность измельчения шаровые мельницы. Наша цель - снизить расход энергии на измельчение и производственные затраты, добившись при этом максимальной тонкости и производительности.
С введением новых стандартов на цемент теперь предъявляются повышенные требования к тонкости цемента, удельной поверхности и составу частиц. Цементные компании часто пытаются повысить прочность за счет уменьшения количества смешанных материалов или увеличения удельной поверхности цемента. Однако самый простой способ добиться большей удельной поверхности - это снизить производительность мельницы и увеличить время помола. Это приводит к "переизмельчению", что увеличивает количество микрочастиц менее 3 микрометров. После этого состав частиц становится бедным. Хотя прочность улучшается не сильно, расход энергии на помол значительно возрастает.
Такой метод снижения производительности и увеличения времени помола для повышения тонкости цемента или увеличения содержания клинкера неизбежно приведет к росту производственных затрат. Поэтому мы должны сосредоточиться на внутренних модификациях мельницы, материалах для предварительного измельчения и оптимизации сортировки мелющих тел, чтобы улучшить содержание частиц размером 3-30 микрометров и повысить прочность цемента.
Общие способы повышения производительности цементной мельницы
1. Уменьши размер частиц поступающих материалов
Уменьшение размера частиц входящих материалов (клинкера) может снизить расход электроэнергии на единицу продукта и повысить производительность помола цемента. Размер частиц входящего материала - основной фактор, влияющий на производительность мельницы. Более мелкие частицы уменьшают средний диаметр стальных шаров. При одинаковой загрузке количество стальных шаров увеличивается, как и общая площадь их поверхности. Это увеличивает площадь контакта между стальными шарами и материалом, тем самым повышая эффективность измельчения. Таким образом, применение подхода "дробить больше, молоть меньше" за счет предварительного измельчения позволяет снизить энергопотребление и повысить производительность мельницы.
2. Отрегулируй внутреннюю структуру мельницы
Мы внедрили процесс предварительного измельчения, который уменьшил размер частиц поступающих материалов. Однако производительность измельчения не улучшилась. Мы наблюдали высокое энергопотребление и нагрузку на классификатор O-Sepa, при этом циклическая нагрузка достигала 240%, а эффективность классификации составляла всего около 25%. Ситовой анализ подтвердил это, показав крутую кривую в первой камере и почти горизонтальную кривую во второй камере.
Очевидно, что сила удара в первой камере слишком велика, в то время как мощность измельчения во второй камере недостаточна. Чтобы решить эту проблему, мы добавили во вторую камеру 3 тонны мелких стальных шариков. Такая корректировка увеличила производительность примерно до 70 тонн в час. Для дальнейшего улучшения мы сократили длину первой камеры с 5,35 до 4,85 метра. Мы передвинули разделительную плиту вперед и увеличили длину второй камеры с 7,25 до 7,75 метра, чтобы увеличить производительность камеры тонкого помола и повысить эффективность. В первой камере используются изогнутые ступенчатые футеровки, чтобы увеличить падение мелющих тел и повысить ударную способность. Во второй камере используется двойная изогнутая футеровка для функций сортировки и подъема, что позволяет достичь производительности 80 тонн в час, повысить эффективность и снизить энергопотребление.
3. Усильте сушку материала
Нам нужно улучшить сушку материалов, чтобы поддерживать влажность поступающих материалов в пределах 1-2%. Избыток влаги во время работы может вызвать шарообразование, что негативно скажется на производительности мельницы.
4. Улучши внутреннюю вентиляцию
Хорошая внутренняя вентиляция существенно влияет на качество продукта и его выход. Эффективная вентиляция позволяет своевременно удалять мелкий порошок, чтобы предотвратить переизмельчение. Она также отводит тепло, образующееся во время помола, снижая внутреннюю температуру и уменьшая вероятность обезвоживания и засорения гипса. Хорошая вентиляция уменьшает буферные слои внутри мельницы и ускоряет скорость потока, повышая производительность мельницы. Однако чрезмерная вентиляция может увеличить частицы пыли, что негативно сказывается на тонкости цемента. Когда вентиляция превышает определенный уровень, это может увеличить расход электроэнергии на единицу продукции. Практика показывает, что существует оптимальный объем вентиляции между максимальной производительностью мельницы и минимальным потреблением электроэнергии.
Обычно скорость внутреннего ветра в мельницах закрытого типа составляет 0,8-1,0 м/с, в то время как для мельниц открытого типа требуется более высокая скорость ветра из-за более высоких температур. Если у шаровой мельницы есть проблемы с вентиляцией, мы можем улучшить это, открыв вентиляционные отверстия на входе сырья и сформировав разгрузочный желоб в виде ступеней. Также мы можем увеличить центральное отверстие разделительной плиты и разгрузочной решетки, усилив запирание воздуха в разгрузочном отверстии. Эти меры устраняют засорение материала и увеличивают площадь вентиляции.
5. Разумно определяй целевую тонкость цементных изделий
В реальном производстве, если целевая тонкость цементных продуктов установлена слишком высокой, это может свести на нет эффект от других мер. Это ограничит производительность мельницы и помешает усилиям по снижению энергопотребления. Поэтому очень важно определять целевую тонкость цементных изделий исходя из реальных условий.
6. Оптимизируй нагрузку на стальные шарики
Увеличение количества стальных шаров в мельнице повышает площадь контакта между стальными шарами и материалом, что приводит к увеличению производительности мельницы. Уменьшение диаметра стальных шаров увеличивает площадь поверхности на единицу объема, что также повышает производительность мельницы. Однако потребление электроэнергии имеет тенденцию увеличиваться с ростом количества загруженных стальных шаров. Как правило, в определенном диапазоне потребляемая мощность пропорциональна количеству стальных шаров и обратно пропорциональна их диаметру. Однако чрезмерная загрузка увеличивает количество столкновений и эффективность помола, что приводит к повышению энергопотребления. Мельница должна иметь оптимальную загрузку стальных шаров, которая минимизирует потребление энергии, что должно быть определено путем испытаний оптимальных коэффициентов загрузки и диаметра шаров.
7. Роль приспособлений для шлифовки
Добавление небольшого количества вспомогательного средства для измельчения в процессе помола может устранить слипание и агломерацию мелких порошков. Это ускоряет процесс измельчения, повышая эффективность и качество, одновременно снижая удельное потребление энергии. Использование вспомогательных средств для измельчения позволяет получить продукты с более высокой удельной поверхностью и уменьшить случаи переизмельчения. Кроме того, скорость потока материалов в мельнице увеличивается, сокращая время пребывания и влияя на тонкость помола на выходе. При измельчении в открытом контуре мы должны регулировать внутренние условия, чтобы соответствовать требованиям к тонкости продукта. При измельчении в закрытом контуре мы должны поддерживать выходную тонкость в пределах нормы, не допуская постепенного увеличения остатков на ситах. В противном случае это может снизить производительность мельницы и увеличить цикличность загрузки, что приведет к перегрузке элеватора и засорению, а в перспективе - к остановке производства. Подводя итог, можно сказать, что выбор и использование вспомогательных средств для измельчения - это сложная научная задача. Мы должны внимательно изучить следующие пять пунктов:
Учитывай свойства входящих материалов и проводи мелкомасштабные сравнительные испытания. Эффективность вспомогательных средств для измельчения зависит от материала, поэтому для достижения оптимальных результатов нужно сначала провести мелкомасштабные испытания в заданных технических условиях, а затем внедрить лучшие решения в более крупных масштабах.
Обращай внимание на условия помола и выбирай разные типы вспомогательных средств для измельчения. Вспомогательные средства для измельчения бывают в газовой, твердой и жидкой формах различных типов. Их адаптивность и эффективность различны, а требования различаются между открытыми и закрытыми контурами, что требует тщательного тестирования.
Убедись, что использование добавок для помола не оказывает негативного влияния на последующие процессы. При использовании добавок для помола в цементных мельницах учитывай их влияние на упаковку, процессы перегрузки сыпучих материалов, строительство и качество цементной продукции.
Сосредоточься на источнике и стоимости вспомогательных средств для измельчения. Экономические преимущества вспомогательных средств для измельчения тесно связаны с их ценой и предложением на рынке. Компании должны оценить и рассчитать эти факторы, прежде чем сделать оптимальный выбор.
Убедись, что добавки для измельчения соответствуют стандартам защиты окружающей среды. Многие добавки создаются с использованием побочных продуктов химических заводов, часто содержащих вредные вещества. При выборе добавок для помола не вводись в заблуждение низкими ценами; убедись, что добавки не загрязняют окружающую среду и не вредят здоровью рабочих. На практике средства для помола лучше всего работают на больших цементных мельницах. Учитывая их более высокую стоимость, для определения целесообразности их использования следует взвесить выгоды от снижения энергопотребления и увеличения производительности.
8. Оптимизация структуры и технических параметров классификатора
Основные технологии классификатора - это "диспергирование", "классификация" и "сбор". Диспергирование означает, что материал, поступающий в классификатор, должен быть максимально распределен, создавая пространство между частицами. Таким образом, конструкция диспергирующей пластины, ее скорость, пространство для диспергирования, влажность материалов и скорость потока - все это напрямую влияет на скорость диспергирования. Классификация подразумевает использование воздушного потока для разделения крупных и мелких частиц в течение их ограниченного времени пребывания в классификаторе. На эффективность классификации существенно влияют такие факторы, как скорость потока газа, скорость воздуха, характер воздушного потока, точки взаимодействия газа и твердого тела, а также конфигурация самого классификатора. Под сбором понимается способность классификатора улавливать крупные и мелкие порошки, которая зависит от метода сбора и конструкции компонентов сбора.
В 1979 году японская компания Onoda разработала классификатор O-Sepa. Этот классификатор сохраняет преимущества циклонных классификаторов, но при этом использует сепараторный ротор с плоскоспиральным принципом классификации воздушного потока, что значительно повышает эффективность классификации. Представленный классификатором сепараторного типа, он известен как высокоэффективный классификатор и считается третьим поколением классификаторов после центробежных и циклонных классификаторов.
Его эффективность классификации обычно превышает 80%. Однако он не включает в себя устройство для сбора тонкого порошка и требует более крупных рукавных фильтров или электрических пылеуловителей, что увеличивает инвестиции в оборудование и усложняет технологические схемы, что ограничивает его широкое распространение. Классификатор O-Sepa вместе с высокоэффективными рукавными пылеуловителями и шаровыми мельницами снижает циклические нагрузки с 200%-300% в центробежных системах до 100%-200%. При измельчении цемента он может достичь более 65% распределения частиц в диапазоне 3-30 микрометров, что обеспечивает высокую эффективность классификации, низкое энергопотребление, высокую производительность и разумное распределение частиц.
9. Соответствующим образом увеличь скорость вращения фрезы
Увеличение скорости особенно эффективно для небольших мельниц. В таких мельницах ударная сила слабее из-за меньшего диаметра. Увеличение скорости повышает дробильную способность мельницы на:
- Увеличение количества ударов по каждой мелющей среде внутри мельницы.
- Усиление трения и шлифовального действия между мелющими предметами и между мелющими предметами и футеровкой.
10. Понизь температуру поступающего клинкера
Усиль управление материальными ресурсами. Необходимо вносить коррективы в зависимости от температуры клинкера в хранилище. Операторы должны строго следовать правилам и получать соответствующую оценку. Используй термометры для контроля температуры и не допускай попадания высокотемпературного клинкера на мельницу.
Внедри в кулер распыление воды. Воду следует распылять в середине охладителя с помощью оцинкованных труб с небольшими отверстиями, чтобы контролировать расход воды в пределах 500-600 кг/ч. Это может снизить температуру выходящего цемента примерно на 10℃.
Хотя эти меры по распылению эффективно снижают температуру, у них есть побочные эффекты. Водяной пар может занести клинкерную пыль в дробилку в конце охладителя, образуя на внутренних стенках связки, что в итоге может нарушить нормальную работу дробилки. Поэтому регулярно контролируй температуру клинкера и соответствующим образом регулируй распыление воды. Периодически очищай клинкерную дробилку.
11. Характеристики и степень измельчения поступающих материалов
Типы и пропорции входящих материалов напрямую влияют на производительность мельницы, качество и удельный расход энергии. Любые смешанные материалы, используемые в цементе, обычно снижают прочность, но степень снижения зависит от активности материалов. Среди часто используемых смешанных материалов шлак обладает самой высокой активностью.
Однако если удельная поверхность шлака ниже 300 м²/кг, то его преимущества в прочности цемента не проявляются. Размалываемость материалов существенно влияет на производительность мельницы и качество продукта. Национальные стандарты определяют коэффициенты размалываемости в зависимости от удельной энергии, необходимой для измельчения. Поскольку на большинстве предприятий отсутствует специализированное испытательное оборудование, определить параметры процесса помола помогут мелкомасштабные испытания, в которых материалы сравниваются со стандартным песком. Измерив коэффициенты размалываемости сырьевых и топливных материалов, мы можем скорректировать загрузку и градацию мелющих тел, основываясь на научных методах.
Коэффициент шлифуемости сильно коррелирует со структурой материала. Даже в пределах одного и того же материала коэффициенты размалываемости могут различаться. Например, плотный и хорошо кристаллизованный известняк имеет низкий коэффициент размалываемости и труднее поддается измельчению. Измельчаемость клинкера зависит от состава его минералов и условий охлаждения. Факты показывают, что высокие значения KH и P, высокое содержание C3S, низкий C4AF и быстрое охлаждение дают более хрупкую текстуру и более высокие коэффициенты размалываемости. И наоборот, низкие значения KH и P, высокое содержание C2S и C4AF и медленное охлаждение приводят к образованию более плотных, жестких клинкеров с более низкими коэффициентами размалываемости, что делает их более трудными для измельчения.
Коэффициент размалываемости шлака может существенно различаться. Шлак, который подвергается быстрому охлаждению после производства, часто бывает пористым и мелким, что дает более высокий коэффициент размалываемости - около 1,2-1,3. Напротив, шлак, который значительно охлаждается перед быстрой закалкой, образует более плотные, тяжелые кристаллические частицы, что приводит к более низкому коэффициенту размалываемости - около 0,7-0,9, что делает его более сложным для размалывания.
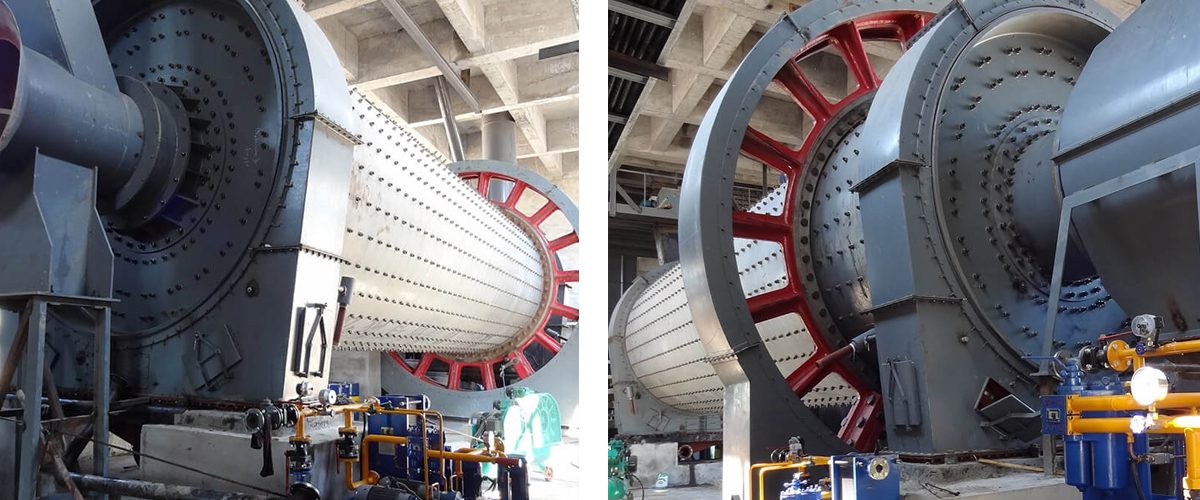
Другие способы повысить производительность цементной мельницы
1. Основа для разумной корректировки средств измельчения
Разумная подгонка мелющих тел зависит от физико-химических свойств измельчаемых материалов, метода измельчения и требуемой тонкости продукта. Анализ остатков на ситах - эффективное средство, позволяющее судить о том, насколько обоснована градация мелющих тел.
Основа для регулировки мелющих тел включает в себя:
- При фиксированном размере частиц поступающих материалов меньшие стальные шары имеют большую общую площадь поверхности, чем большие, что увеличивает возможности их контакта с материалами. И наоборот, более крупные стальные шары обеспечивают большую энергию и ударную способность дробления. Для материалов с большим средним размером частиц и более высокой твердостью следует использовать шары большего среднего диаметра; для более мягких материалов подойдут шары меньшего диаметра. Для мельниц меньшего диаметра используются шары меньшего среднего диаметра.
- Если размалываемость поступающих материалов хорошая, можно выбрать небольшие стальные шары; если размалываемость плохая, нужны более крупные стальные шары.
- Выбор диаметра шаров также связан с количеством материала, проходящего через мельницу на единицу объема. При измельчении в замкнутом цикле возврат крупных частиц увеличивает пропускную способность на единицу объема, что позволяет немного амортизировать стальные шары при ударе. Поэтому в сценариях с высокой отдачей предпочтительнее использовать более крупные стальные шары, а в остальных случаях выбирать шары меньшего размера.
- Если на выходе требуется тонкость, следует использовать маленькие стальные шарики, в противном случае подойдут более крупные.
- В однокамерных мельницах обычно используются стальные шары, а в двухкамерных - стальные шары в первой камере и стальные секции во второй.
- Размеры мелющих тел должны быть хорошо подобраны. Технические характеристики стальных шаров обычно варьируются от 3 до 5 уровней, а стальных секций - от 2 до 5 уровней.
- Пропорция стальных шариков разного размера может следовать принципу "маленький на обоих концах, большой в середине". При использовании двух видов стальных секций каждая должна занимать половину.
- При соблюдении требований к размеру частиц средний размер частиц должен быть минимизирован, чтобы увеличить площадь контакта и частоту ударов, при этом отношение диаметра к длине стальных секций должно быть небольшим из-за быстрого радиального износа. Разница между длиной и диаметром стальных секций должна составлять около 5 мм.
2. Разумно отрегулируй коэффициент возврата и степень измельчения мелющих тел
В целом, чтобы уменьшить переизмельчение, скорость заполнения первой камеры при измельчении в замкнутом цикле часто выше, чем второй, что ускоряет скорость подачи материала. Скорость возврата 100-150% обычно дает самую высокую часовую производительность. Если скорость возврата слишком высока, то, хотя тонкость помола может соответствовать стандартам, удельная площадь поверхности уменьшается. По мере износа мелющих тел в процессе производства коэффициент заполнения уменьшается. Поначалу это проявляется не в снижении часовой производительности, а в увеличении нормы возврата, уменьшении площади поверхности цемента и снижении 3-дневной прочности на сжатие. Когда скорость возврата становится слишком высокой, это приводит к перенасыщению, что в свою очередь вызывает падение часовой производительности. Поэтому очень важно определить, нужно ли дополнять мелющие среды, исходя из скорости возврата и удельной площади поверхности. Если часовая производительность значительно падает, необходимо очистить мельницу и заново провести градацию мелющих тел.
3. Мелющая среда в камерах тонкого помола
Мелющие среды - одна из основных мер по оптимизации работы мельницы. В настоящее время в зарубежных цементных мельницах в камерах тонкого помола, как правило, используются небольшие стальные шары, а не стальные секции, потому что стальные секции потребляют примерно на 20-30% больше энергии.
Высококачественные маленькие стальные шары изнашиваются меньше, чем стальные секции, и производят более сферические частицы цемента, которые превосходят те, что производятся стальными секциями. Однако у стальных секций есть свои преимущества, например, более высокая скорость потока материала и предотвращение агломерации цемента в мельнице. В последние годы постоянно ведутся споры о том, что использовать в камерах тонкого помола - стальные секции или стальные шары. Одни выступают за стальные секции, другие предпочитают стальные шары. Это решение требует специального анализа с точки зрения измельчения. Функция измельчения в мельнице включает в себя как дробление, так и измельчение. Оптимизация условий работы мельницы заключается в балансировании этих двух возможностей для повышения эффективности измельчения, обеспечивая приемлемый уровень как производительности, так и тонкости продукта. Правильный анализ соответствия возможностей дробления и измельчения при различных условиях имеет решающее значение для определения того, что лучше использовать - стальные секции или стальные шары в камерах тонкого помола.
- Каждая камера мельницы выполняет функции как дробления, так и измельчения, хотя и в разной степени. Основная функция камеры тонкого помола - измельчение, причем размольные способности небольших стальных шаров и секций различны. Эффективность измельчения зависит в основном от площади поверхности контакта мелющих тел с материалами. Большая площадь поверхности контакта обеспечивает больше возможностей для измельчения, что приводит к более высокой скорости образования продукта в единицу времени. При равном качестве секций площадь поверхности контакта выше из-за их линейного характера контакта по сравнению с шарами. Для одиночных камер при одинаковой загрузке мелющей среды и одинаковом исходном материале производительность в единицу времени в секционной камере выше, чем в шаровой, что подтверждается теорией измельчения и практическим применением. Стоит отметить, что современные размеры мелющих сред в камерах тонкого помола, как правило, слишком велики по сравнению с материалами, отчасти из-за ограничений по ширине сита.
Заключение
Практика доказала, что основные пути достижения качественного, энергоэффективного и высокопроизводительного помола цемента включают: "добавление процессов предварительного измельчения перед помолом, конструктивные улучшения внутри мельницы и выбор эффективных классификаторов после помола". Предварительное измельчение - это "предпосылка", внутренние модификации - "фундамент", а оптимальный подбор классификаторов после помола - "гарантия". Для получения дополнительной информации или запросов, пожалуйста связаться с нами!