С момента ввода в эксплуатацию в мае 2007 года система предварительного помола цемента компании "А" часто сталкивалась с неполадками в работе валкового пресса. К этим проблемам относятся низкое и нестабильное рабочее давление с обеих сторон, неправильная регулировка клапана распределения материала, крупный размер частиц материала, выходящего из валкового пресса, низкая часовая производительность, высокий расход энергии на помол и низкая общая экономическая эффективность. В этой статье мы поделимся своим опытом и мерами по улучшению управления валковым прессом.
Анализ проблем и их решение
1. Причины и регулировка нестабильного давления
Материал попадает в валковый пресс между подвижным и неподвижным валиками через верхний загрузочный лоток. Мы обнаружили, что пластина регулировки материала со стороны подвижного валика выдвинулась в сторону неподвижного валика. Это привело к тому, что точка выгрузки сместилась в сторону неподвижного валика. В результате на стороне неподвижного валика оказалось слишком много материала, а на стороне подвижного - почти нет. Такое неравномерное распределение привело к нестабильному давлению и, в конечном итоге, к большим размерам частиц на выходе.
Чтобы решить эту проблему, в августе 2010 года Дарко отрегулировал пластину регулировки материала со стороны подвижного ролика. Мы перенесли ее положение со стороны неподвижного ролика на внешнюю сторону подвижного ролика. Также мы изменили угол ее наклона с 45° на 60°. Кроме того, мы отрегулировали начальный зазор между роликами до 10 мм. Это позволило материалу правильно проходить между валиками и равномерно распределяться, тем самым контролируя колебания давления.
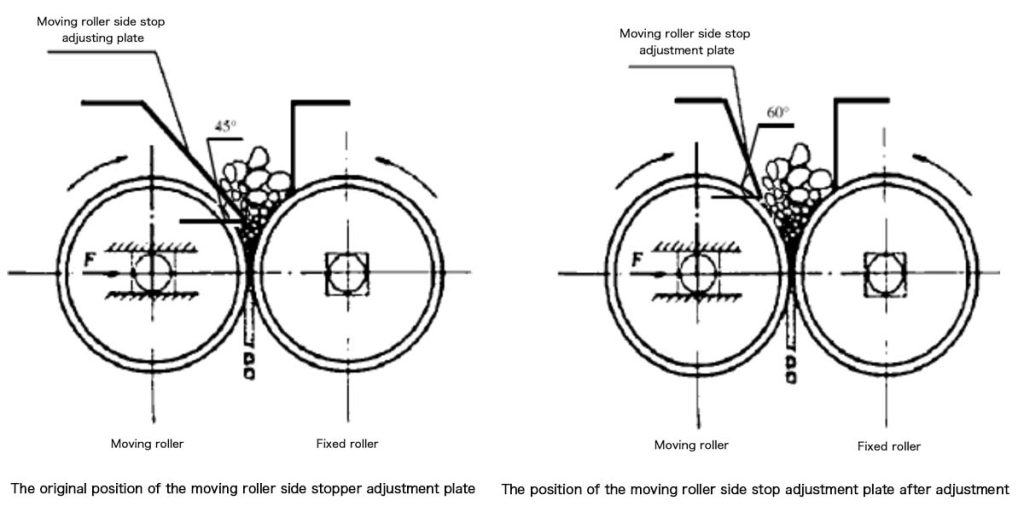
2. Причины и регулировка низкого рабочего давления
Внимательно осмотрев валковый пресс и гидравлическую систему, мы обнаружили, что начальное давление с обеих сторон системы составляло 6,0 МПа. Оборудование могло запуститься только тогда, когда давление было загружено до 5,5-6,5 МПа. Операторы обычно увеличивали давление до 6,0 МПа, а затем останавливались. Из-за ограничений начального зазора между вальцами давление масла в гидроцилиндре при 6,0 МПа было недостаточным. Даже если зазор между роликами увеличивался, давление не могло достичь рабочего давления в 8,2 МПа.
Мы поняли, что начальное давление оказывает значительное влияние на рабочее давление. Поэтому мы отрегулировали начальное давление до 6,5 МПа, стабилизировав при этом поток материала на входе. После этой регулировки рабочее давление с обеих сторон увеличилось с 7,4-7,8 МПа до 8,2-8,6 МПа, что привело к заметному уменьшению размера частиц.
3. Регулировка клапана распределения материала
В процессе измельчения материал образует лепешку и выгружается из нижней части между двумя валиками. При достаточной подаче материал эффективно прессуется. Однако эффект прессования для краевого материала не так хорош, как для центрального. Роль клапана распределения материала заключается в том, чтобы отделить хорошо спрессованный материал от плохо спрессованного.
Мы ошибочно посчитали, что меньшее отверстие распределительного клапана лучше, и настроили его на 20%. В результате готовый продукт содержал крупный материал около 10 мм. Осмотрев боковую дверь валкового пресса, мы обнаружили значительное скопление материала в краевом желобе, что мешало плавному течению. Проведя дополнительные настройки, мы обнаружили, что установка отверстия распределительного клапана на 23% устранила скопление материала, обеспечив плавное поступление в возвратную ленту.
Заключение
Благодаря этим мерам мы успешно уменьшили средний размер частиц клинкера из валкового пресса с 3,81 мм до 1,54 мм. Коэффициент дробления улучшился с 4,09 до 10,10. Внешний вид измельченного материала стал порошкообразным, и большинство частиц можно было легко раздробить вручную. Кроме того, часовая производительность шаровая мельница увеличилась на 13,1%, а расход энергии на измельчение в системе снизился на 16,6%. Эти улучшения значительно повысили экономическую эффективность и стабильность работы системы. Если ты столкнешься с подобными проблемами, не стесняйся, пожалуйста. связаться с нами. Мы рады помочь!