Энергопотребление систем измельчения является ключевым показателем их эффективности. В настоящее время технологии измельчения развиваются в сторону полностью бесшаровых систем, таких как Вертикальные мельницы или вальцовые прессы, а также более крупное оборудование. С развитием цементных технологий общее потребление энергии в цемент Производство демонстрирует следующие тенденции:
- Шаровая мельница Эра: Более 100 кВт-ч/т
- Эпоха частичного измельчения постели: Около 90 кВт-ч/т
- Эра без мяча: Ниже 80 кВт-ч/т
Эта тенденция говорит о том, что технология измельчения постоянно совершенствуется, чтобы добиться снижения энергопотребления и повышения эффективности производства.
Методы снижения энергопотребления в системах шаровых мельниц
1. Влияние материалов на энергопотребление системы измельчения
1.1 Влияние измельчаемости материала
Производительность системы помола цемента тесно связана с размолоспособностью клинкера. Минеральный состав и скорость охлаждения клинкера влияют на его размалываемость. Например, клинкеры с высоким содержанием C3S и низким содержанием C4AF обычно демонстрируют хорошую размалываемость. И наоборот, клинкеры с высоким содержанием C2S и C4AF приводят к повышенному расходу энергии. Поэтому оптимизация минерального состава и условий охлаждения клинкера эффективно снижает расход энергии.
1.2 Влияние размера частиц материала
Уменьшение размера частиц исходного материала значительно повышает производительность мельницы, тем самым снижая расход энергии. Когда средний размер частиц исходного материала уменьшается с 30 мм до 2 мм-3 мм, производительность мельницы может увеличиться более чем на 50%. Кроме того, использование процесса предварительного дробления "больше дробления, меньше измельчения" эффективно минимизирует переизмельчение и повышает эффективность мельницы.
1.3 Влияние температуры и влажности материала
Когда температура исходного материала превышает 80 °C, внутренняя температура мельницы может превысить 120 °C, что приведет к снижению эффективности помола и увеличению расхода энергии. Поэтому очень важно контролировать температуру клинкера и поддерживать содержание влаги в пределах от 1.0% до 1.5%, чтобы обеспечить стабильную работу мельницы.
2. Влияние вентиляции мельницы на потребление энергии
Усиление вентиляции внутри мельницы уменьшает буферный эффект и увеличивает скорость потока материала, тем самым снижая температуру и увеличивая производительность мельницы. Скорость воздушного потока внутри мельницы должна поддерживаться в пределах от 0,9 до 1,1 м/с, чтобы избежать переизмельчения и повышенного расхода энергии. Кроме того, улучшение герметичности системы для уменьшения утечек воздуха имеет решающее значение для снижения энергопотребления.
3. Регулярное техническое обслуживание и осмотр мельницы
Регулярная проверка и обслуживание мельницы, а также оптимизация таких параметров, как загрузка шаров, степень заполнения и эффективность отбора, помогут сохранить стабильность системы и высокую эффективность работы. Правильная настройка конфигурации мелющего тела необходима для достижения оптимальной производительности мельницы.
4. Влияние распределения частиц по размерам на качество продукта и потребление энергии
Оптимальный гранулометрический состав для цемента колеблется от 3 мкм до 32 мкм, при этом мелкие частицы не должны превышать 10%. Регулярный анализ гранулометрического состава помогает своевременно корректировать шаровые загрузки, повышая эффективность работы мельницы и снижая энергопотребление.
Оптимизация комбинированных систем измельчения
В традиционных комбинированных системах помола валковые прессы и шаровые мельницы выполняют разные задачи по измельчению. Оптимизировав управление шаровыми мельницами, мы сможем эффективно снизить энергопотребление и повысить качество цемента.
- Преимущества роликовых прессов: Увеличение рабочего давления вальцового пресса значительно повышает урожайность при стабильных условиях работы.
- Увеличение общей площади поверхности стальных шариков: Регулировка диаметра и количества стальных шаров увеличивает размольную способность мельницы, тем самым повышая эффективность помола.
- Регулировка конструкции мельницы: Укорачивание камеры грубого помола и увеличение эффективной длины камеры тонкого помола помогает улучшить способность мельницы к тонкому помолу.
Методы снижения энергопотребления в вертикальных мельничных установках
Вертикальные мельницы - эффективное и энергосберегающее помольное оборудование. Их энергопотребление в основном приходится на главный двигатель и циркуляционный вентилятор. Вот предложения по снижению энергопотребления в системах вертикальных мельниц:
1. Выбор оптимальных энергетических параметров
Операторы должны регулировать рабочие параметры, основываясь на тенденциях изменения параметров системы, чтобы добиться высокой производительности и низкого потребления энергии.
2. Рациональное использование воздушного потока системы
Контролируя поток воздуха в мельнице и минимизируя утечки воздуха, можно эффективно снизить энергопотребление циркуляционного вентилятора.
3. Регулировка кольца для удержания материала
Регулярная проверка и регулировка высоты удерживающего кольца материала позволяет избежать неэффективной шлифовки из-за неправильной толщины слоя материала.
4. Повышение урожайности и скорости работы оборудования
Обеспечение непрерывной работы оборудования и избежание ненужных отключений помогают повысить стабильность и снизить расход энергии.
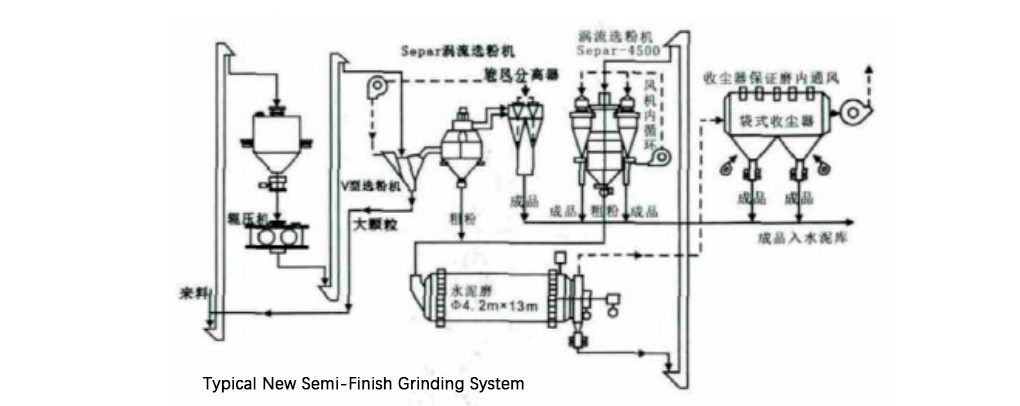
Заключение
Каждый процесс и этап производства цемента содержит потенциал для снижения энергопотребления. Комплексно оптимизировав систему помола, мы сможем значительно снизить энергопотребление, уменьшить себестоимость продукции и повысить конкурентоспособность на рынке. Будучи профессионалами в цементной промышленности, овладение энергосберегающими технологиями и методами управления будет способствовать достижению целей устойчивого развития.
За дополнительной информацией или вопросами обращайся по адресу связаться с нами.