Введение
Компания S эксплуатирует шесть силосов для цемента Φ18×35. Как показано на схеме, под силосами 1, 2, 3 и 4, 5, 6 находятся желоба для транспортировки материалов к внешнему элеватору. В августе 2020 года компания планировала увеличить количество сортов цемента. Для этого потребовалось переместить цемент из силоса 4 в желоб под силосами 1, 2 и 3. Из-за большого объема перекачки (300 м³/ч) и небольшой разницы в высоте между точками подачи и выгрузки установка желоба для воздушной транспортировки была нецелесообразной. Другие варианты оборудования были либо энергоемкими, либо подверженными износу, либо несовместимыми, что усложняло процесс выбора и проектирования.В этот момент отдел хранения и транспортировки узнал о Даркопневматический цепной конвейер. Они связались с технической группой компании Darko. После осмотра площадки и продолжительных обсуждений они окончательно согласовали технический план использования пневматического цепного конвейера. Заказ был размещен в конце 2020 года. Из-за плотного производственного графика установка началась только в июле 2021 года и была завершена в течение месяца. Система работала исключительно хорошо и оправдала все ожидания. Вот ключевые технические особенности проекта:
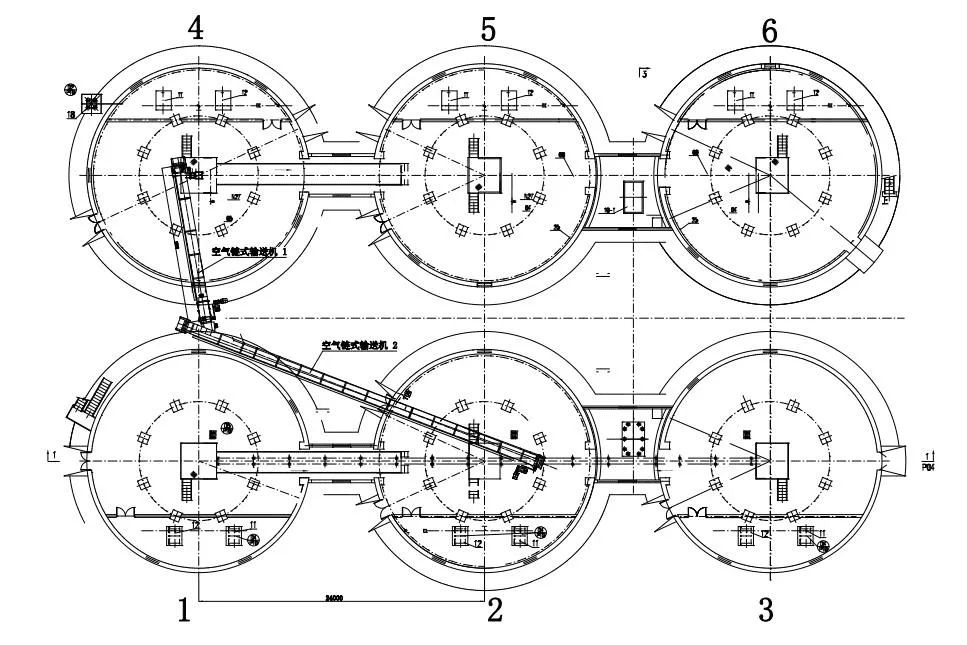
1. Гарантированная высота процесса
Пневматический цепной конвейер может транспортировать материал в горизонтальном направлении. Эта конструкция перемещает материал из бункера 4 в желоб под бункером 2. Эта установка предполагает изгиб примерно на 135°. Чтобы сэкономить на высоте, мы приняли две меры:
Во-первых, мы изменили способ подачи материала на входе первого воздушного цепного конвейера с обычной верхней подачи на боковую. Эта регулировка позволяет материалу падать прямо из разгрузочного клапана бункера в боковую часть оборудования, экономя около 500 мм пространства.
Во-вторых, на стыке двух воздушных цепных конвейеров мы перешли от типичного вертикального перекрытия к горизонтальному. Выгрузка с первого конвейера подается на боковую сторону второго конвейера. Из-за угла в 135° это горизонтальное перекрытие создавало треугольную область, в которой мог скапливаться материал, потенциально препятствуя транспортировке. Чтобы предотвратить скопление материала, мы установили на стыке воздушную подушку, подаваемую обычной воздуходувкой Рутса. Это значительно снизило сопротивление, обеспечив плавный поток материала. В результате такая конструкция сэкономила около 1000 мм высоты процесса, позволив материалу из силоса 4 беспрепятственно попадать в желоб под силосом 2.
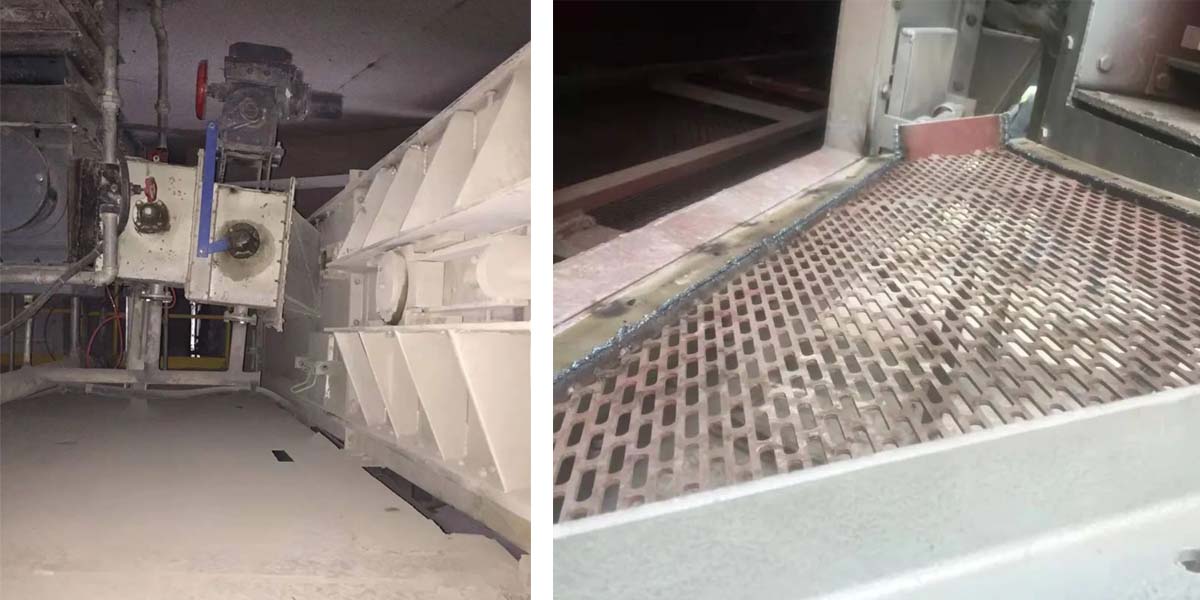
2. Рациональный выбор оборудования
Для объема переноса 300 м³/ч в простой схеме с одним устройством и минимальными углами, как правило, используется модель FUK630. Однако, учитывая текущие требования к процессу, в частности, стык 135° и торцевой разряд, мы остановили свой выбор на модели FUK800. После нескольких месяцев эксплуатации мы убедились, что эта модель соответствует требованиям к производительности 300 м³/ч и справляется с внезапным повышением давления в бункере, не вызывая засорения.
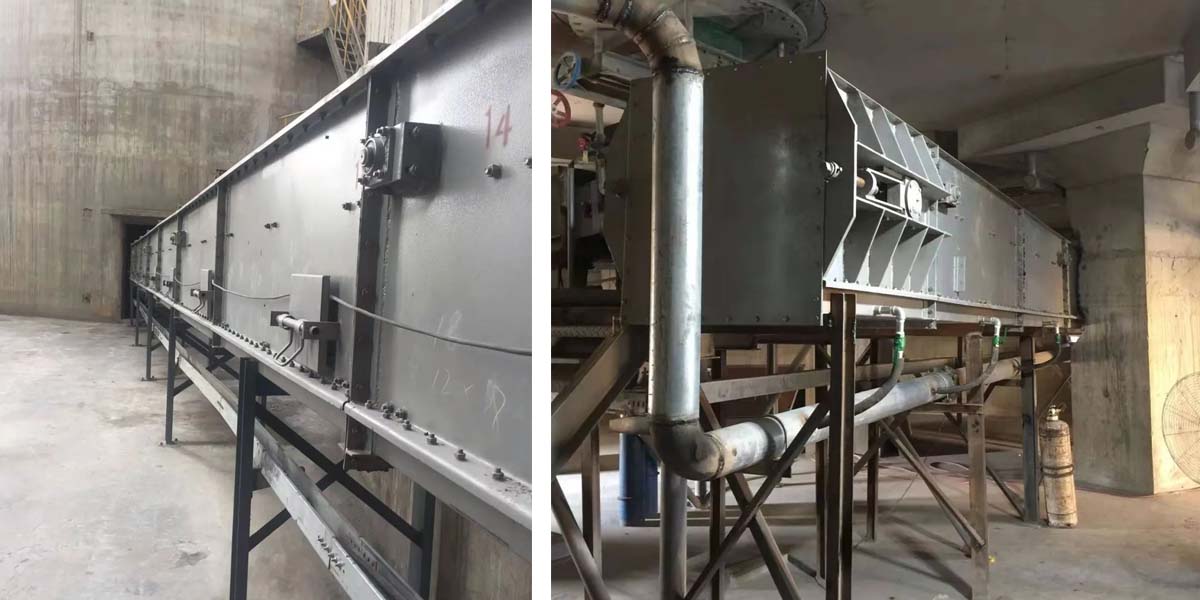
3. Низкое потребление энергии
Характеристики двух воздушных цепных конвейеров таковы: первый - FUK800×13,5 метров с мощностью 5,5 кВт, а второй - FUK800×31,7 метров с мощностью 11 кВт. Оба конвейера используют одну воздуходувку Рутса мощностью 18,5 кВт для подачи воздуха, в результате чего общее расстояние транспортировки составляет 45,2 метра, а общая потребляемая мощность - 35 кВт. Это немного выше, чем у FUK630 (30 кВт), но значительно ниже, чем у традиционных цепных конвейеров (75-90 кВт), что позволяет добиться экономии энергии более чем на 50%. Кроме того, несколько меньшая скорость цепи увеличивает срок службы конвейера, сохраняя полную герметичность корпуса, что соответствует всем экологическим стандартам.
Заключение
Хотя выбор высокопроизводительного оборудования очень важен, не менее важна и разработка технологического процесса с учетом характеристик оборудования и условий на участке. Успех технических решений зависит от того, насколько хорошо характеристики оборудования соответствуют конкретной ситуации. Многие пользователи придают этому аспекту первостепенное значение. Опыт проектирования также неоценим в этом процессе, поэтому очень важно выбрать не только правильное оборудование, но и опытного производителя.
Если Вас заинтересовали наши технические решения или Вам нужна дополнительная информация, пожалуйста, не стесняйтесь связаться с нами. Мы рады помочь!