Для чего используется роликовый пресс?
Валковый пресс, также известный как прессовая мельница, валковая мельница или двухвалковая машина. Валковый пресс - это измельчающее устройство, используемое в промышленности, в частности, в производстве цемента. Он состоит из двух вращающихся в противоположных направлениях валков, которые сжимают и измельчают материал. Этот процесс значительно уменьшает размер частиц материала, что делает его эффективной альтернативой традиционным методам измельчения.
Валковый пресс обладает высокой эффективностью измельчения, низким энергопотреблением и высокой производительностью, благодаря чему он широко используется в цементной промышленности. Однако в процессе эксплуатации возникают различные проблемы, обусловленные такими факторами, как конструкция, использование и внешние условия. Эти проблемы приводят к плохим условиям работы, неадекватному контролю подачи и сбоям в работе гидравлической системы, что негативно сказывается на производительности вальцового пресса. Чтобы решить эти проблемы, мы анализируем основные причины и внедряем усовершенствования по нескольким аспектам, включая конструкцию и использование. В результате мы оптимизируем процесс модификации, повышаем эффективность и добиваемся лучших результатов в работе.
I.Роль валкового пресса на цементных заводах
В цементные заводы, operators use the roller press to grind clinker and other raw materials into fine powder. Typically, they employ it alongside other grinding systems, such as ball mills, to enhance overall efficiency and reduce energy consumption. Furthermore, the roller press’s capacity to manage high pressure and produce fine products makes it an essential component of modern cement production.
II.Различия между валковым прессом и шаровой мельницей
Основное различие между валковым прессом и шаровая мельница заключается в их механизмах измельчения. Вальцовый пресс сжимает материал между двумя валками под высоким давлением, что приводит к снижению энергопотребления и повышению эффективности. В шаровой мельнице, напротив, измельчение материала происходит за счет удара и трения шаров, что, как правило, требует больше энергии. Поэтому вальцовые прессы обычно лучше с точки зрения энергоэффективности и тонкости помола.
III.Проблемы перекоса в валковых прессах
Перекос означает несоосность между роликами вальцового пресса и может возникнуть в результате механического износа или неправильной установки. Такой перекос может привести к неравномерному распределению давления, что в конечном итоге снижает эффективность измельчения. Поэтому регулярное техническое обслуживание и правильная центровка имеют решающее значение для минимизации перекоса и обеспечения оптимальной производительности вальцового пресса.
IV.Анализ проблем с валковыми прессами
1. Содержание мелкого порошка на выходе
Содержание мелкого порошка на выходе из вальцового пресса, также известное как выход первого прохода, напрямую отражает эффективность процесса прессования. Однако многие компании упускают этот важный аспект из виду. Тестирование образцов, полученных с различных предприятий, показало, что немецкий вальцовый пресс BHS достигает тонкости на выходе 33% на сите 0,9 мм и 64% на сите 0,08 мм (при этом 36% ниже 0,08 мм). В отличие от этого, многие из этих машин не достигают подобных результатов.
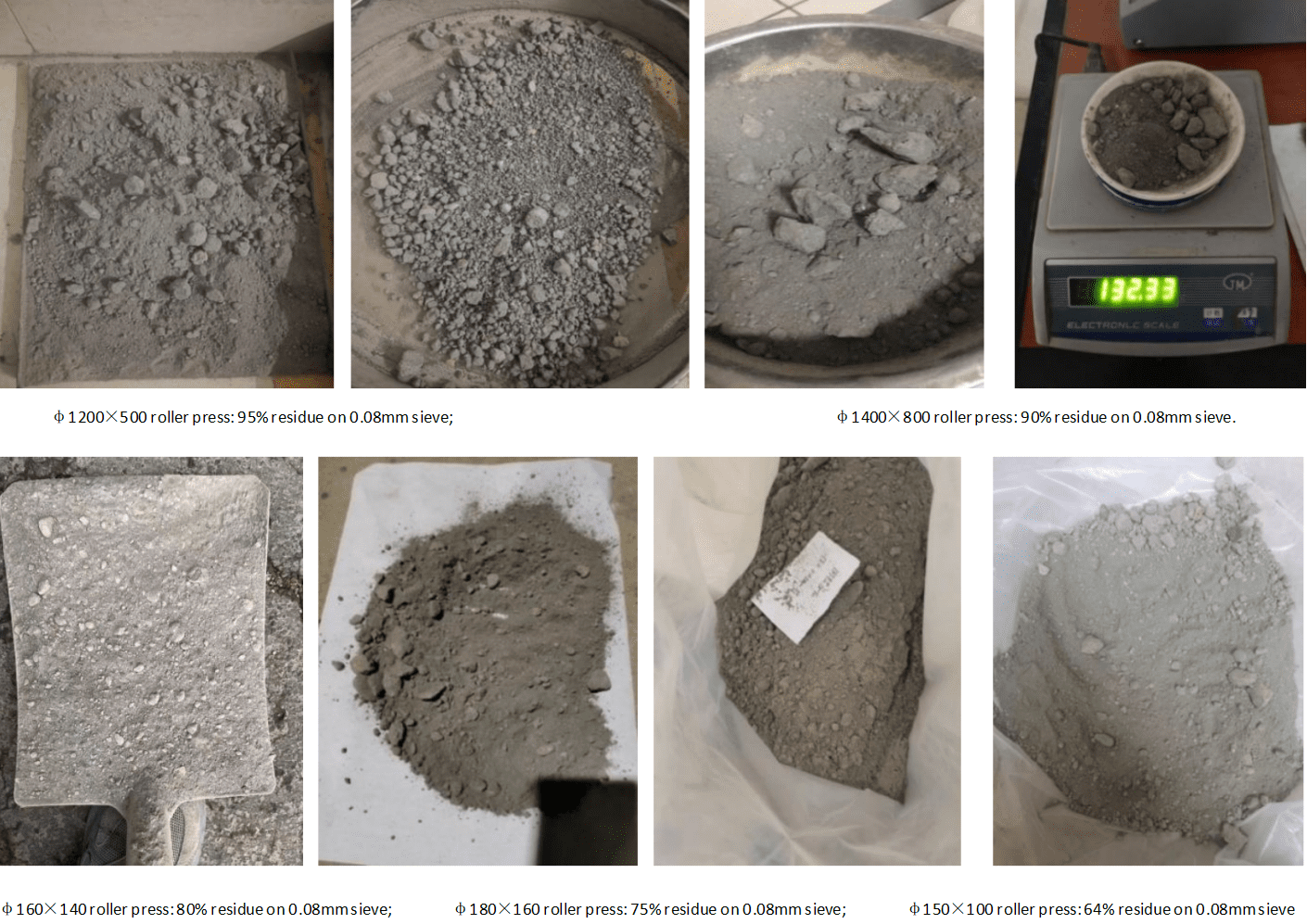
2. Рабочее давление
Усилие прессования является наиболее фундаментальным параметром, определяющим эффективность работы вальцового пресса. Чтобы рассчитать общее усилие F (в кН) роликового пресса, мы используем формулу:
F=n⋅S⋅Pr
где:
- n= количество гидравлических цилиндров
- S= эффективная площадь гидроцилиндра (м²)
- Pr = давление в гидравлической системе (МПа)
Кроме того, среднее давление ролика Pcp(в кН/м²) определяется:
Pcp=2F/D⋅B⋅sinα
Вот:
- D = диаметр шлифовального валика (м)
- B = эффективная ширина размольного валка (м)
- α = угол давления, также известный как угол прикуса (°)
Расчет прогнозируемого давления
Кроме того, прогнозируемое давление PT (в кН/м²) рассчитывается с помощью:
PT=F/B⋅D
Влияние максимального давления валков на эффективность прессования
На практике максимальное давление ролика существенно влияет на эффект прессования. В частности, когда линия, соединяющая центры двух роликов, установлена на 0 градусов, угол давления начинается с 8,3 градуса и заканчивается на -1,6 градуса. Примечательно, что максимальное пиковое давление возникает при 1,5 градусах, что немного превышает среднее давление в два раза.
Кроме того, решающую роль играет гидравлическая система вальцового пресса, которая обеспечивает динамическое давление вальцов, необходимое для сжатия материала. Эта система состоит из различных компонентов, включая маслостанцию, гидравлические цилиндры, азотные мешки, электромагнитные клапаны, переливные клапаны, манометры, маслопроводы и шкаф управления. Если в конфигурации отсутствуют клапаны регулировки демпфирования и клапаны регулировки хода, то оптимальных результатов прессования достичь не удастся. Поэтому в некоторых случаях добавление небольших мешков с азотом может помешать отображаемому давлению точно отражать фактические изменения давления.
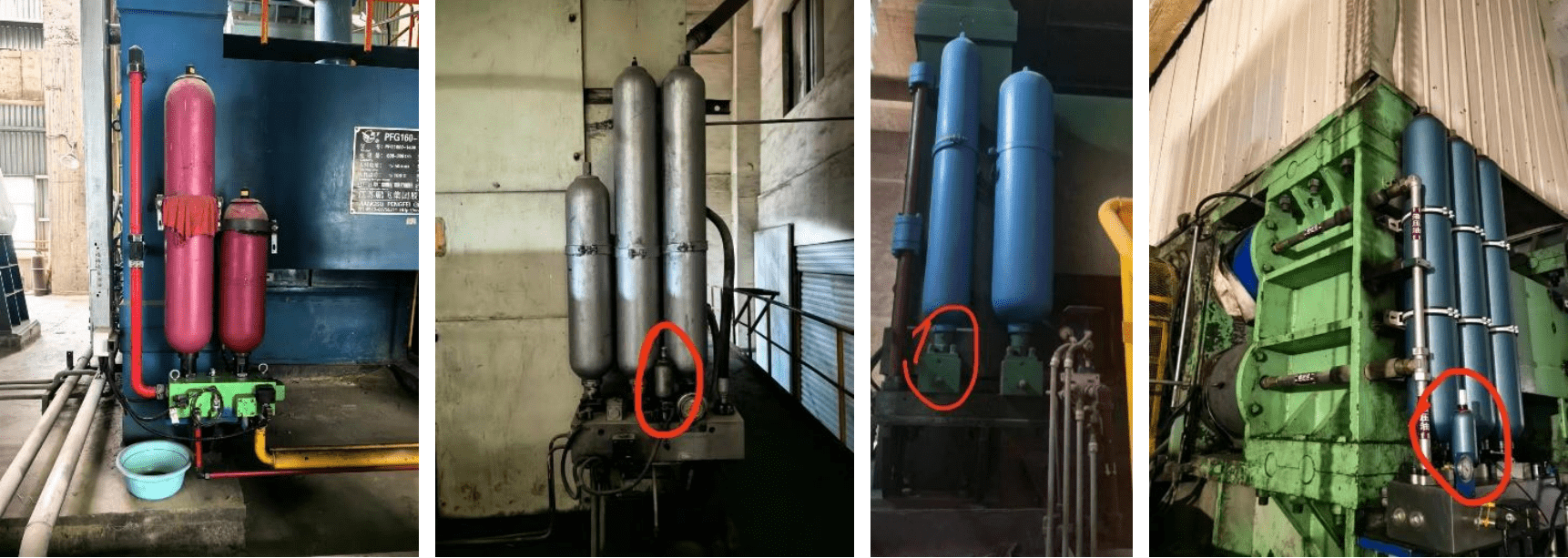
Конфигурация азотного мешка и управление давлением
- Размер азотных мешков и трубопроводов должен быть рассчитан исходя из размера гидравлических цилиндров. Кроме того, использование слишком маленьких труб приведет к увеличению сопротивления. При параллельной установке, когда используется один большой и один маленький азотный мешок, сначала срабатывает маленький мешок, а затем большой. В результате этот процесс неоднократно подавляет открытие зазора между роликами, который работает в цикле втягивания, втягивания и выдвижения, что в конечном итоге приводит к низкой эффективности прессования.
- Кроме того, давление в азотных мешках установлено на уровне 8, 10 и 12 МПа, то есть только один азотный мешок работает в определенном диапазоне, а два других становятся неэффективными. Хотя эта теория перепада давления была первоначально предложена немецкими инженерами, она не дала ожидаемых результатов из-за значительных различий в свойствах материалов. Поэтому немцы не стали развивать этот подход.
- Как правило, рекомендуется устанавливать давление в азотном мешке на уровне 60-80% от минимального давления в системе. Такой подход гарантирует, что, когда система работает при минимальном рабочем давлении, между азотными мешками и клапаном отключения сохраняется определенный уровень безопасности. Однако для определения эффективности системы ее рабочее состояние должно контролироваться на месте. Если температура масла слишком высока или слишком низка, это свидетельствует о том, что система находится в плохом рабочем состоянии, что серьезно влияет на эффективность прессования.
3. Скорость вращения роликов
Скорость вращения валков вальцового пресса может быть выражена двумя способами: первый - окружная линейная скорость V роликов, а другая - скорость вращения роликов. Окружная линейная скорость связана с производительностью, энергопотреблением и стабильностью работы. Как правило, более высокая скорость вращения роликов приводит к увеличению производительности; однако слишком высокая скорость может вызвать большее относительное скольжение между роликами и материалом, что приводит к плохому сцеплению и повышенному износу поверхностей роликов, что отрицательно сказывается на производительности роликового пресса.
В настоящее время типичная скорость вращения роликов колеблется от 1,0 до 1,75 м/с, при этом некоторые эксперты считают, что она не должна превышать 1,5 м/с. Линейная скорость роликов обычно находится в диапазоне от 1,0 до 1,7 м/с, при этом большинство из них работает на уровне 1,5-1,7 м/с, а некоторые даже достигают 2,0-2,2 м/с. При выборе скорости очень важно отдать предпочтение эффекту выдавливания; этот эффект должен быть основан на фактическом отборе проб. Если скорость слишком высока, время прессования сокращается, что приводит к усилению вибраций в оборудовании. Значительные колебания силы становятся трудно контролируемыми, что приводит к чрезмерному потреблению энергии без достижения желаемого эффекта прессования.
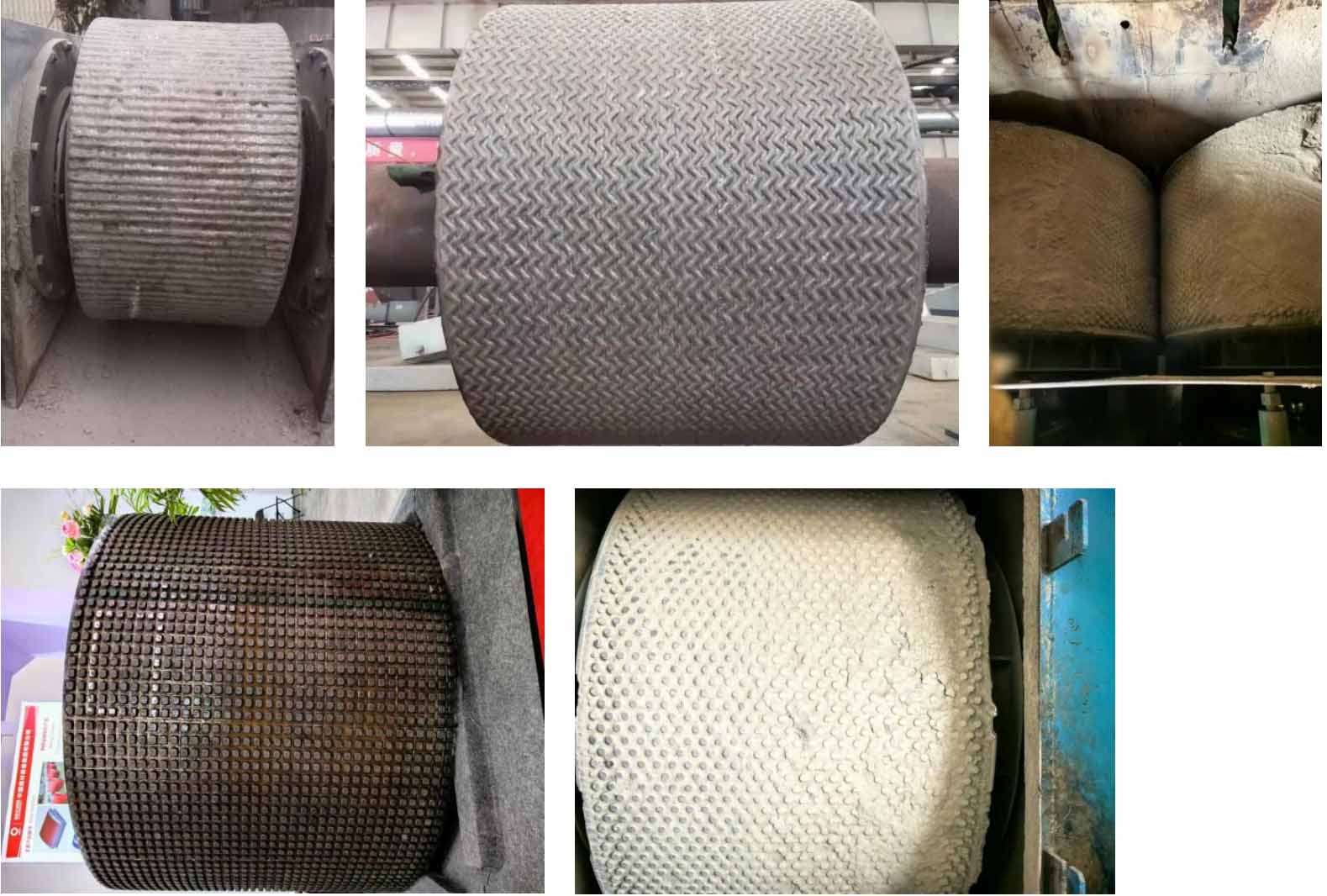
4. Рабочий зазор и свойства материала
На работу зазора между валками влияют различные факторы, включая свойства материала (такие как твердость, размер частиц и содержание влаги), форму поверхности валков, скорость, давление и метод управления давлением. Существует два способа управления давлением в гидроцилиндре: управление постоянным давлением и управление постоянным зазором. Однако, независимо от используемого метода, оба они являются в корне неверными с точки зрения гидравлики, поскольку давление и зазор постоянно колеблются.
Время срабатывания манометра составляет 200 миллисекунд, что усложняет управление регулировкой давления масляного насоса. Это, в свою очередь, влияет на давление в гидроцилиндре и, как следствие, на зазор между роликами. В результате возникают две основные проблемы: во-первых, запаздывает реакция, во-вторых, возникают чрезмерные перепады давления. Эти факторы препятствуют стабильной работе вальцового пресса и негативно влияют на эффективность прессования.

5. Устройство подачи
В настоящее время в большинстве роликовых прессов используется подающее устройство, которое направляет материал прямо из бункера в зазор между роликами, протягивая его между двумя роликами. Этот процесс обычно называют "углом втягивания" вальцового пресса. Однако управление потоком в двух направлениях не представляется возможным, поскольку диапазон регулировки ограничен, что затрудняет достижение точного и стабильного управления. Кроме того, два других направления вообще не поддаются регулировке. В результате часто возникают такие проблемы, как сегрегация материала и несоосность роликов, что приводит к неуправляемым условиям.
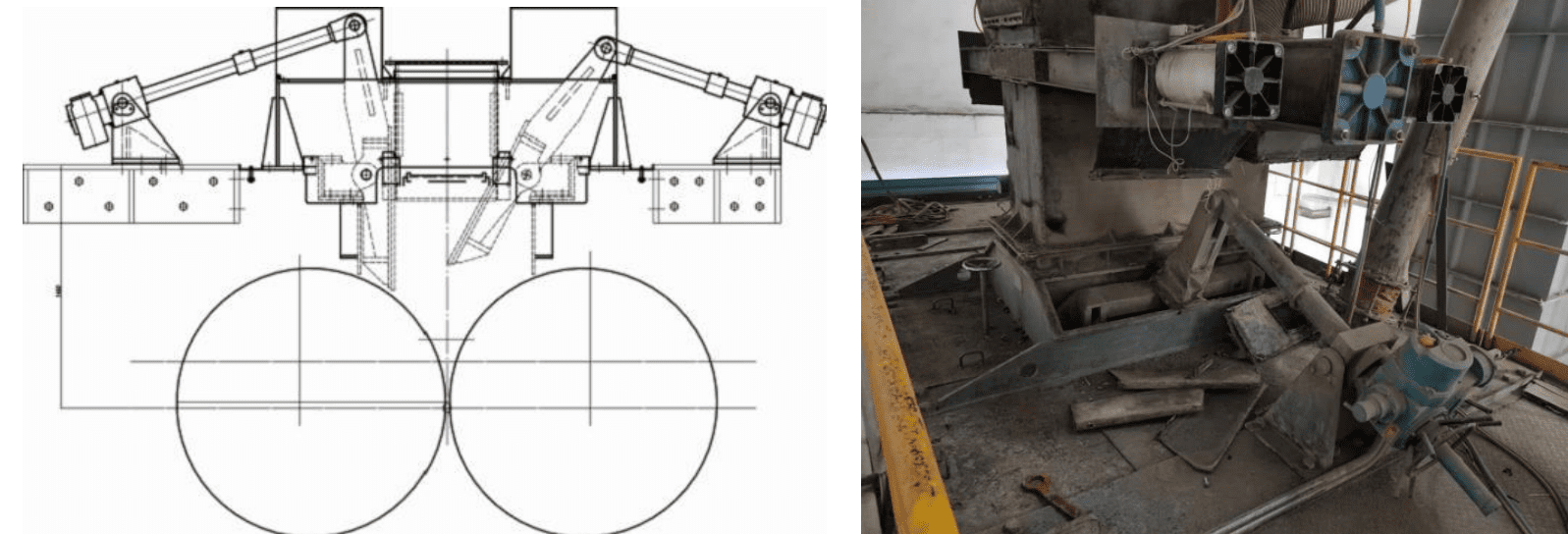
V.План модификации системы роликового пресса
1. Замена устройства для кормления
Замените подающее устройство роликового пресса на новый тип системы подачи в четырех направлениях (запатентованная технология) для управления подачей материала. Эта система позволяет регулировать и контролировать подачу материала в двух направлениях, обеспечивая разумный контроль. Два других направления могут быть отрегулированы для устранения бокового отклонения зазора между роликами, что уменьшает воздействие материала на роликовый пресс и способствует формированию стабильного слоя материала. Такой подход устраняет такие проблемы, как сегрегация материала и несоосность вальцов, и работает при низком положении бункера, что облегчает регулировку и контроль.
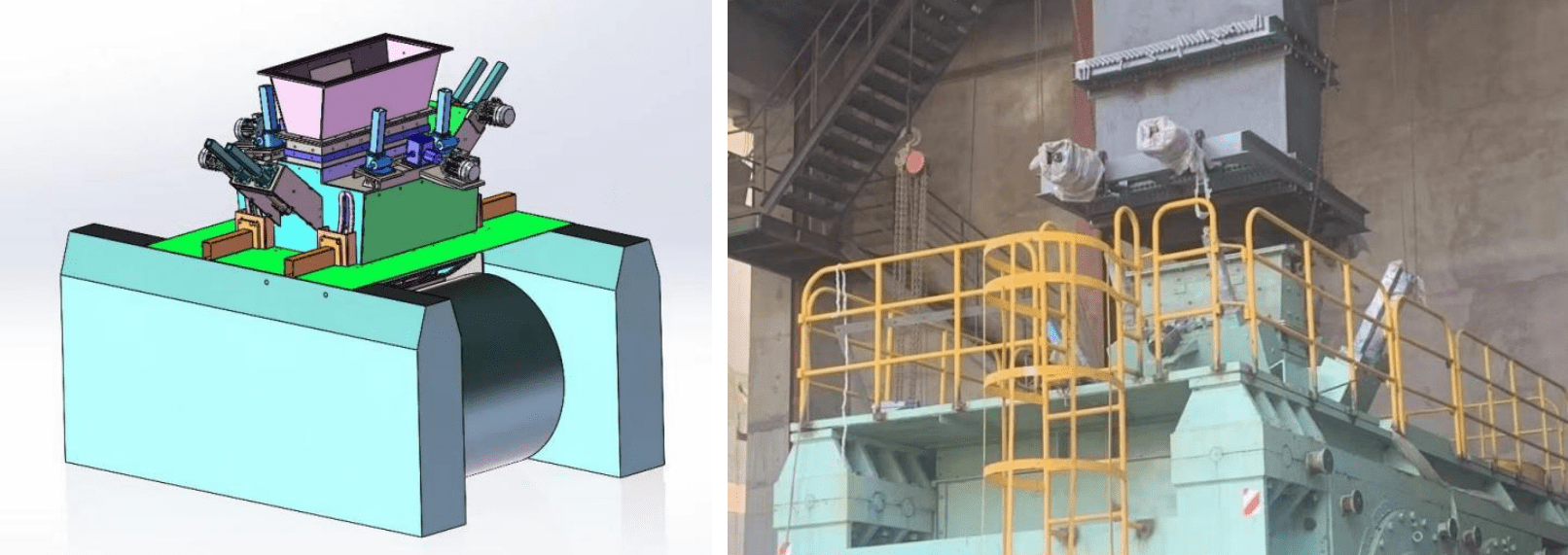
2. Модернизация гидравлической системы
Мы заменили гидравлическую систему вальцового пресса, включая такие компоненты, как маслостанция, переливной клапан, манометр, аккумулятор (азотный мешок) и клапан в сборе. Кроме того, мы установили клапаны регулировки демпфирования и клапаны регулировки хода (запатентованная технология), чтобы сделать гидравлическую систему гибкой, жесткой и управляемой.
В процессе исследований и разработок мы провели обширные полевые испытания с использованием специализированного высокоточного прибора для измерения давления (1000 Гц) для сбора и анализа данных. Мы использовали специализированное программное обеспечение для моделирования и сложные математические модели, чтобы успешно разработать двухканальный регулируемый демпфирующий антивибрационный механизм регулирования, добившись разумного баланса жесткости и гибкости гидравлической системы.
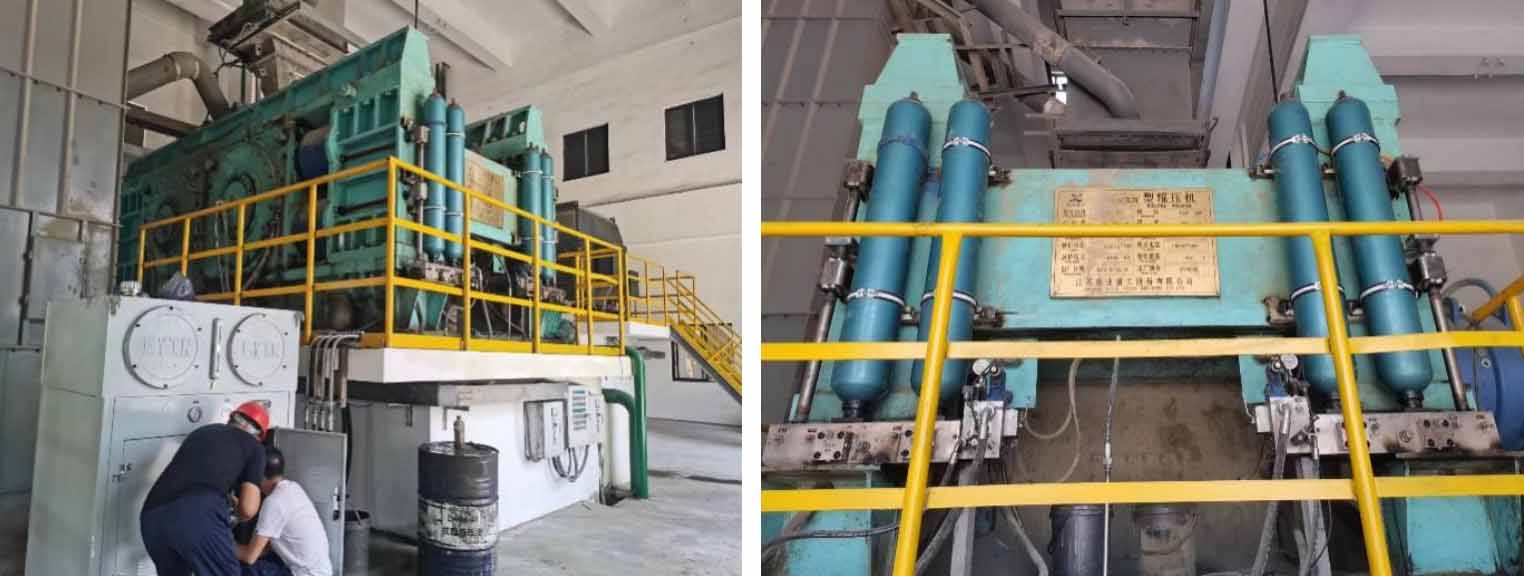
3. Реализация управления с помощью ПЛК
Мы заменили гидравлический ПЛК роликового пресса и внедрили четырехнаправленное управление подающим устройством, используя метод управления постоянной мощностью для упрощения централизованного управления. Мы сконфигурировали систему с Siemens SIMATIC S7-1200, интегрировав в нее приводные устройства Siemens SINAMICS и продукты SIMATIC для человеко-машинного интерфейса. В стандартную комплектацию процессора входит интерфейс Ethernet, поддерживающий различные промышленные протоколы связи Ethernet, включая PROFINET, TCP, UDP и Modbus TCP.
Наша компания разработала эту технологию с помощью математического моделирования, собрав обширные полевые данные в процессе исследований и разработок. Мы использовали специализированное программное обеспечение для моделирования и сложные математические модели, которые были подтверждены практическим применением.
VI.Тематические исследования
1. Чао Лейк Хэнсин Цемент Лтд.
После внесения изменений в августе 2020 года эффективность производства выросла с 200 тонн/час до 290 тонн/час, а потребление энергии контролируется на уровне 22 кВт-ч на тонну цемента.
2. Хайнань Хуарен Цемент
В июне 2022 года был модернизирован валковый пресс, что позволило увеличить часовую производительность со 150-160 тонн до 180-200 тонн, а потребление энергии сократилось примерно до 23 кВтч/тонну.
3. Юго-запад Гуйчжоу
Благодаря модернизации производительность выросла до 180-190 тонн в час, а потребление энергии снизилось с 32 кВт-ч/тонну до 25 кВт-ч/тонну.
4. Цзянси Саньцин Цемент Лтд.
После модификации производительность увеличилась до 270-280 тонн в час при стабильной работе и поддержании температуры азотного мешка на уровне 40-60°C.
VII.Преимущества модернизации и модификации технологии валковых прессов
- Стабильность роликового пресса улучшилась, практически отсутствуют боковые утечки. Регулировка перекоса роликов осуществляется тремя способами: первый - регулировка подачи в четырех направлениях; второй - регулировка гидравлической системы; третий - раздельная регулировка давления для левого и правого роликов. Управление стабильное, с минимальными случаями обрушения материала и перекоса роликов.
- Гидравлическая система вальцового пресса гибко регулируется и контролируется. Колебания зазора между роликами изменились с медленного втягивания и быстрого выдвижения на быстрое втягивание и медленное выдвижение, что повысило эффективность прессования. Содержание мелкого порошка на выходе из вальцового пресса увеличилось на 3-7%, улучшилась удельная площадь поверхности исходного материала, а часовая производительность увеличилась на 10-20%.
- Используется метод регулирования постоянной мощности, при котором рабочая мощность поддерживается на уровне 85±5% от номинальной. К эффективности вальцового пресса предъявляются два требования: во-первых, высокая рабочая мощность; во-вторых, высокий выход первого прохода. Повышение эффективности вальцового пресса и снижение энергопотребления мельницы позволило снизить общее энергопотребление на 2-5 кВт-ч/тонну.
Если у вас есть потребности в модификации и модернизации систем роликовых прессов, пожалуйста, обращайтесь к нам. связаться с нами на Дарко. Мы предоставим вам профессиональные решения и поддержку.