Star discharge valves are key devices in powder conveying systems. Their stable operation is crucial for production efficiency. Here are ten common problems to avoid during use, along with their solutions:
1.Incorrect Selection
Choosing the wrong model may lead to the star discharge valve not meeting actual needs. Evaluate material characteristics such as particle size, moisture content, flowability, handling capacity, and working pressure when selecting the appropriate model and specifications. Incorrect selection can cause overloading, low efficiency, or frequent failures.
2.Material Blockage
Material accumulation or blockage inside the star discharge valve is a common issue. Materials with high moisture, high viscosity, or high fiber content easily adhere to the blades or housing. To prevent blockage, consider using heating, vibration, or installing cleaning devices to maintain material flow.
3.Seal Failure
Worn or damaged seals can lead to dust leakage, which pollutes the environment and poses safety risks. Regularly check seals and replace worn parts promptly. Ensure that the sealing structure is designed reasonably to maintain a good sealing effect.
4.Insufficient Lubrication
Lack of lubrication can increase wear on bearings and drive components, shortening the life of the star discharge valve. Regularly inspect the lubrication system to ensure that oil or grease is sufficient and clean, preventing failures due to inadequate lubrication.
5.Foreign Object Ingress
Foreign objects such as metal fragments or stones can enter the star discharge valve and jam the blades or damage the equipment. Install screens or magnetic separators at the feed inlet to prevent foreign objects from mixing in and ensure normal operation.
6.Overloading
Running the star discharge valve at overload for extended periods can cause motor overheating, bearing damage, or even equipment shutdown. Control the feed rate according to the rated handling capacity to avoid overload and ensure safe and stable operation.
7.Blade Wear
Excessive blade wear affects discharge efficiency, leading to larger gaps and decreased sealing performance. Regularly check blade wear and repair or replace them promptly to maintain efficient operation.
8.Improper Installation
Incorrect installation may result in excessive vibration or noise. Ensure that the star discharge valve is level, stable, and tightly connected to the piping during installation to improve operational stability.
9.Inadequate Maintenance
Insufficient maintenance can lead to frequent equipment failures. Establish a regular maintenance schedule that includes cleaning, lubrication, and tightening bolts to effectively extend the lifespan of the star discharge valve and feeders, reducing failure risks.
1O.perational Errors
Improper operation can cause equipment failures or safety incidents. Operators should be familiar with the performance of the star discharge valve and feeders and strictly follow operational procedures to avoid damage from operational mistakes.
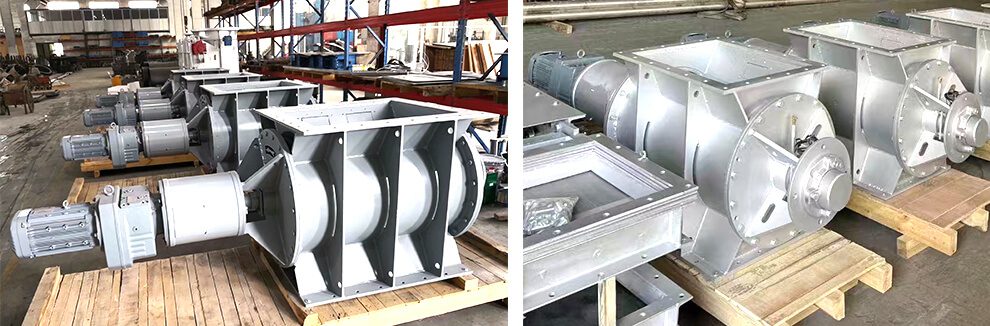
Summary
Maintaining stable operation of star discharge valves requires careful attention to selection, installation, operation, and maintenance. By avoiding the above ten problems, you can effectively extend the equipment’s life, improve production efficiency, and reduce operating costs. Ensure efficient operation of the star discharge valve and feeders to provide reliable support for production.
For further inquiries about star discharge valves and feeders, please feel free to contact us. We are committed to providing you with support and services.