Rotary valves are essential equipment in industrial applications, widely used in cement, food processing, chemical, and other industries.
A rotary feeder valve operates by using a motor and reducer to rotate an evenly divided impeller inside its housing. Material from the upper hopper or feeding device fills the impeller’s chambers and is discharged at the bottom as the impeller turns.This makes sure the system keeps getting material smoothly and without interruptions.
This guide answers key questions about rotary valves, including their applications, functions, differences from linear valves, and the role of rotary feeders.
1. What Is a Rotary Valve Used For?
Rotary valves primarily control bulk material flow while maintaining airtightness in pneumatic conveying systems. Common applications include:
Cement Industry: Precisely regulates cement flow in bulk loading systems.
Food Processing: Handles powdery materials like flour and sugar without dust emission.
Chemical Industry: Transfers powdered or granular chemicals with leak-proof performance.
Environmental Systems: Works with dust collectors to maintain negative pressure.
Key advantages: High efficiency, low maintenance, and minimized dust pollution.
2. What Is the Function of a Rotary Control Valve?
A rotary control valve not only manages material flow but also adjusts flow rate and pressure. Core functions include:
Precise Metering: Controls discharge volume by adjusting rotor speed.
Airlock Function: Prevents airflow backflow and stabilizes system pressure.
Automation Integration: Connects with PLC systems for smart control.
Example: In cement bulk loading systems, rotary control valves prevent dust leakage while improving loading efficiency.
3. Key Features of Rotary Valves
Simple structure, easy maintenance; handles material temperatures from 0–300°C.
Speed adjustable via frequency converter for flexible feed control.
Stable discharge rate, even with material property changes.
Good airtightness; slow rotation minimizes material damage.
4. What Is the Difference Between a Rotary Valve and a Linear Valve?
The main differences lie in motion type and applications:
Aspect | Rotary Valve | Linear Valve |
---|---|---|
Motion | Rotating impeller | Linear movement (up/down) |
Materials | Powders, granules | Liquids, gases, viscous media |
Sealing | Depends on rotor-housing gap | Higher (e.g., gate valves) |
Maintenance | Regular wear inspection | Frequent seal replacement |
Rotary valves excel in bulk material handling, while linear valves suit liquid/gas control.
5. What Is the Purpose of a Rotary Feeder?
A rotary feeder (a specialized rotary valve) ensures:
Uniform Feeding: Steady material flow into conveying pipelines.
Clog Prevention: Impeller rotation avoids material buildup.
Energy Efficiency: Reduces power consumption.
Applications:
Cement plants: Transfers cement from silos to bulk trucks.
Food factories: Precisely doses ingredients into mixers.
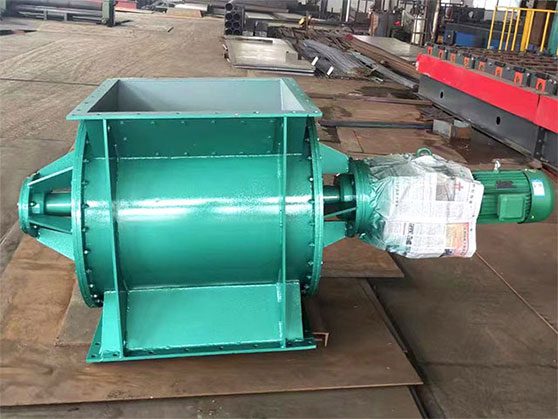
6. How to Select the Right Rotary Valve?
Consider these factors:
Material Properties: Particle size, abrasiveness (e.g., wear-resistant design for cement).
Flow Requirements: Valve size based on capacity needs.
Sealing Standards: Explosion-proof or food-grade (e.g., stainless steel).
Automation Needs: Variable speed or remote control options.
Conclusion
Rotary valves are really important when working with bulk materials. They help keep things flowing smoothly, prevent leaks, and give you control over the process. Whether for cement, food, or chemicals, choosing the right valve boosts productivity and cuts costs.